В тот день, когда я узнал о принципе работы безлопастного вентилятора, я был поражен тем, какая простая и крутая идея стоит за этим устройством.
В тот же день я решил соорудить один для моего племянника, чтобы он не поранился, прохлаждаясь в жаркие летние дни.
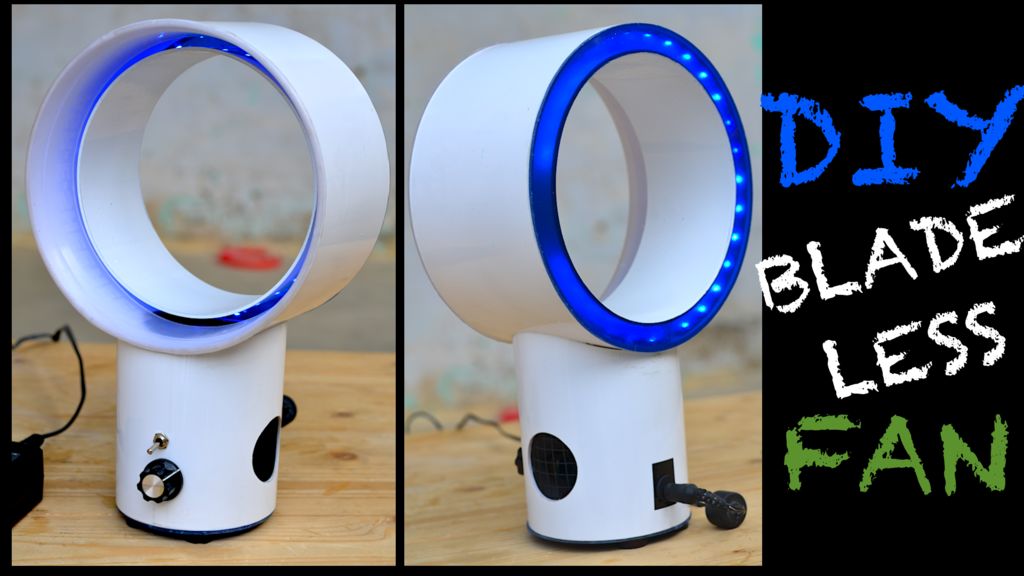
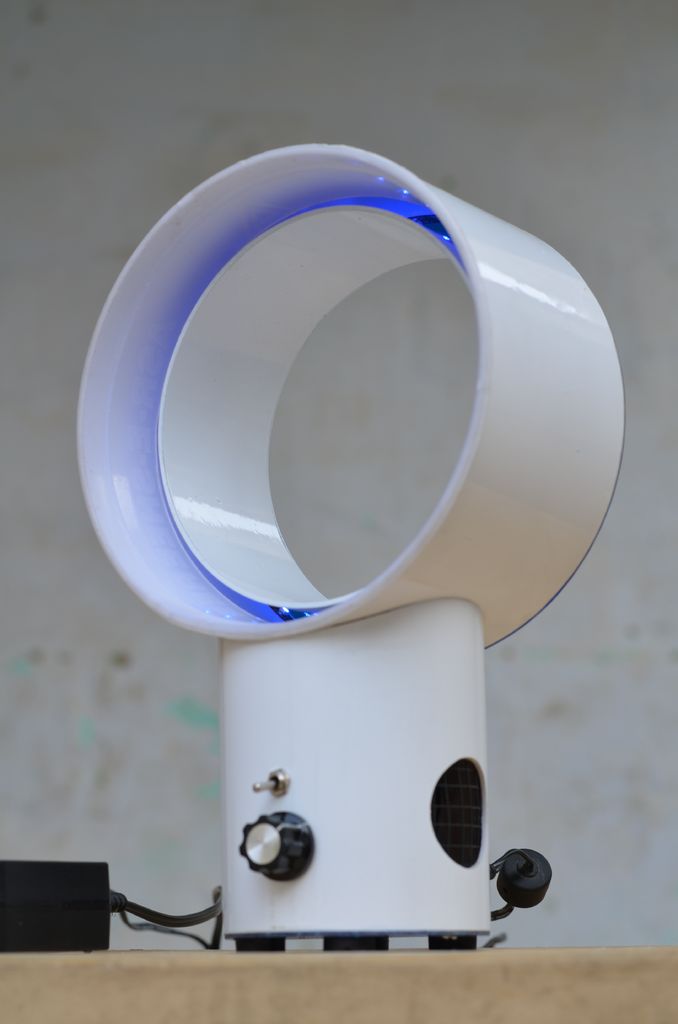
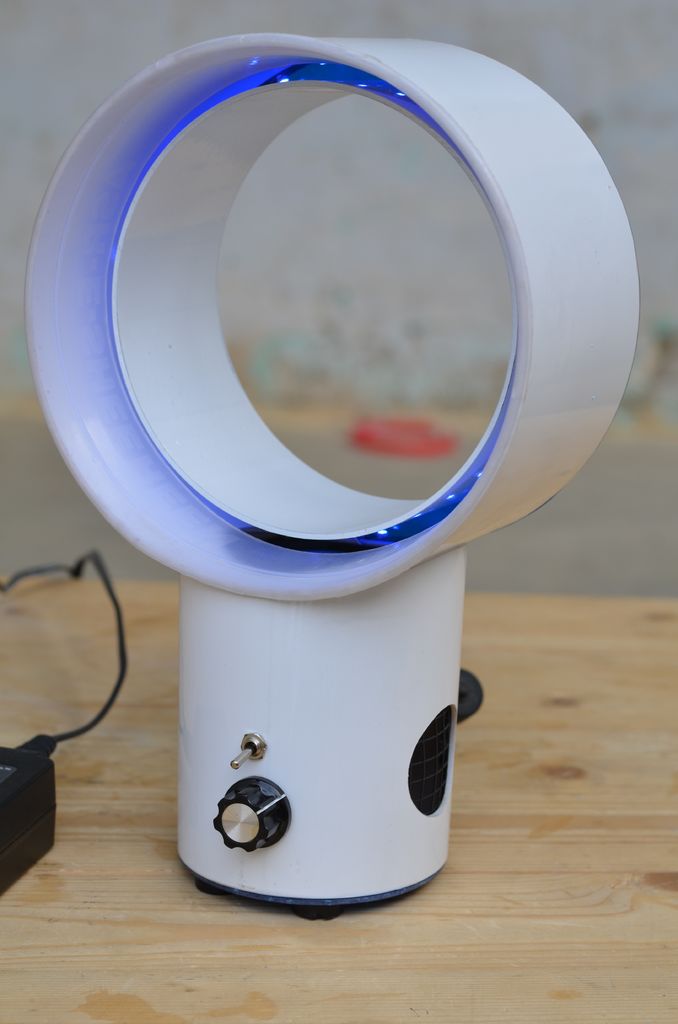
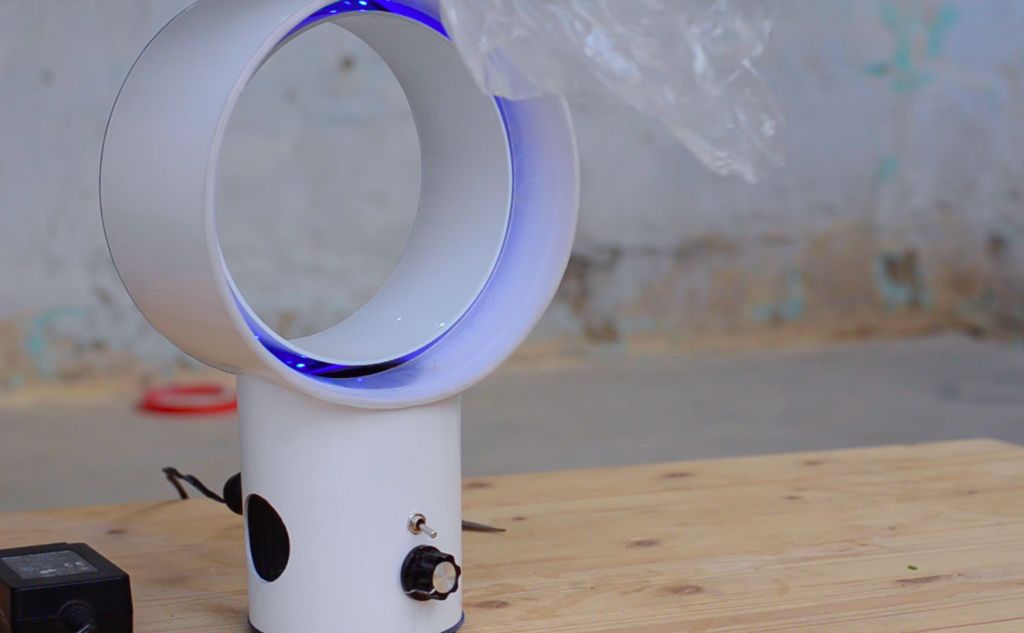
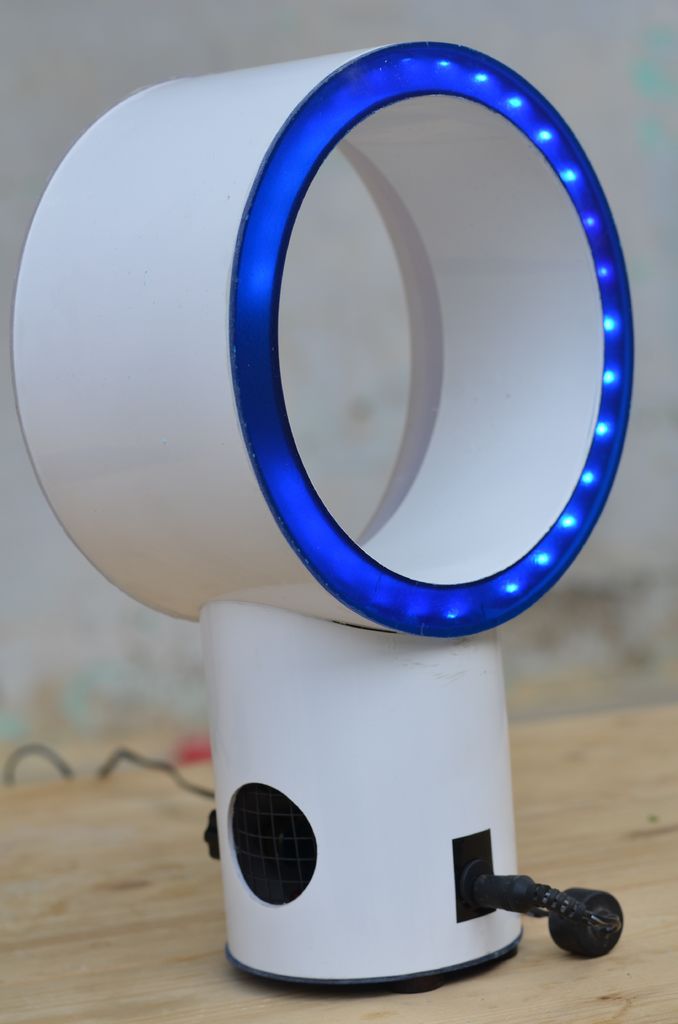
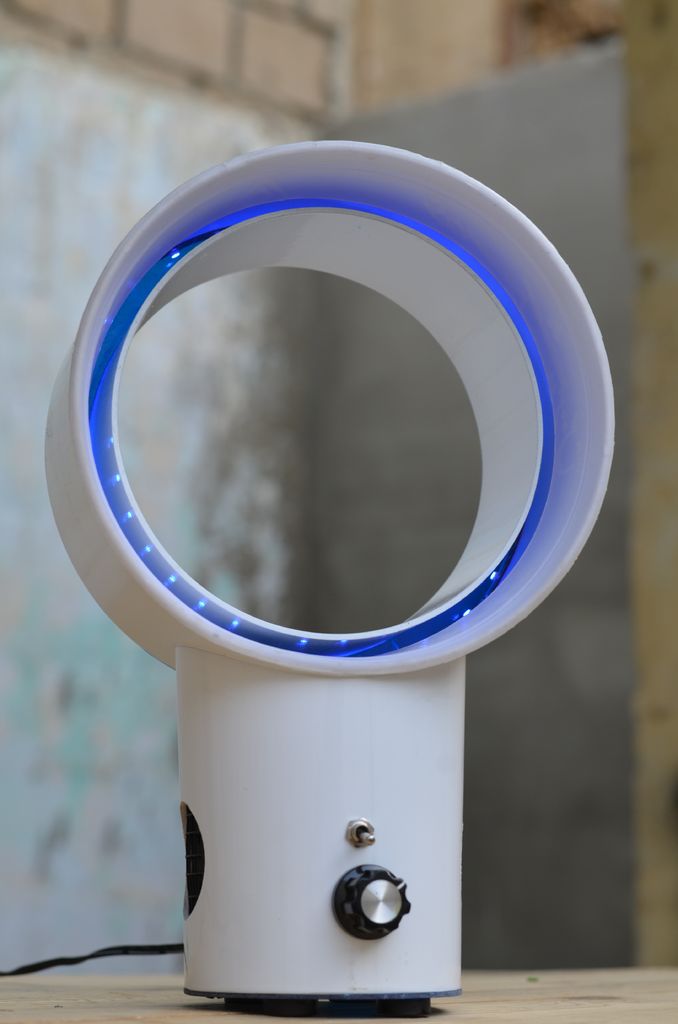
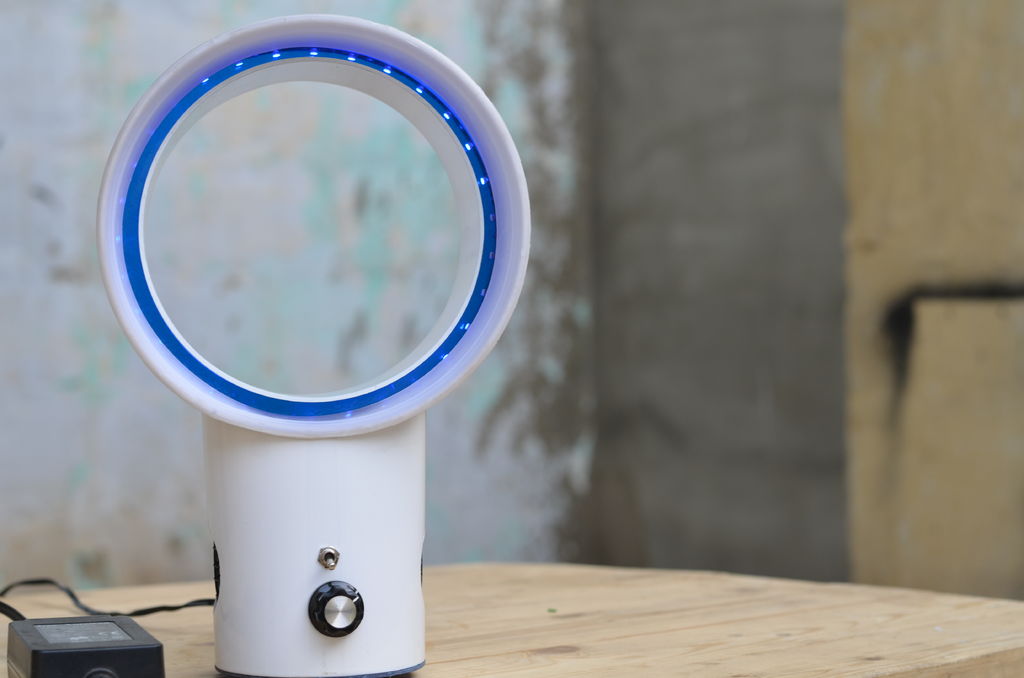
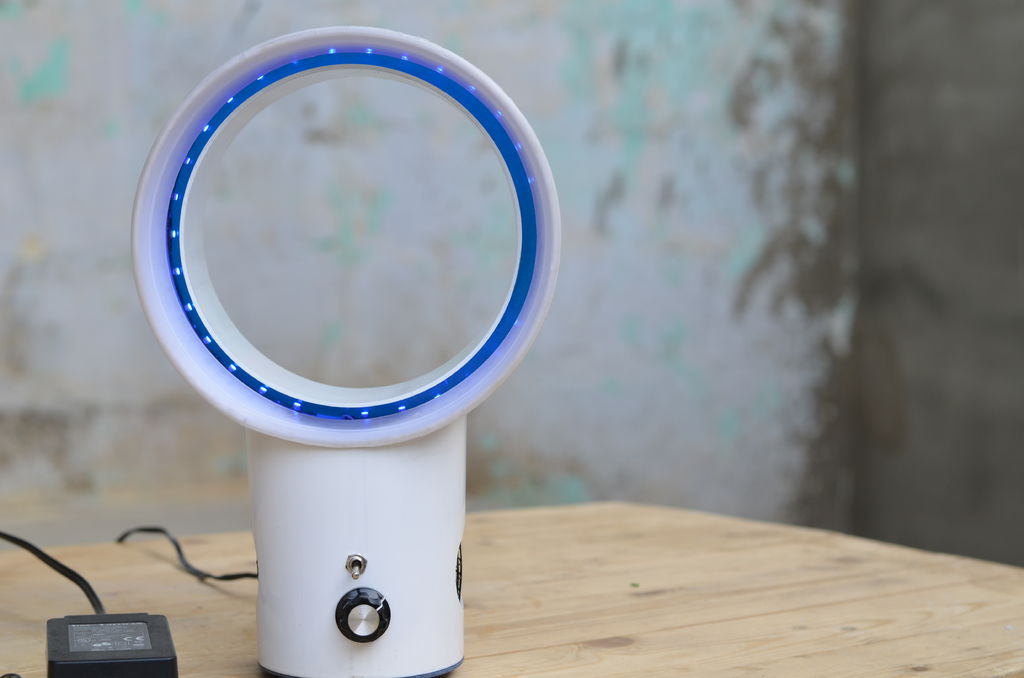
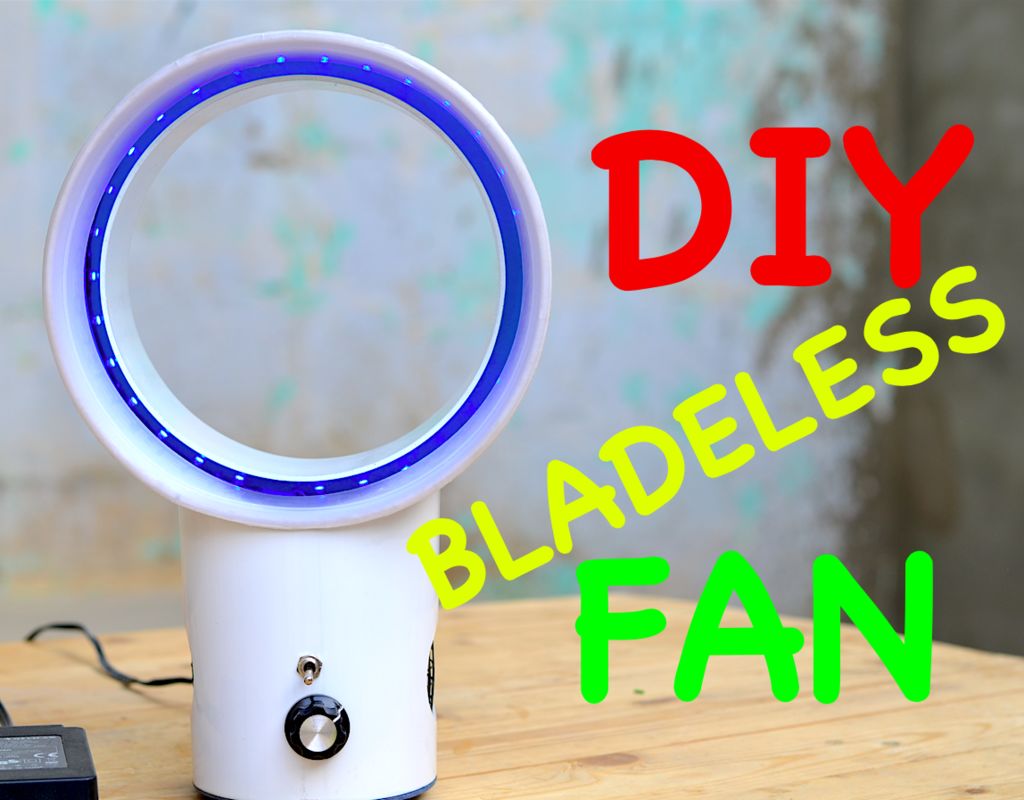
Итак, в этой инструкции я собираюсь собрать безлопастной вентилятор своими руками, используя обычные материалы, такие как пара ПВХ трубок, пластиковая чашка и пара листов фибергласа. Самой крутой особенностью этого вентилятора, в отличии от остальных самодельных безлопастных вентиляторов, является то, что я собираюсь сделать этот проект доступным каждому, без нужды печатать какие-либо его части на 3Д принтере. Это также делает проект очень дешевым — не более $10.
Содержание статьи
Шаг 1: Необходимые материалы и оборудование
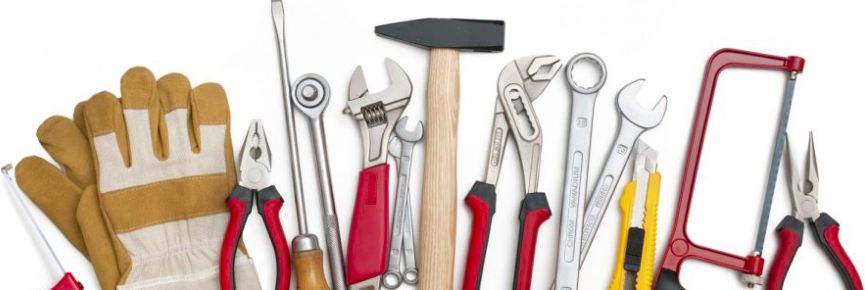
Приспособления и материалы для этого проекта легко найти. Нам нужна пара ПВХ трубок на 6,5 и 3,5 дюйма в диаметре, пластиковая чаша, лист фибергласа толщиной 3мм и т.д.
Не надо ничего печатать на 3Д принтере, как это обычно бывает необходимо в других проектах подобного рода. Более того, для большинства распилов я использовал торцовочную пилу, так как она сделала работу более точной и простой, но всё то же самое можно сделать с помощью обычной ножовки и терпения… поэтому для более аккуратного вида вам потребуются более дорогие приспособления.
Шаг 2: Принцип работы

В отличие от своего имени, которое подразумевает, что девайс будет безлопастным, эта штука на самом деле имеет высокоскоростные лопасти внутри своего корпуса.
Кроме того, безлопастной вентилятор обеспечивает скрытую работу лопастей, а создаваемый поток воздуха направляется через замкнутое тело с каналами, которое воспроизводит обычную структуру вентилятора, но без присутствия лопастей. Этот дизайн обеспечивает отличный уровень защиты для детей.
Шаг 3: Изготовление
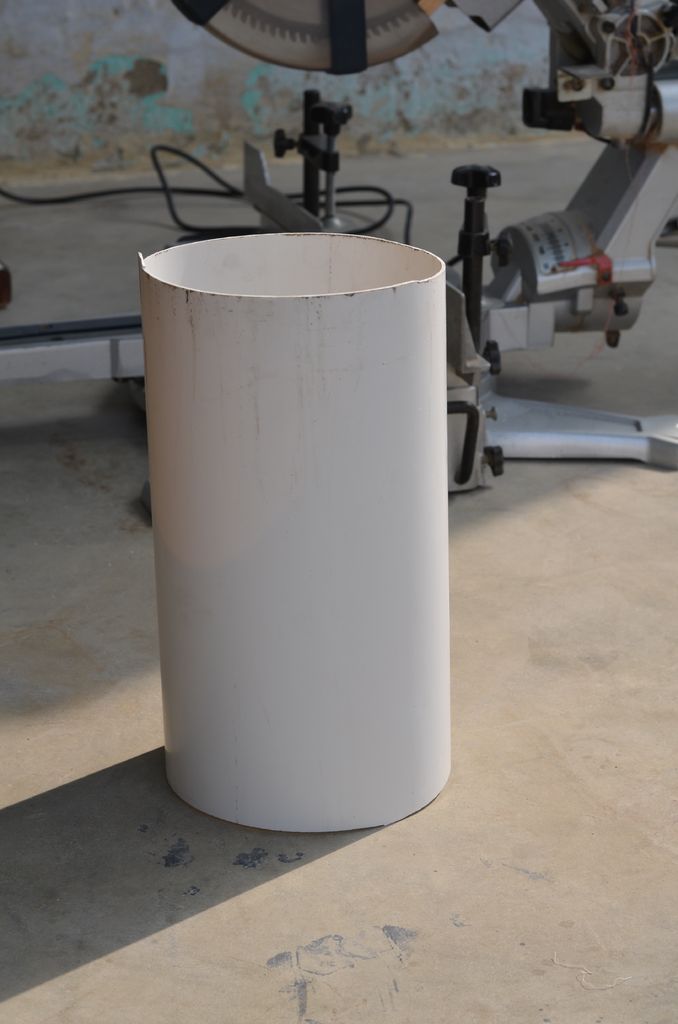
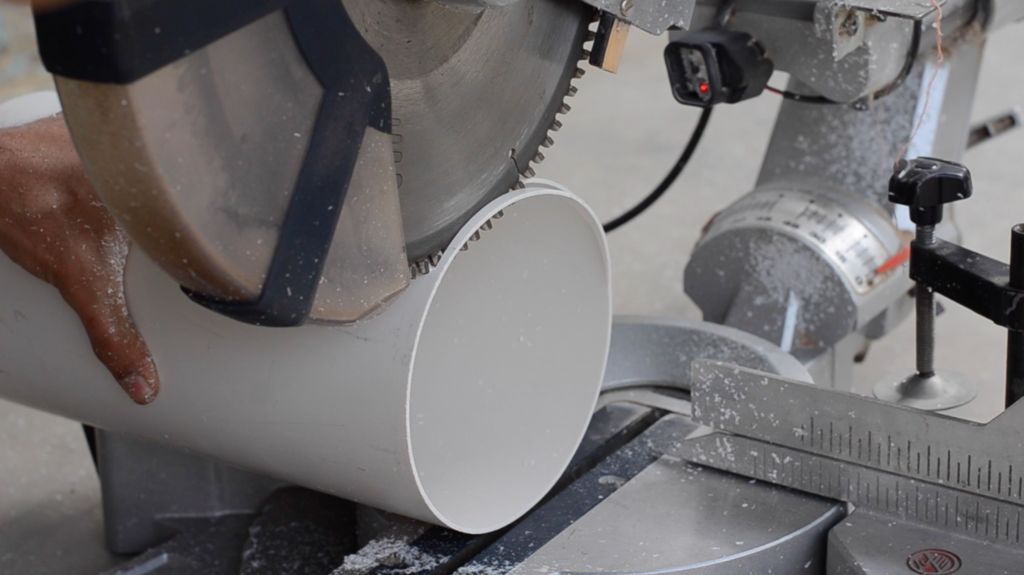
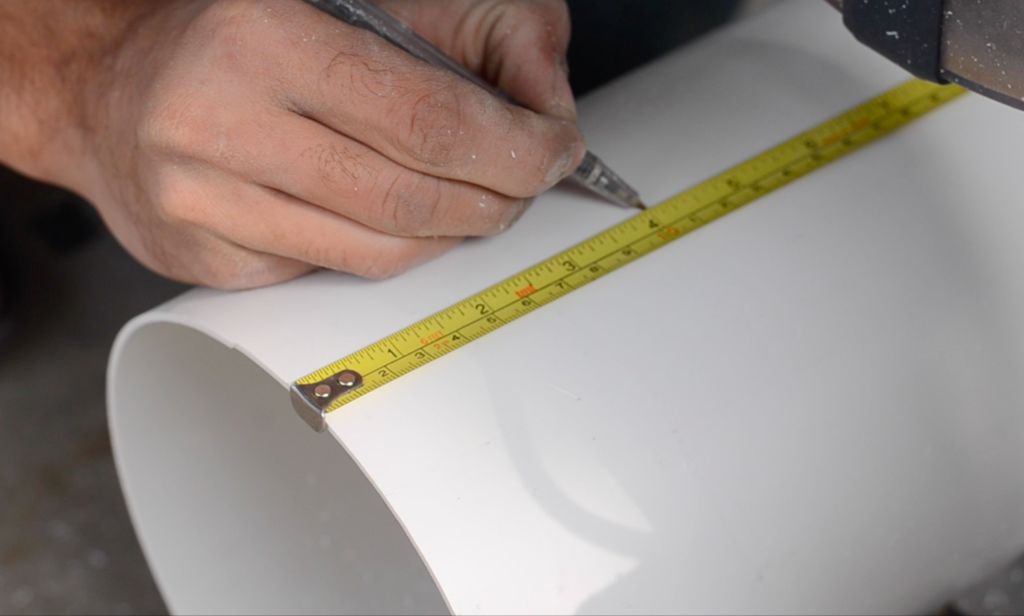
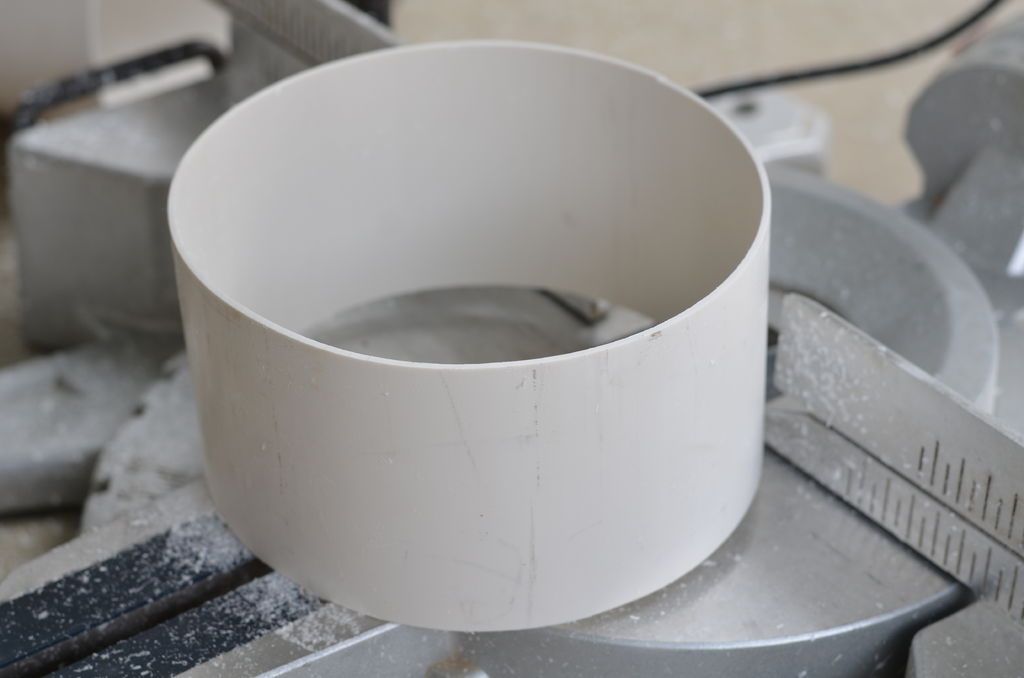
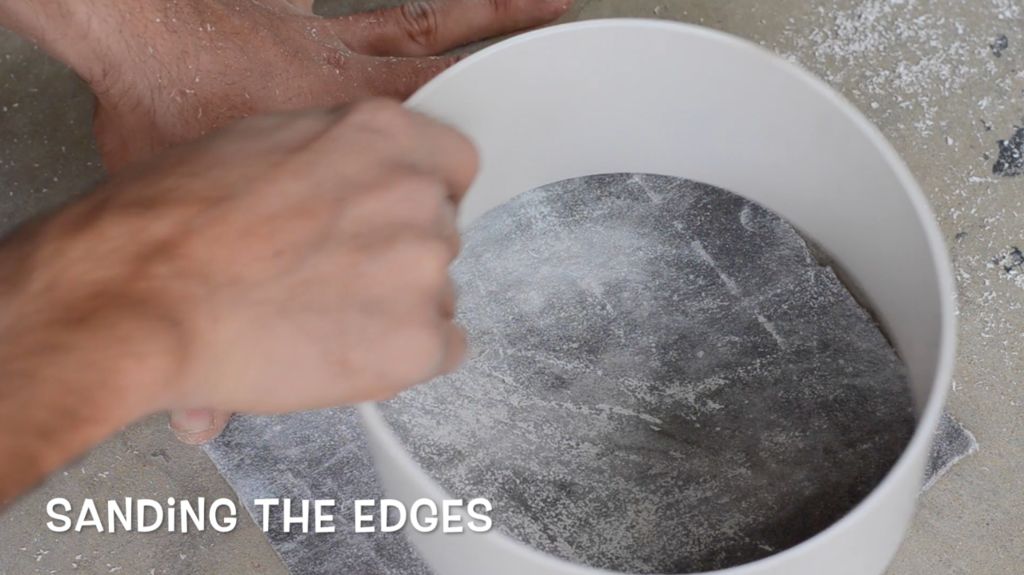
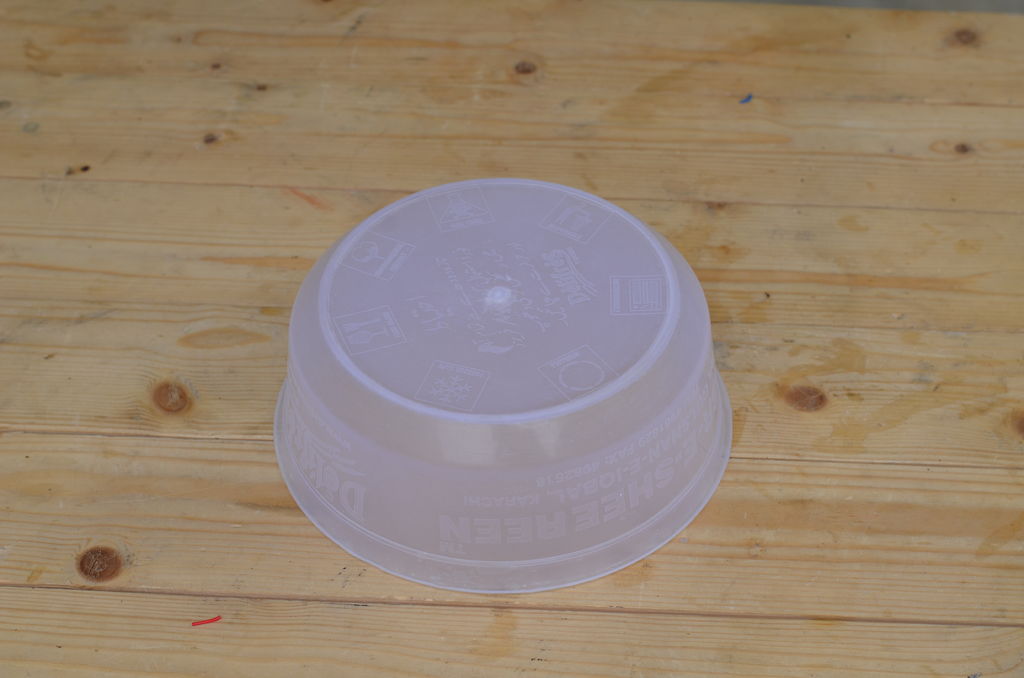
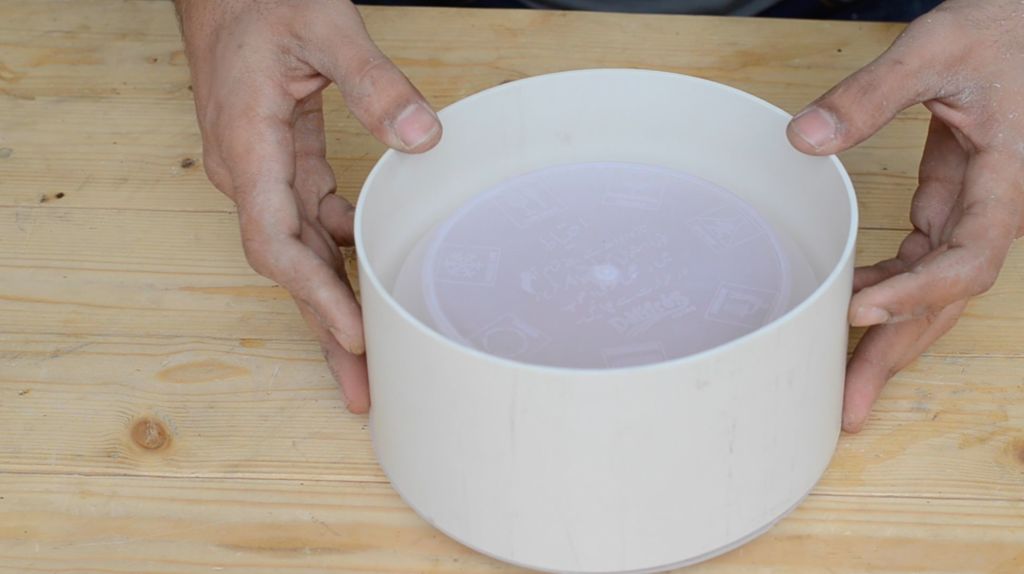
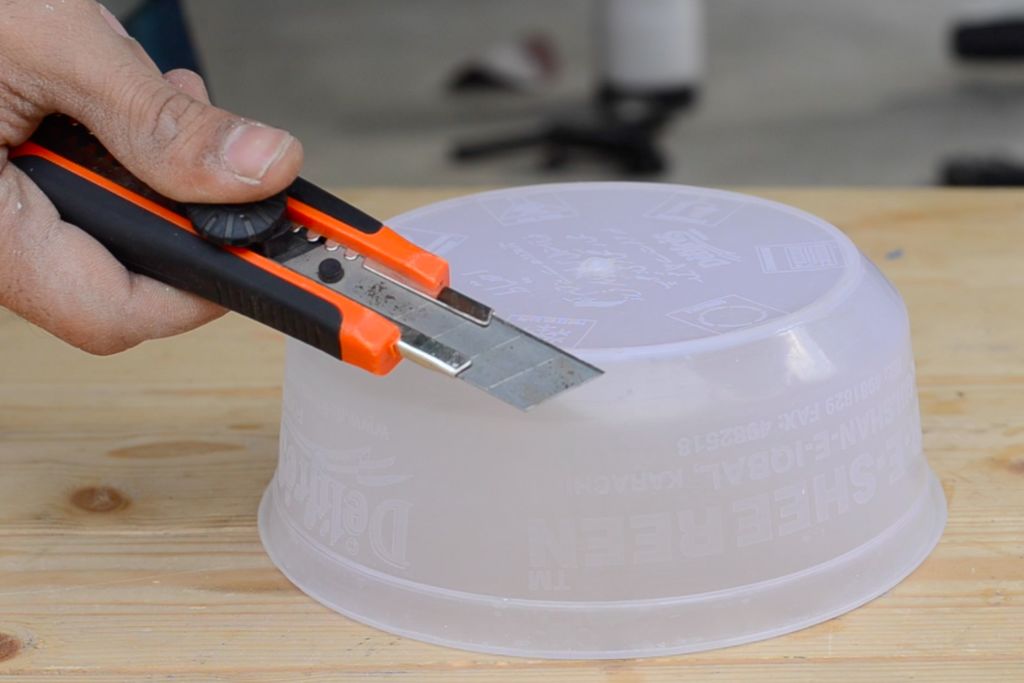
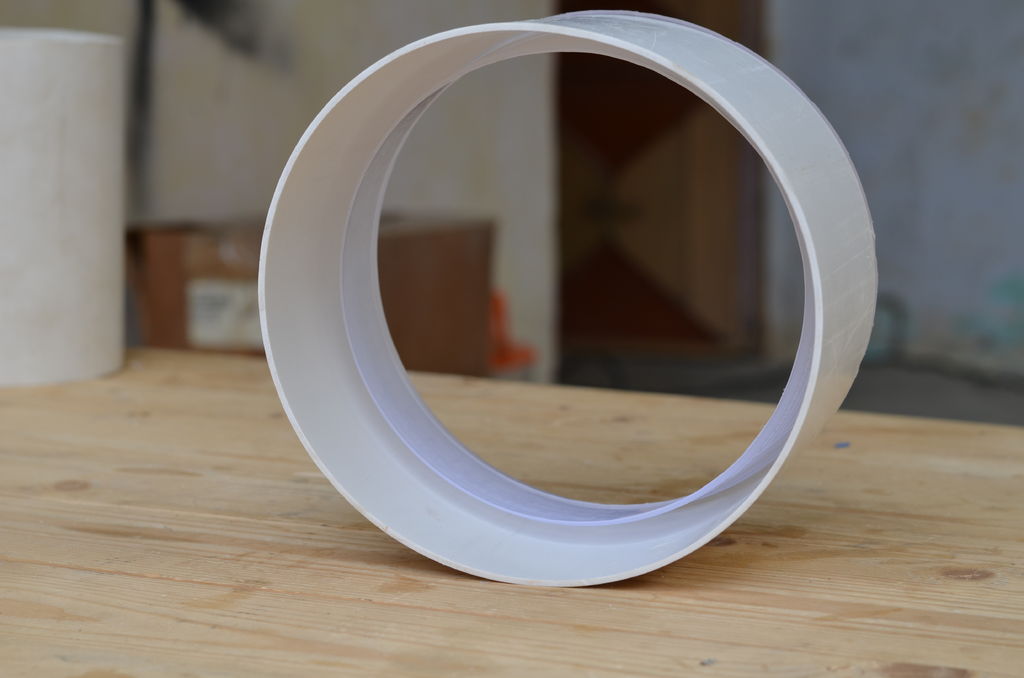
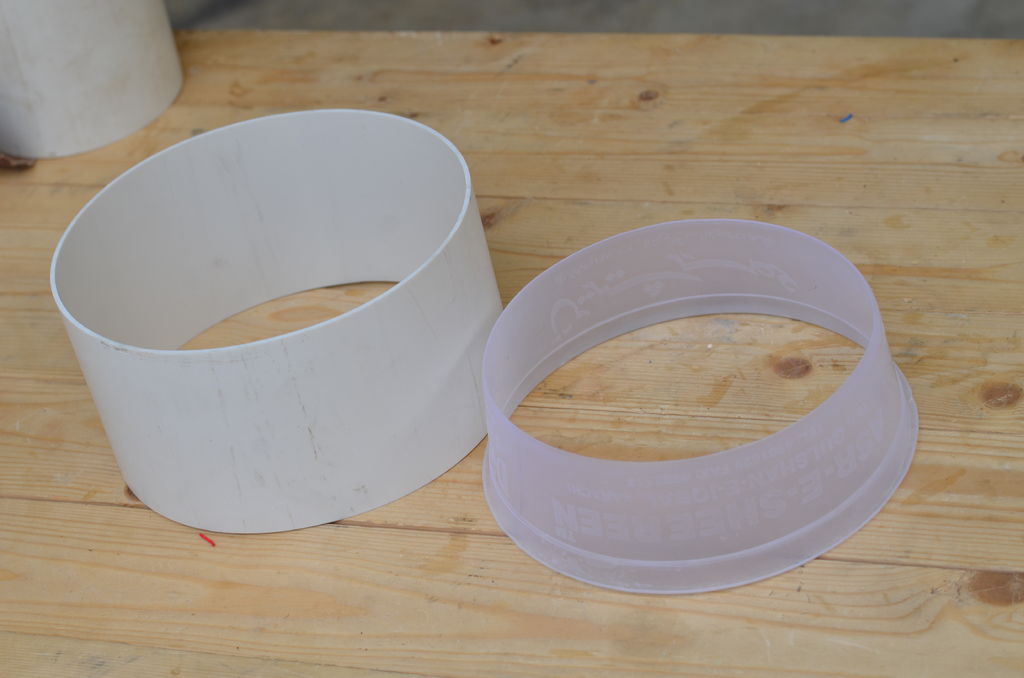
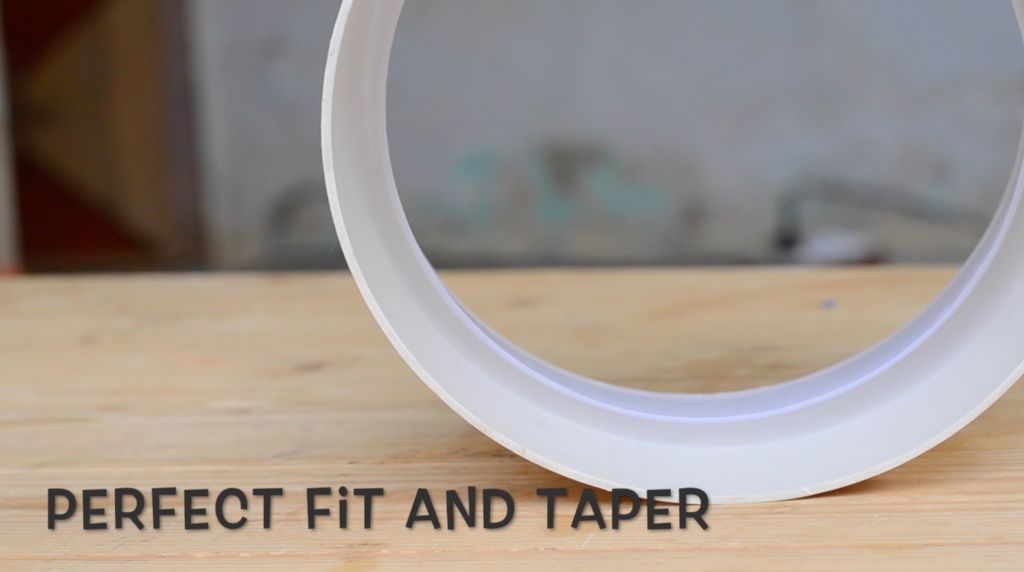
Вначале я собрался изготовить основное тело вентилятора и для этого я использовал трубку ПВХ.
Основная выходная труба изготовлена из ПВХ диаметром 150 мм, он отрезана в ширину на 100мм, образуя наружный корпус воздуховода.
Чтобы сформировать воздушный карман внутри основного воздуховода, я использовал чашу конической формы, которая идеально подошла к 150мм трубке ПВХ, так как её ободок превосходно прижался к ободу трубки. Я отрезал дно чашки примерно на 25мм в высоту и таким образом получил неплохой конический хомут внутри главного воздуховода, который позволяет воздуху равномерно вращаться внутри воздуховода, прежде чем он покидает его.
Шаг 4: Внутренний воздуховод и основание
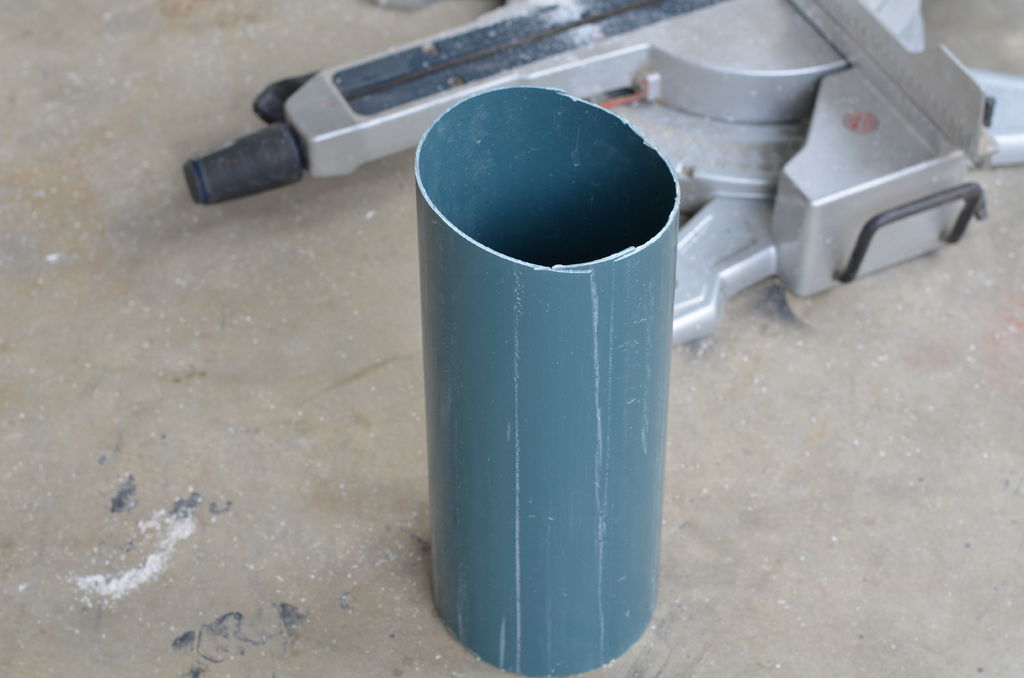
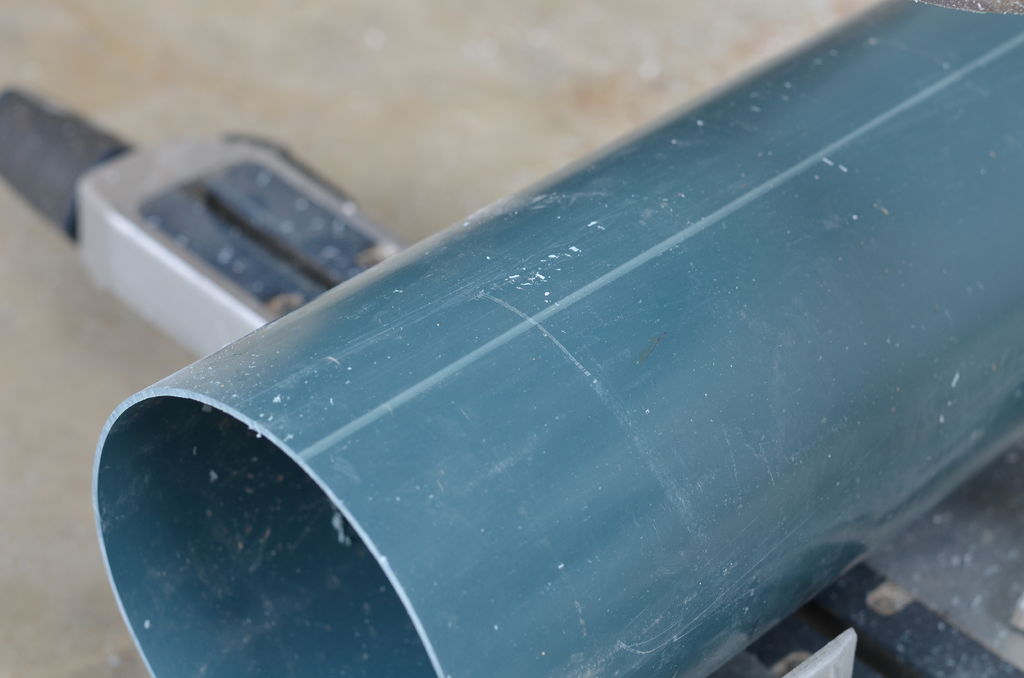
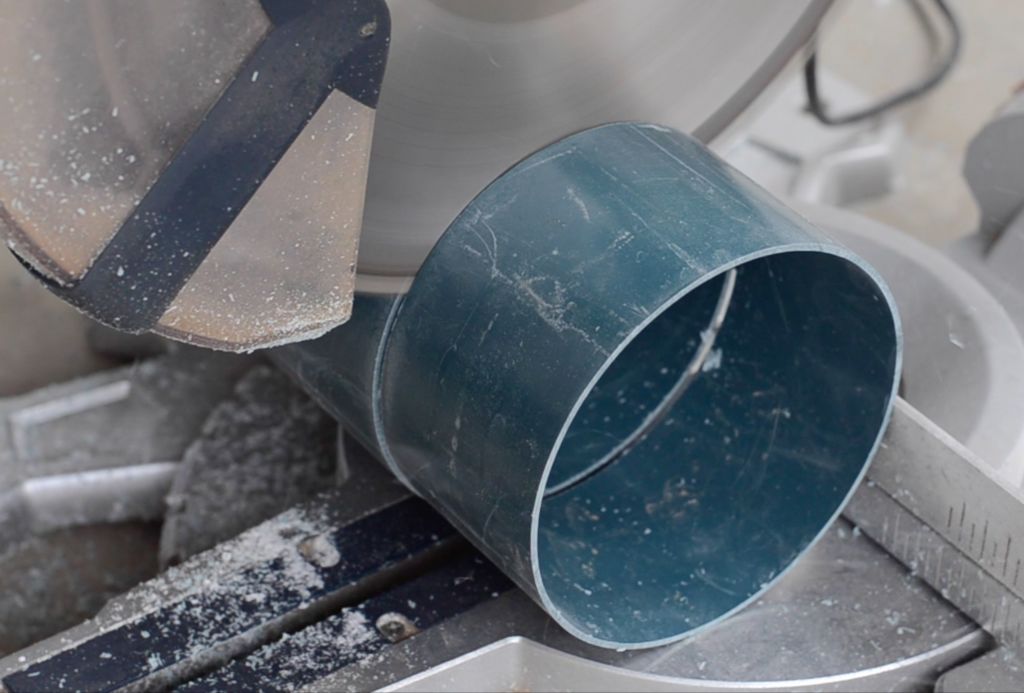
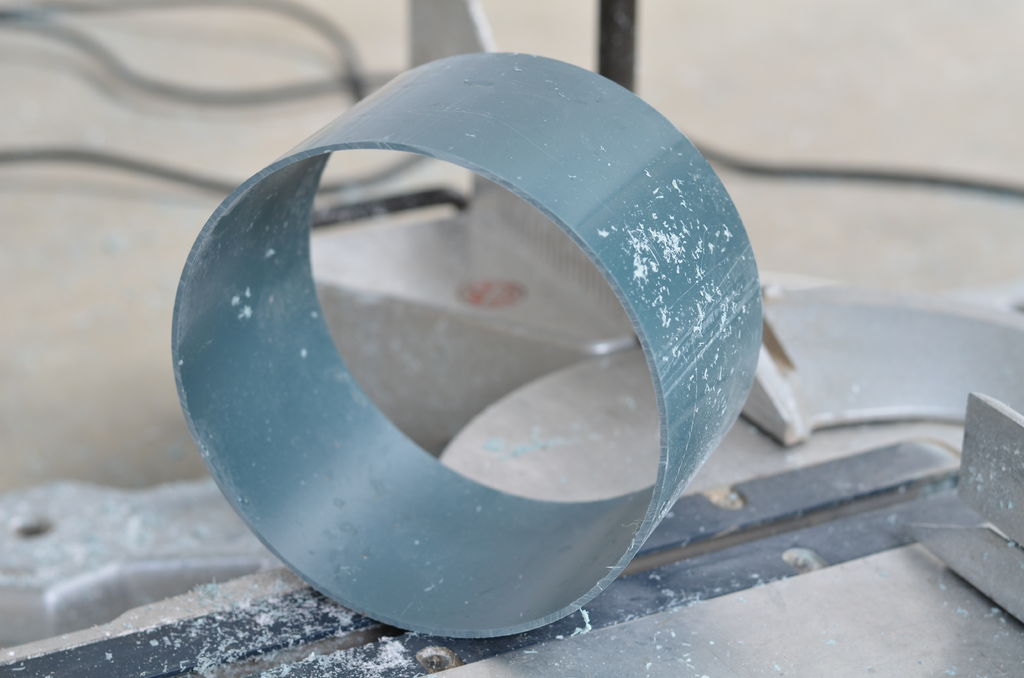
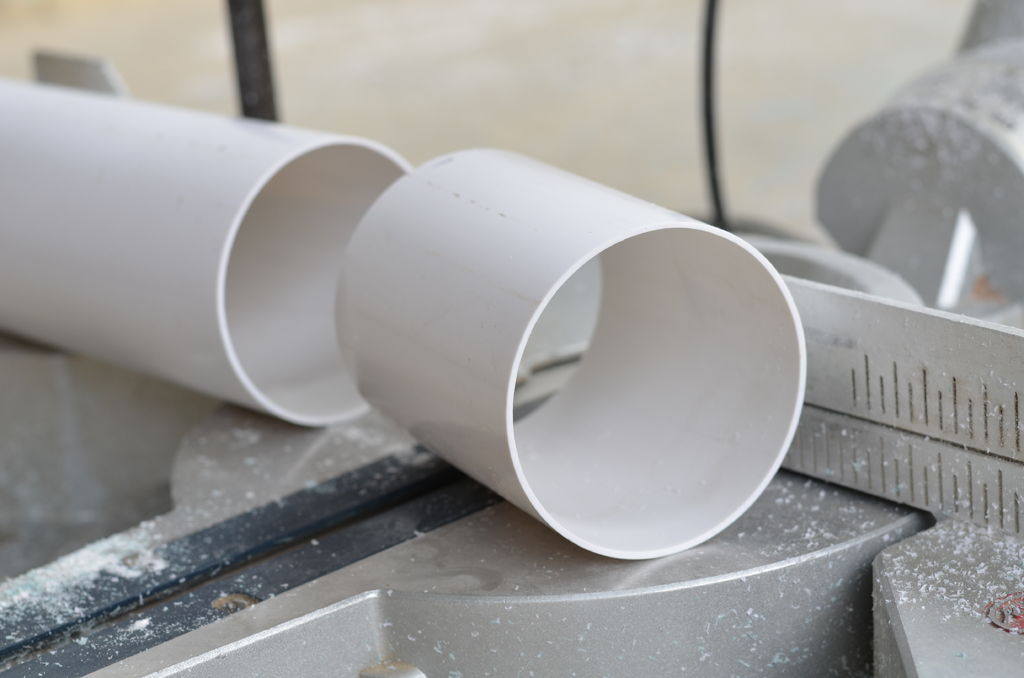
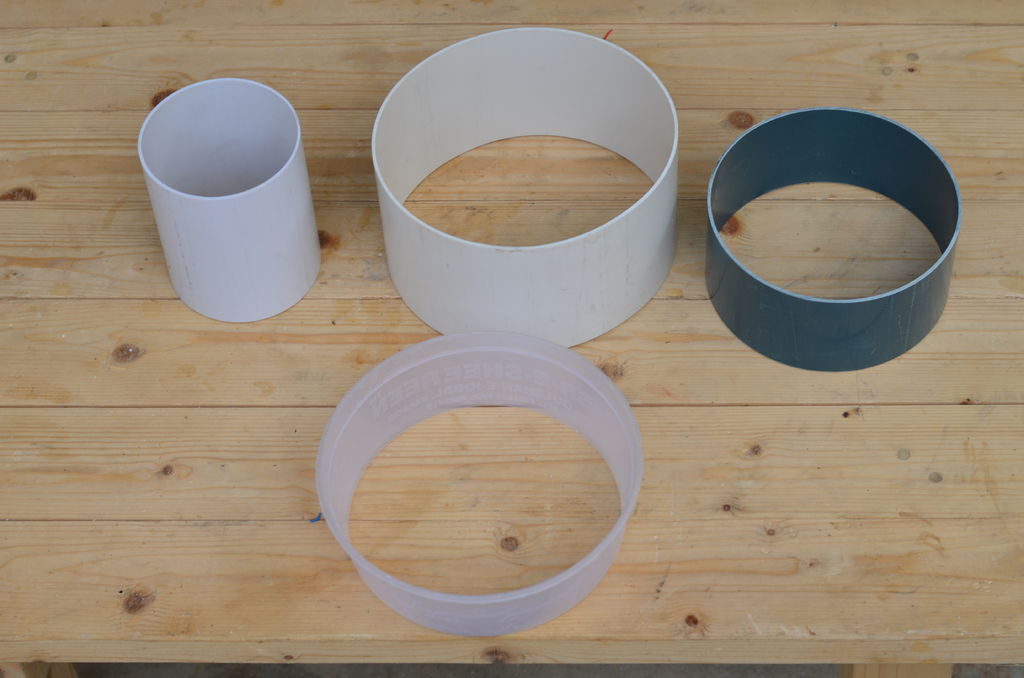
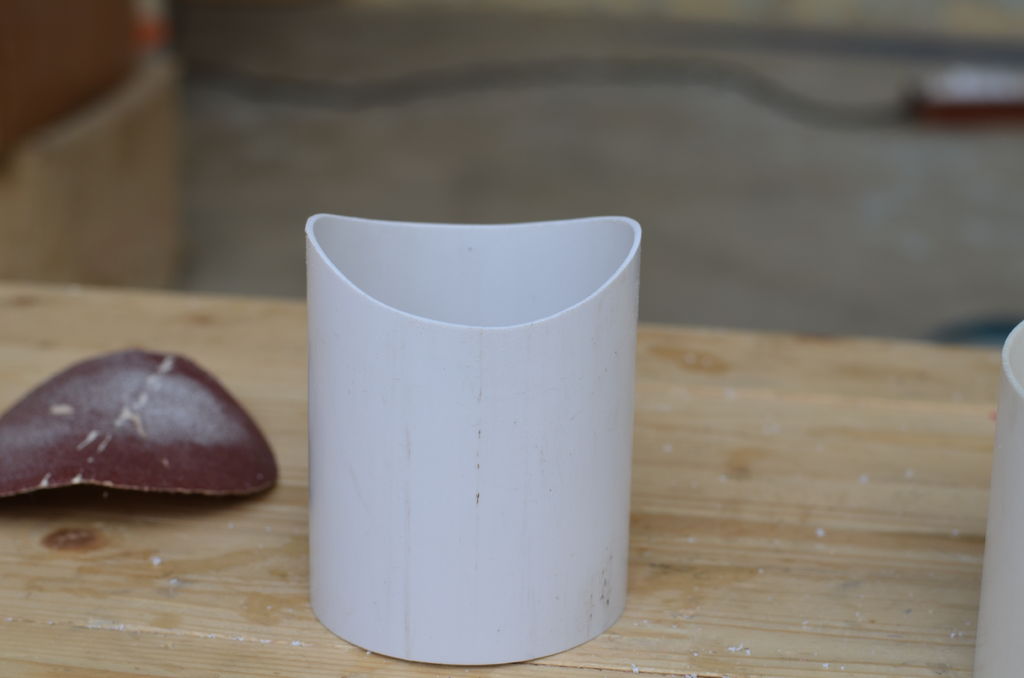
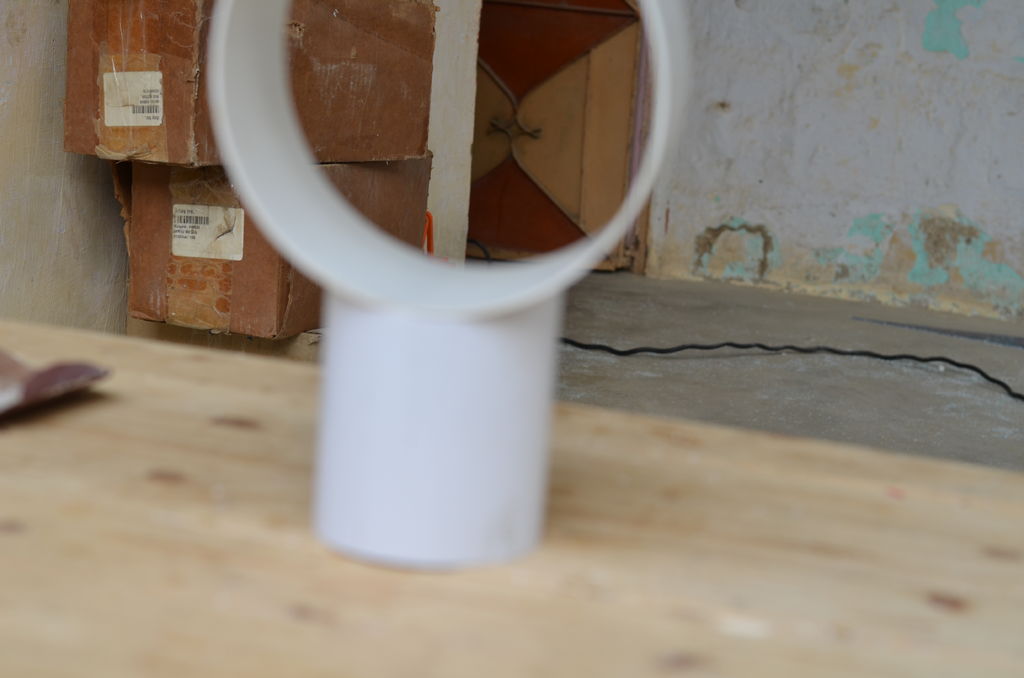
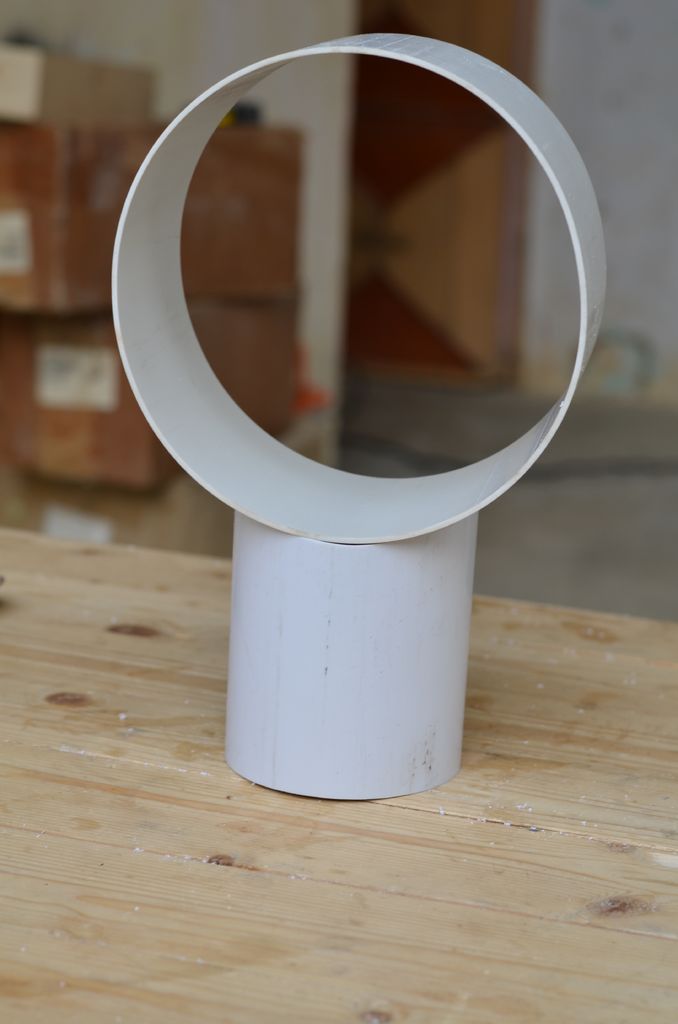

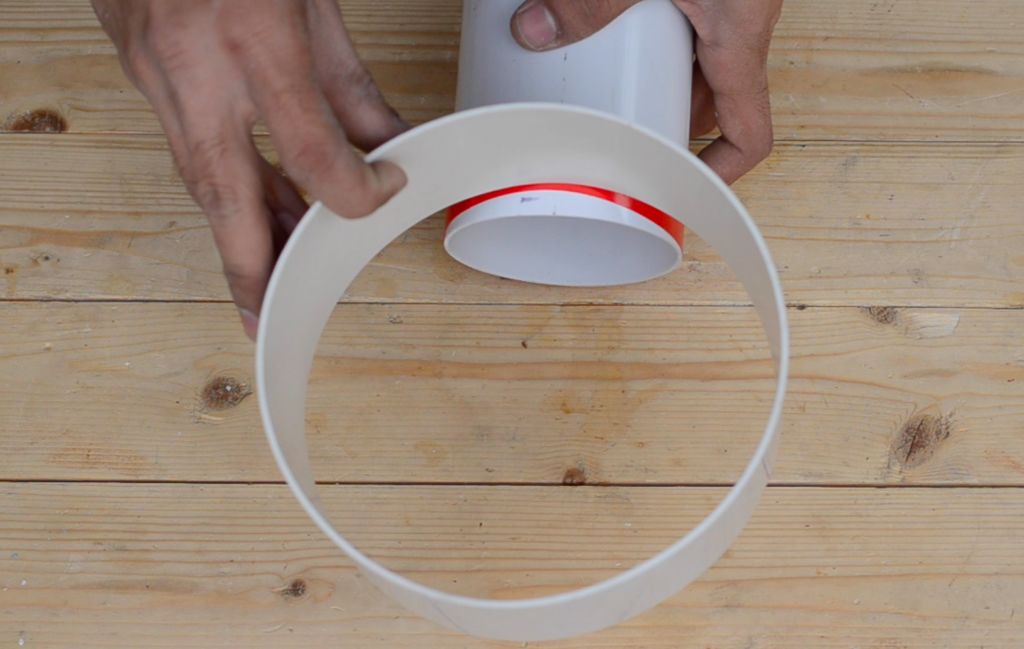
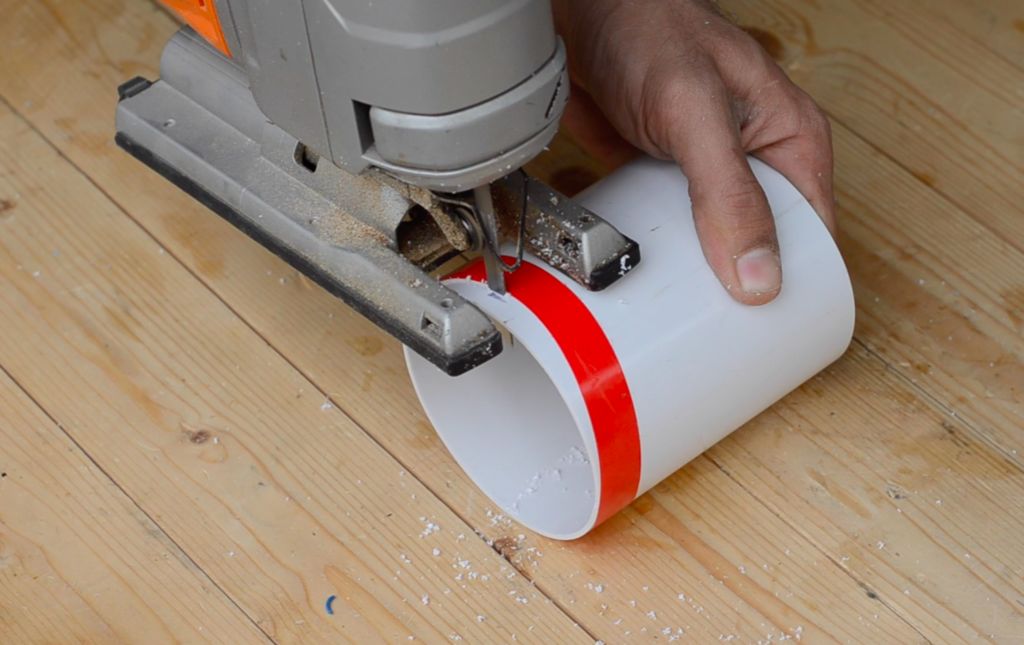
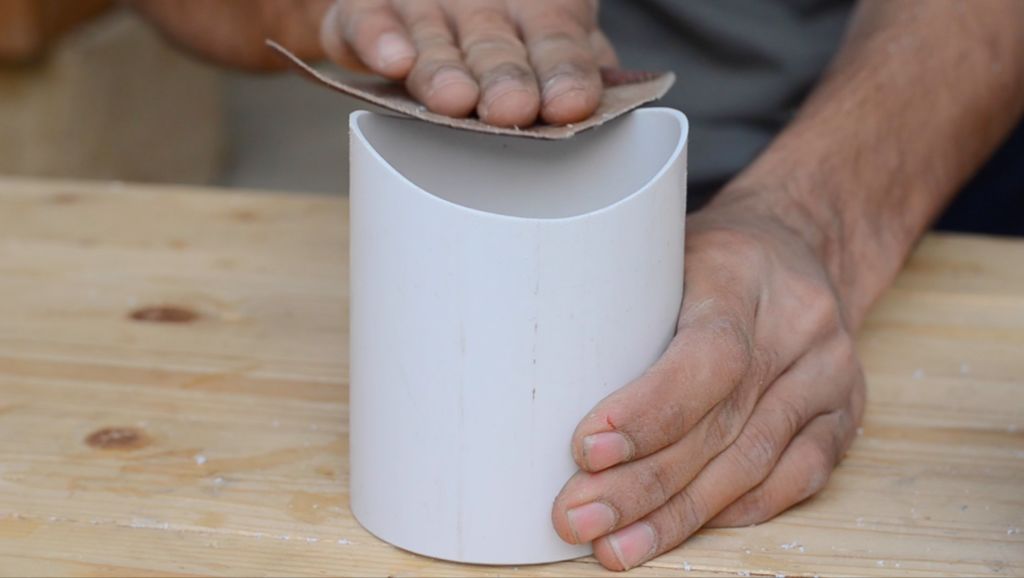
Внутренний воротник для воздуховода изготавливается из 125 мм ПВХ-трубки. Эта трубка формирует узкое отверстие примерно 13 мм шириной для равномерного распространения воздуха из полости/воздуховода. Три части, а именно внешняя 150мм дюймовая ПВХ-трубка, конический внутренний корпус из пластиковой чашки и внутренний воротник из 125мм дюймовой ПВХ-трубки, вместе формируют корпус для выхода воздуха.
Чтобы сформировать основание, я использовал 90 мм ПВХ-трубку, отрезанную в высоту на 100 мм. Чтобы основание идеально прилегало к корпусу воздуховода, я сделал один срез трубки изогнутой формы. Эту форму я получил при помощи изоленты, контуром служила 150мм ПВХ-трубка.
Шаг 5: Впускное отверстие для воздуха
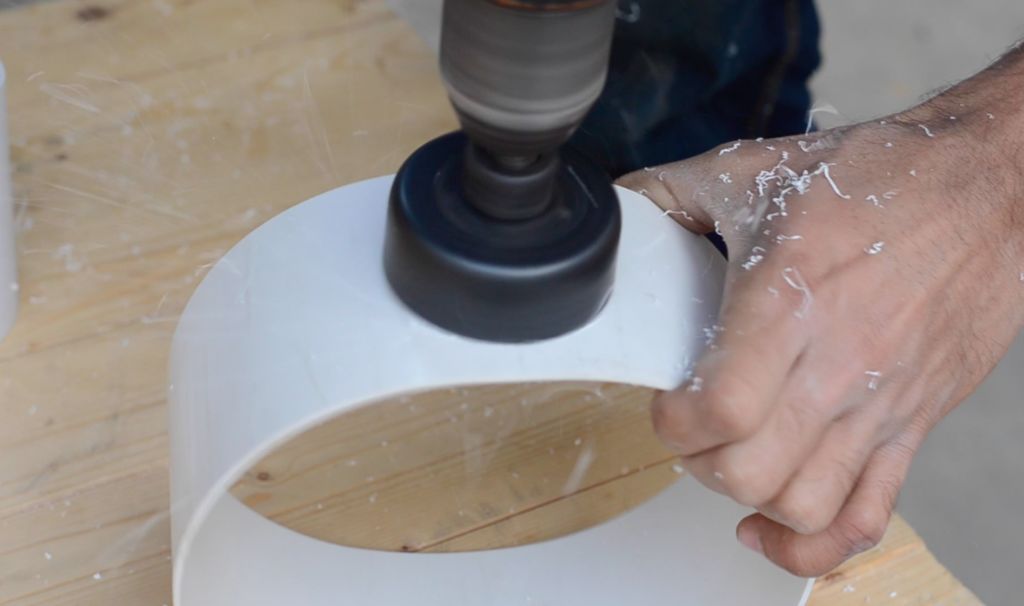
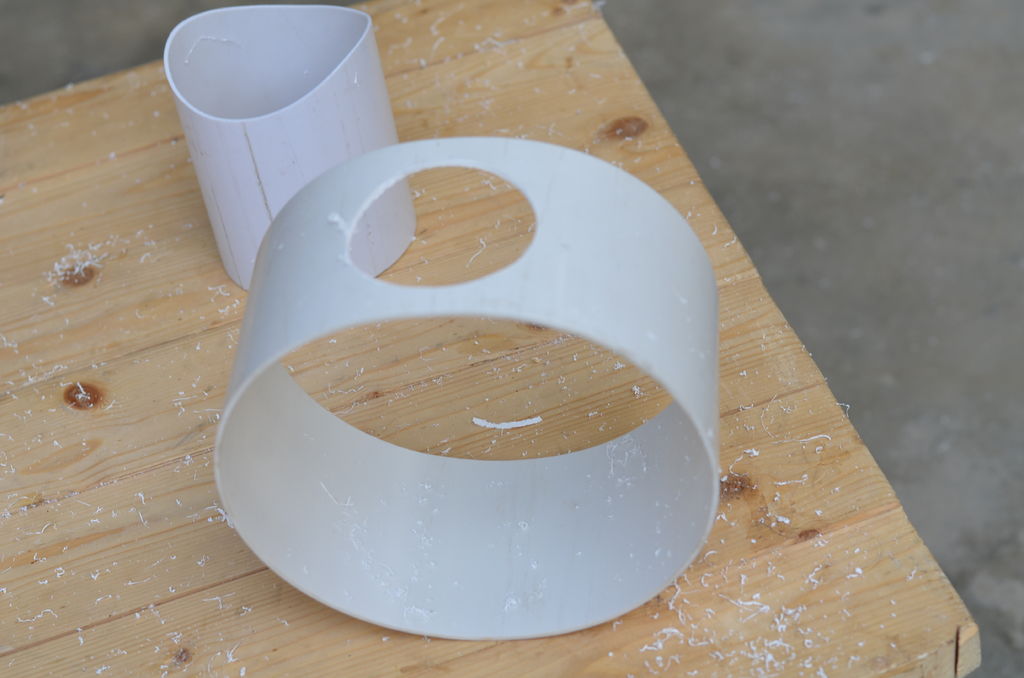
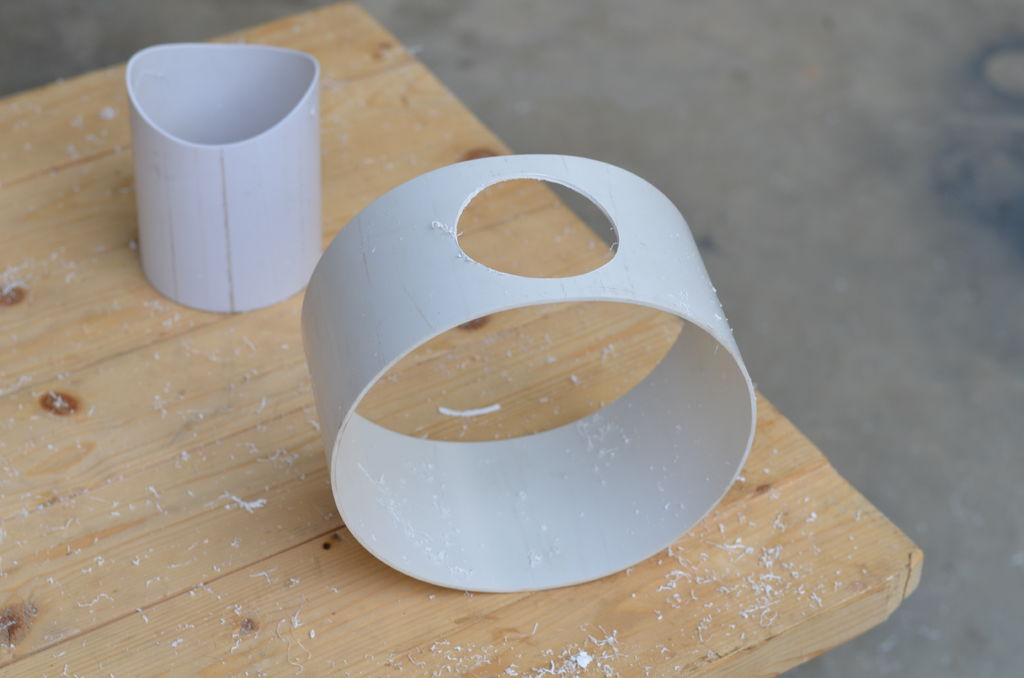
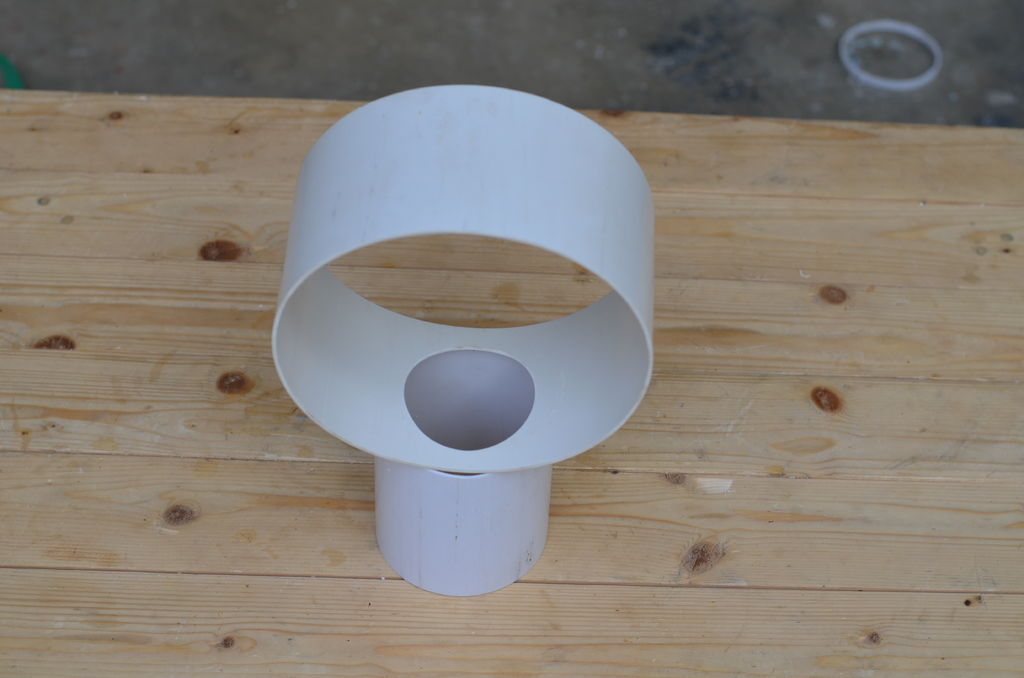
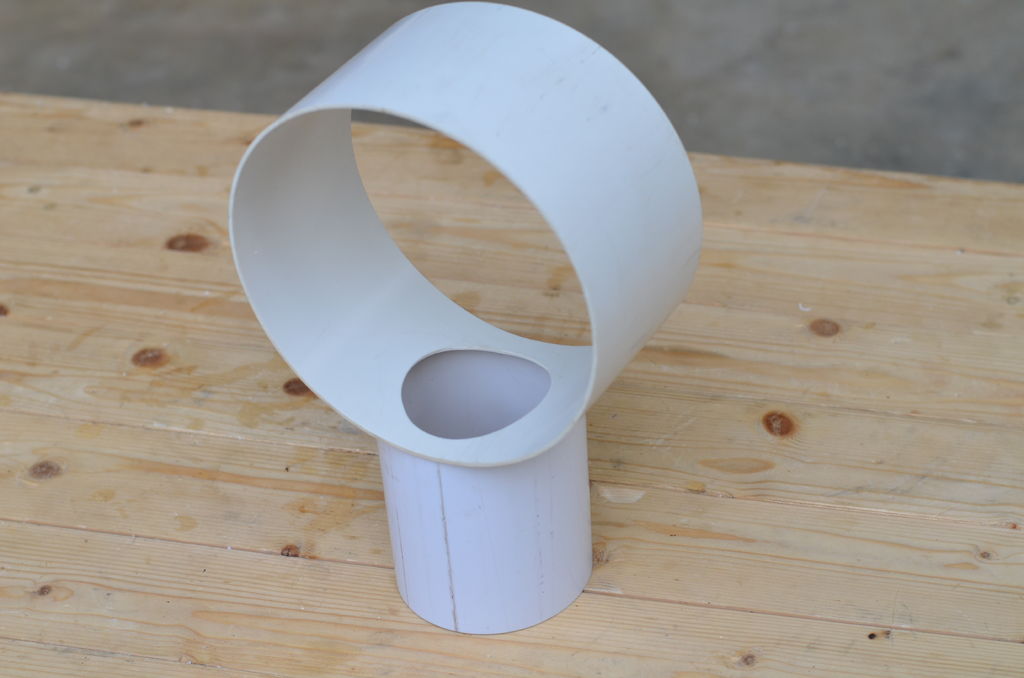
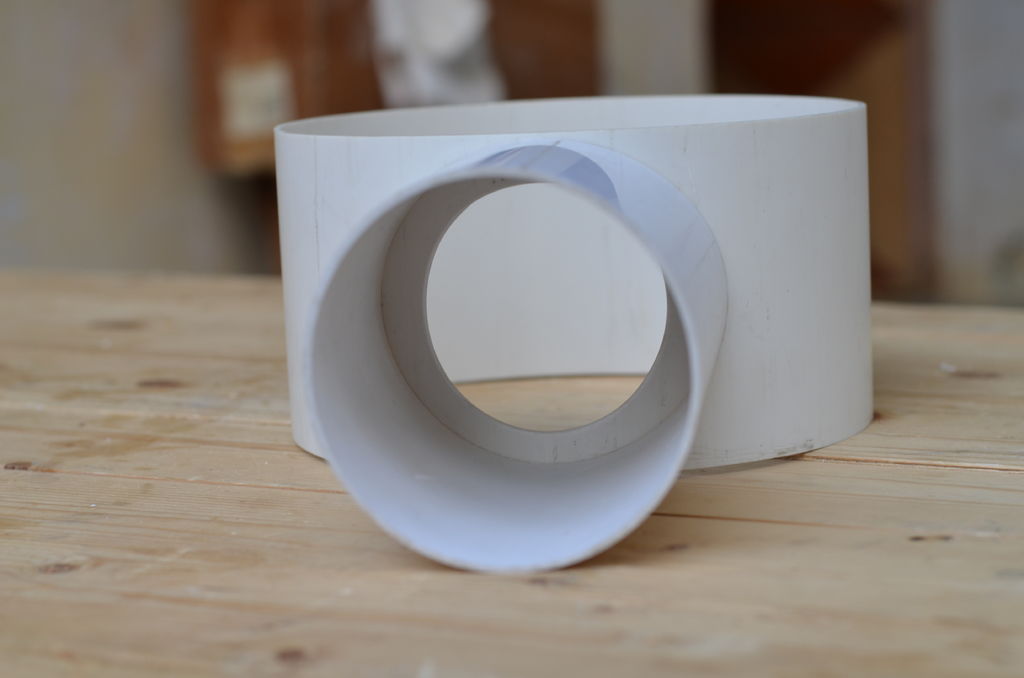
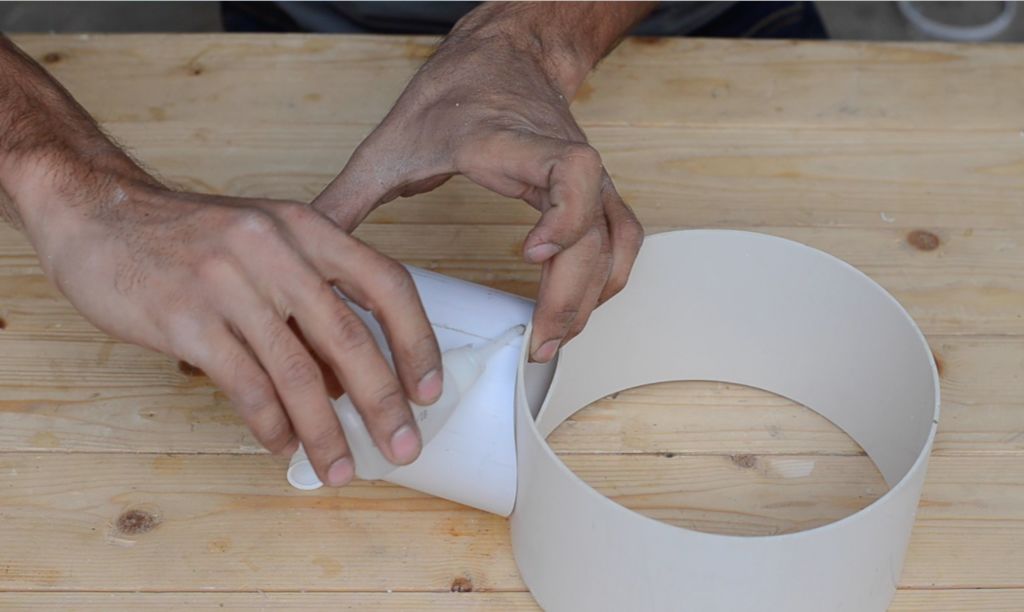
Перед тем, как приклеить основание к основному корпусу, я просверлил трёхдюймовое отверстие в шестидюймовой трубке, оно будет действовать как коридор для воздуха, проходящего в основной корпус и воздуховод. Дырка сверлится дрелью с насадкой для сверления дырок.
Затем основание приклеивается к внешней части воздуховода с помощью суперклея. Если вы идеально подогнали основание к 150 мм трубке, то суперклей создаст очень прочное соединение между ними.
Шаг 6: Кольцо воздуховода
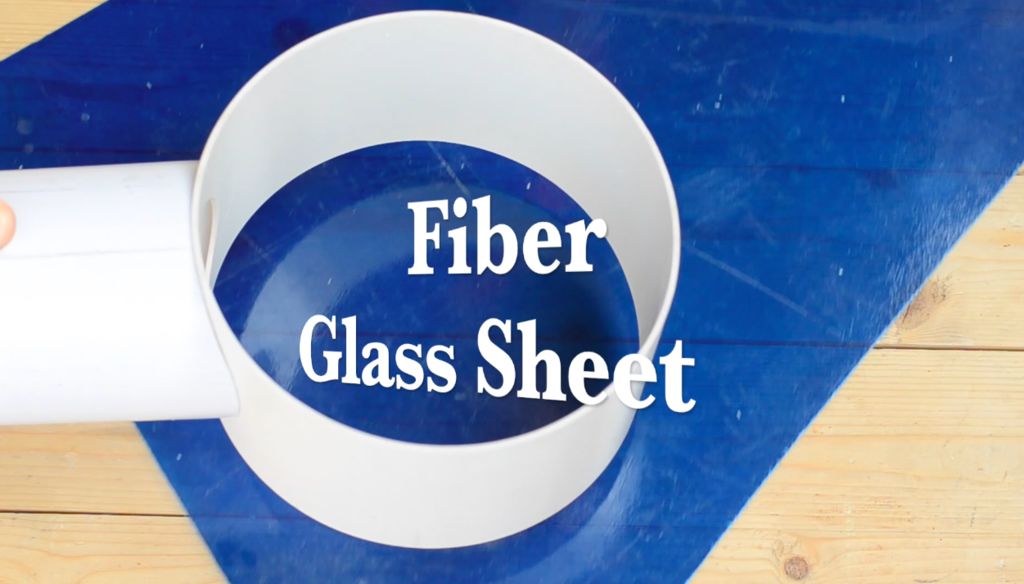
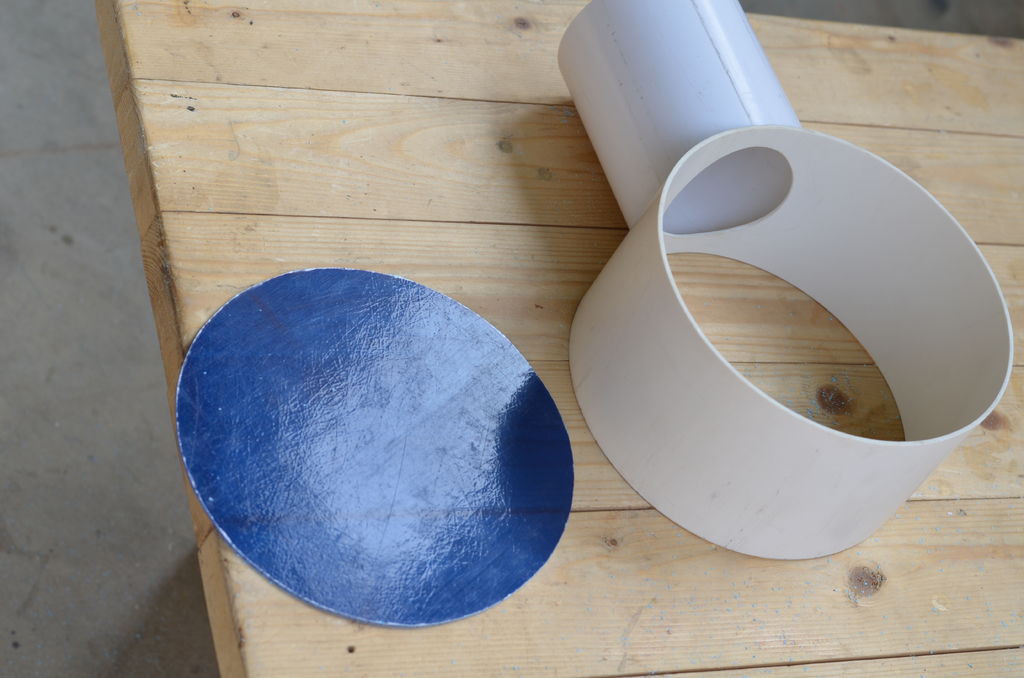
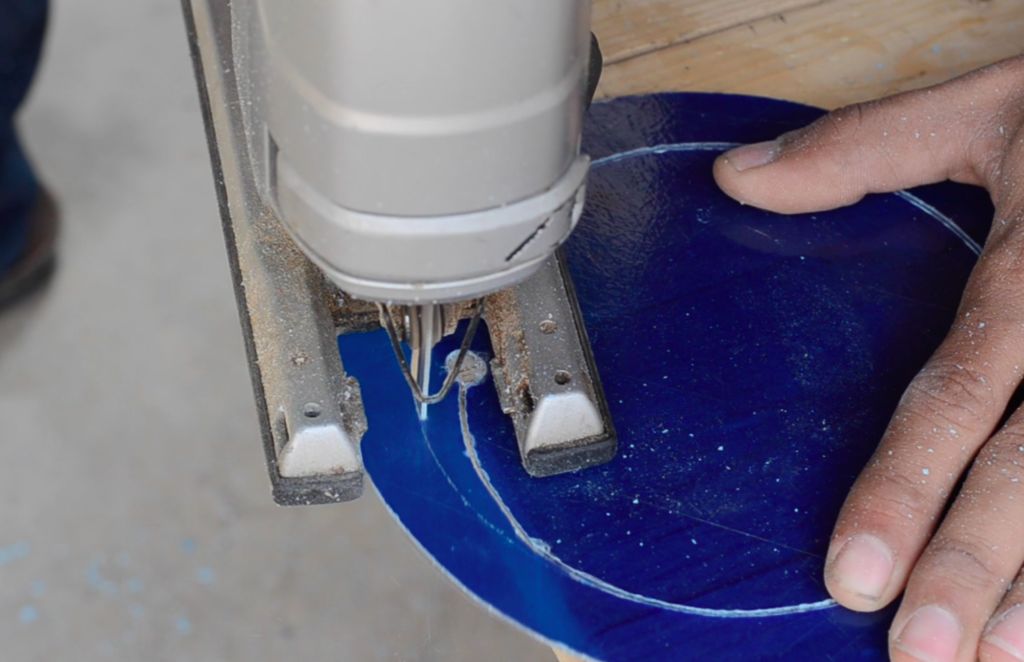
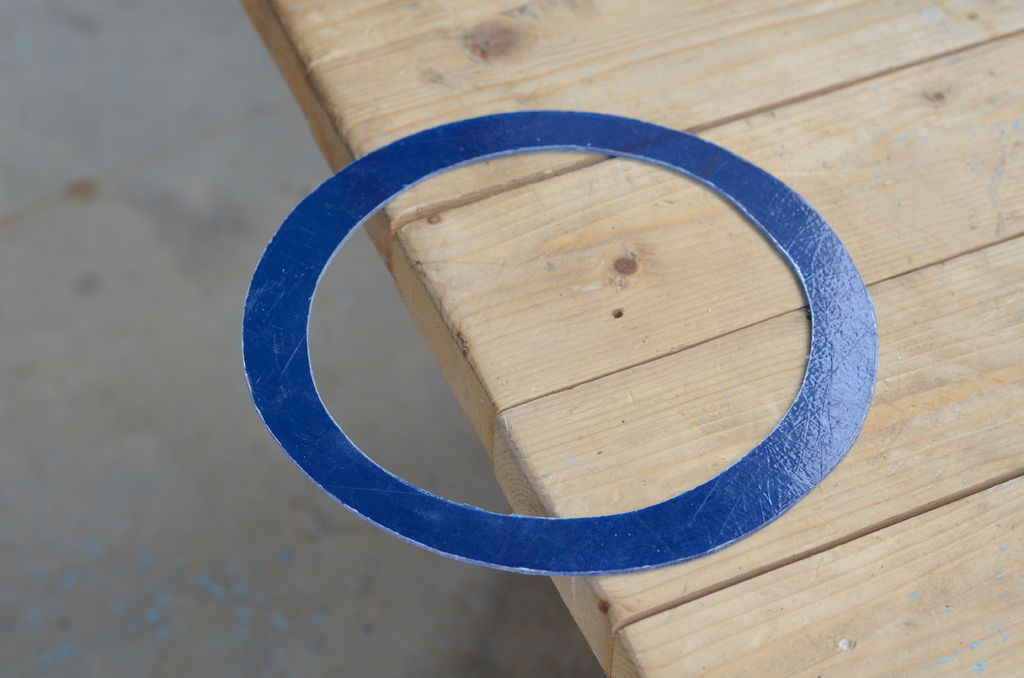
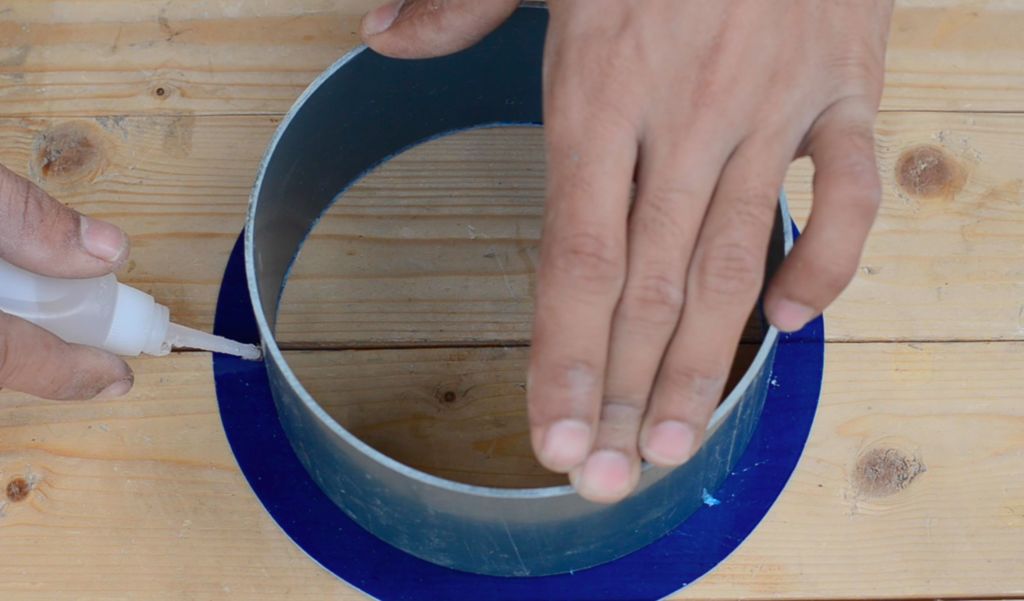
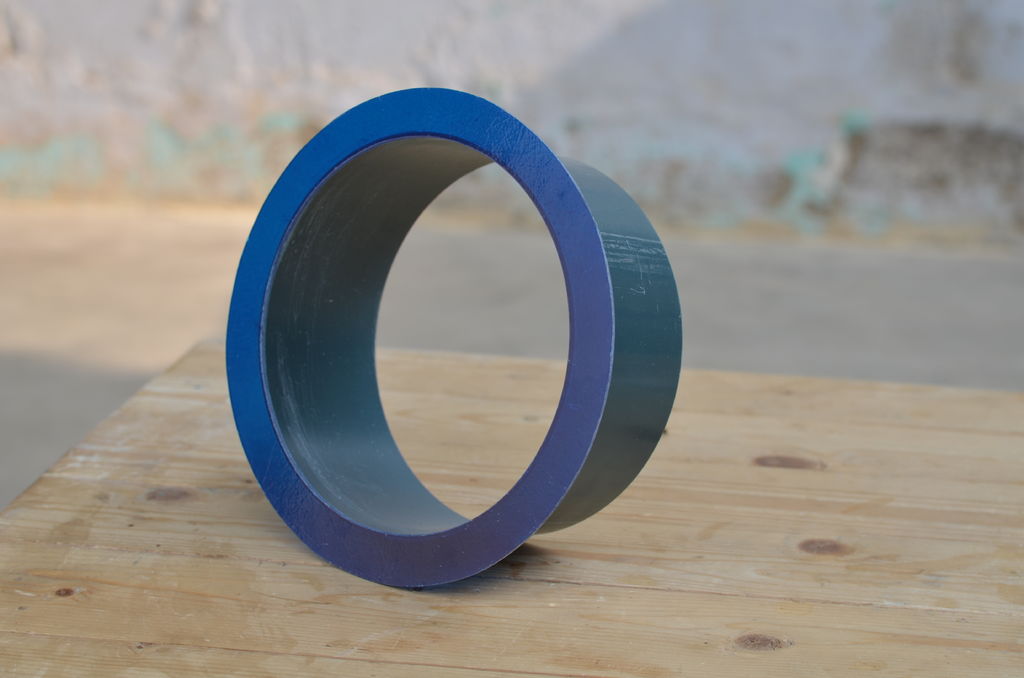
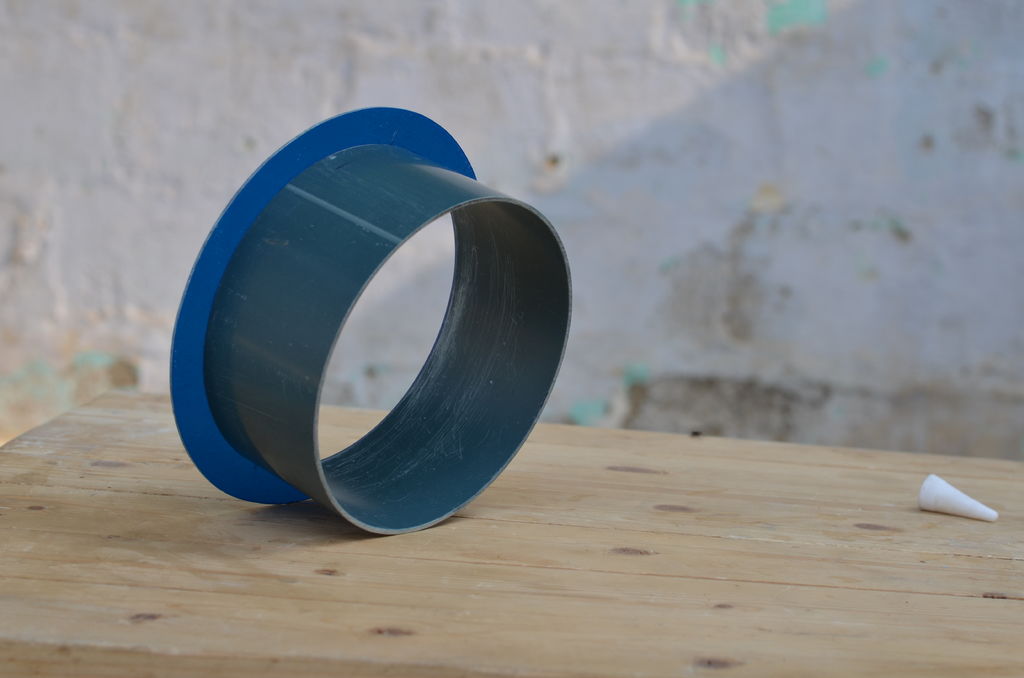
Кольцо для воздуховода делается из фибергласа толщиной 3мм, которое также служит соединением между внутренней половиной и внешней половиной основного воздуховода.
Шаг 7: Покраска
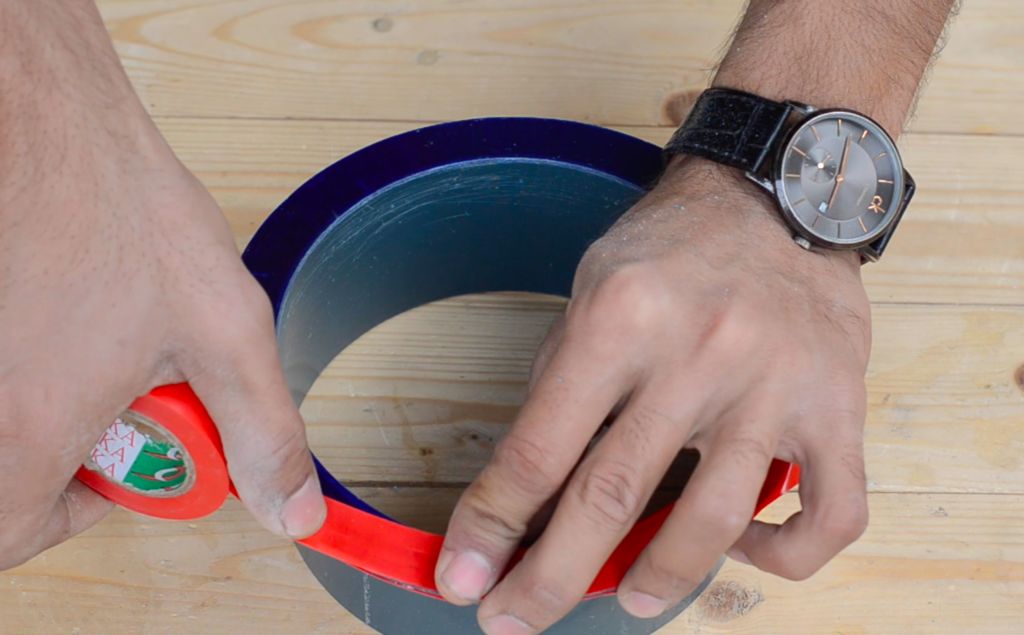
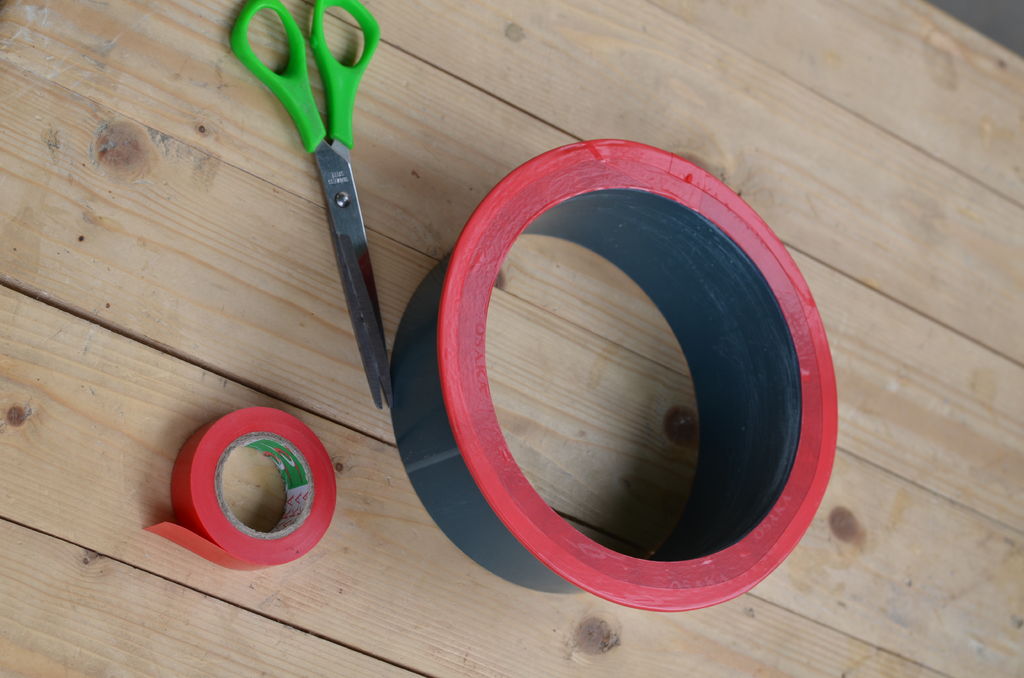
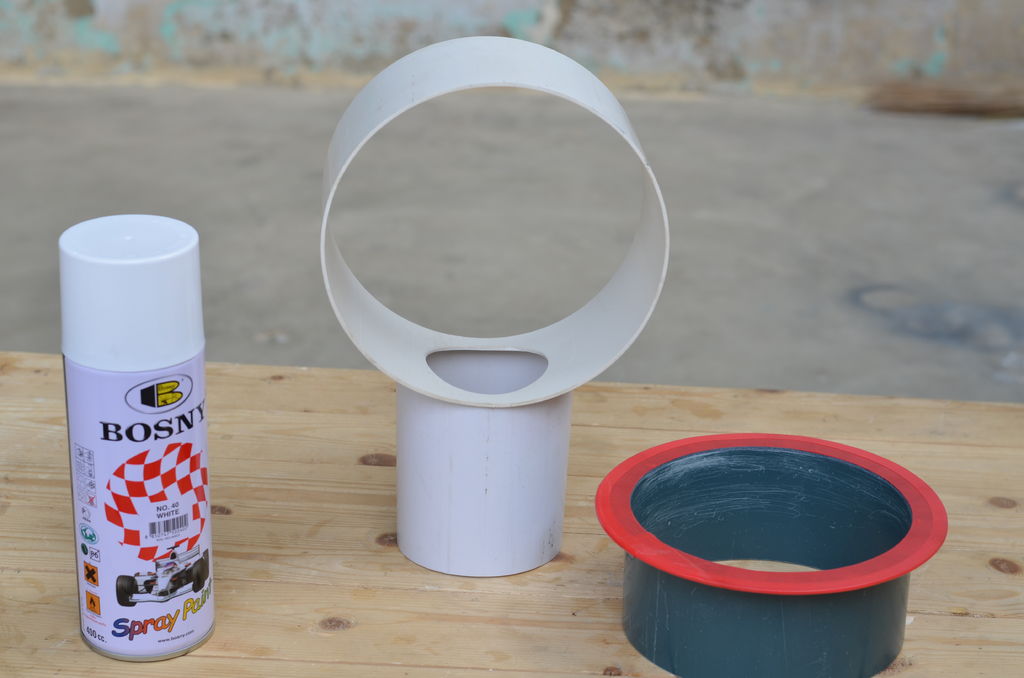
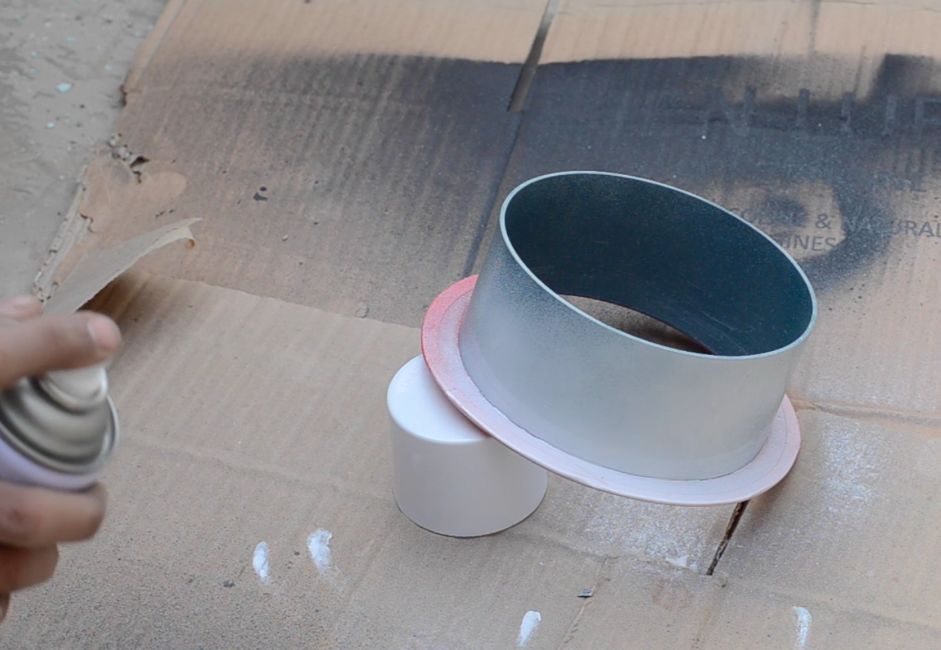
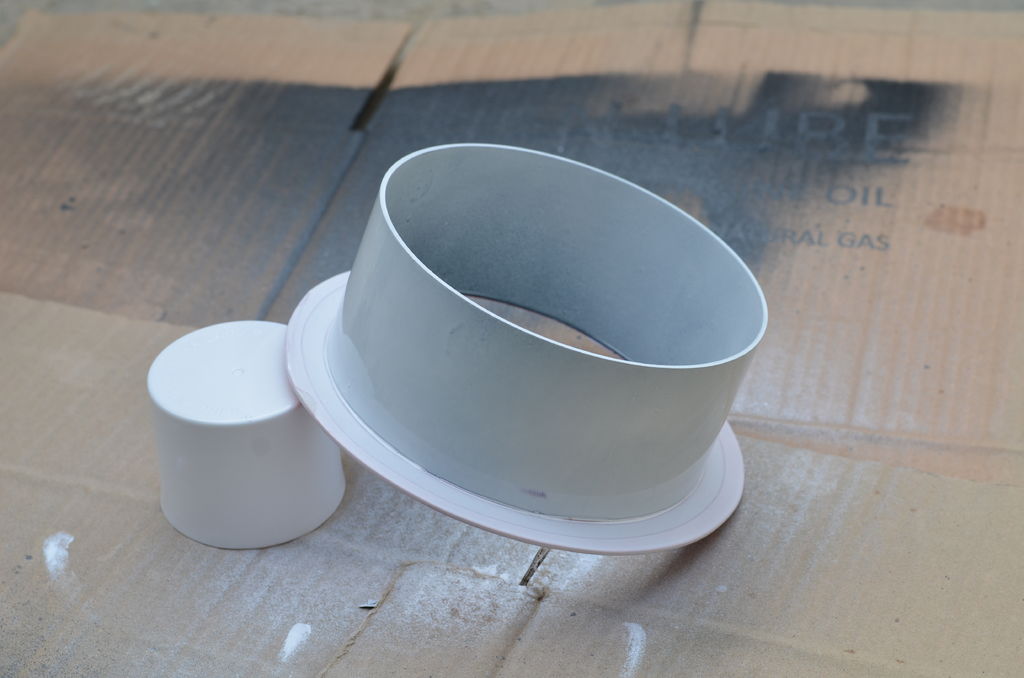
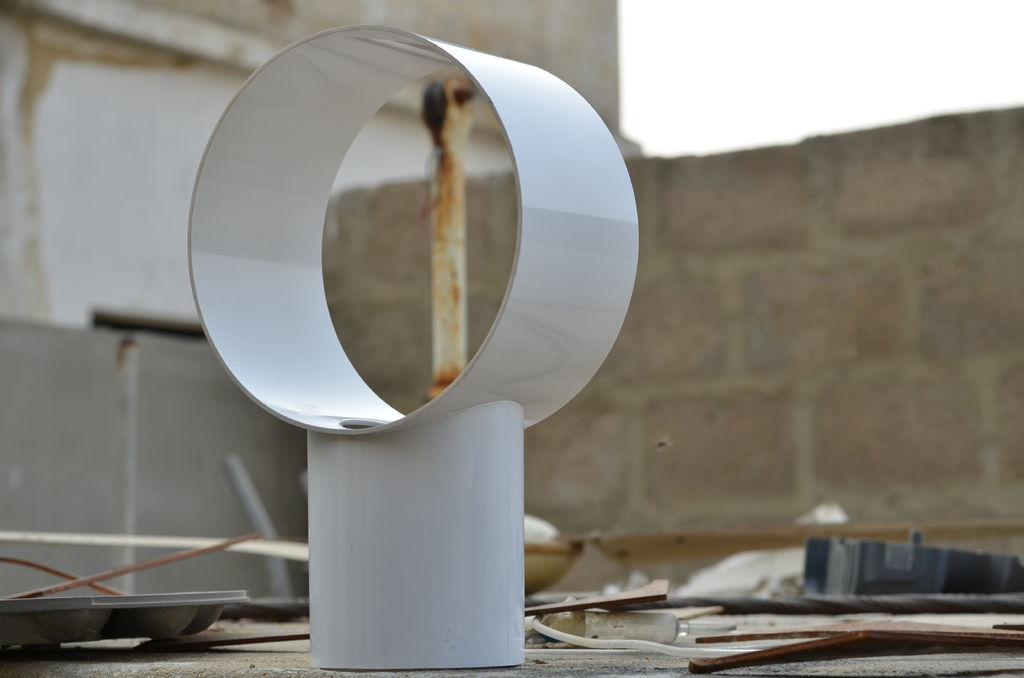
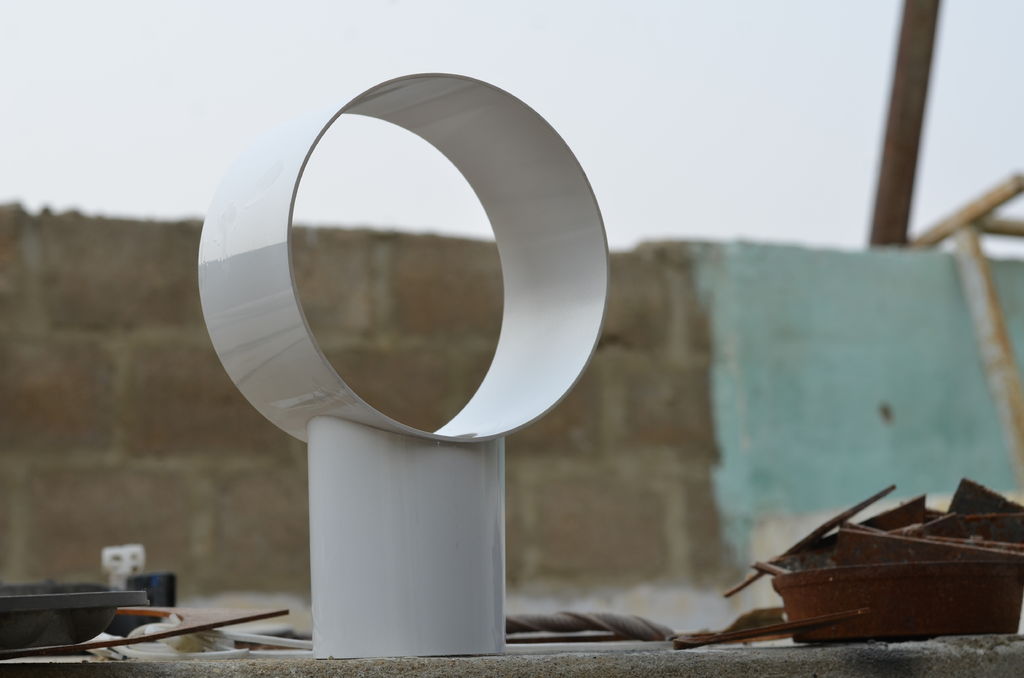
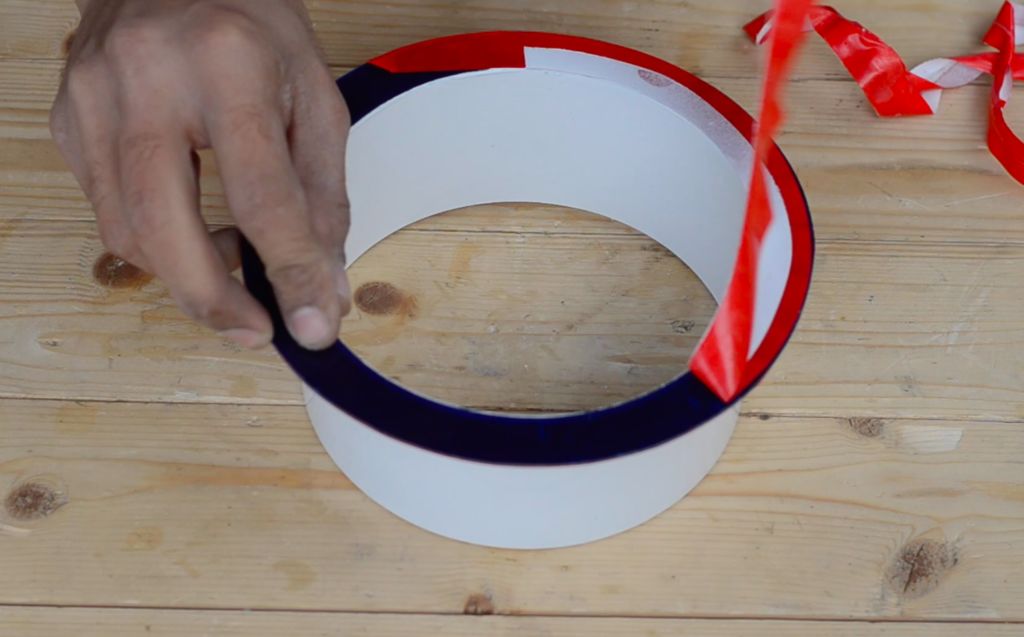
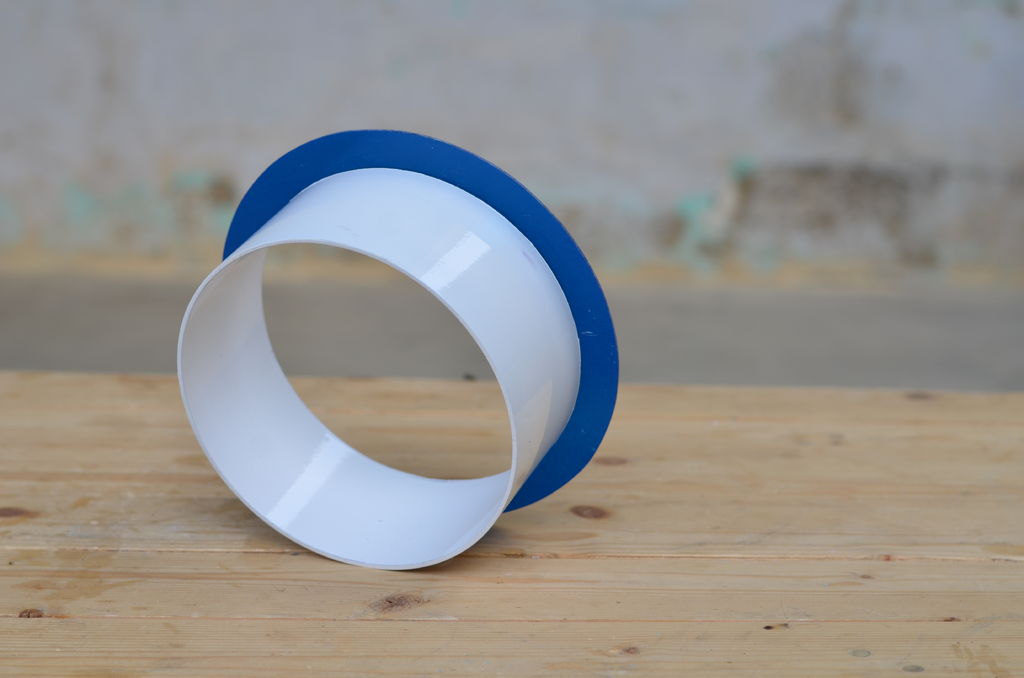
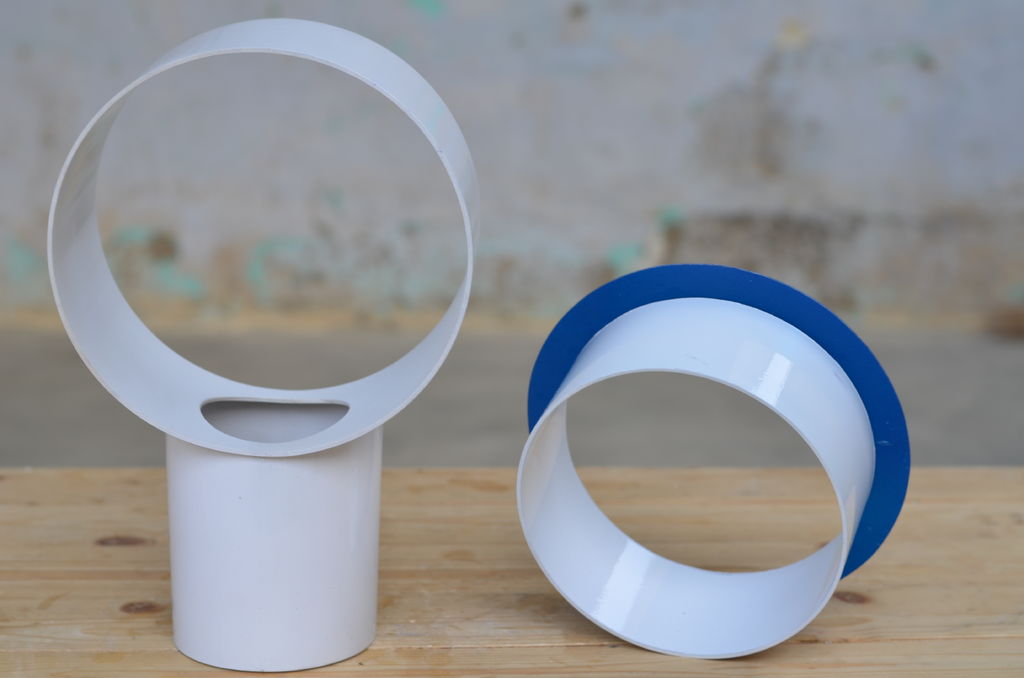
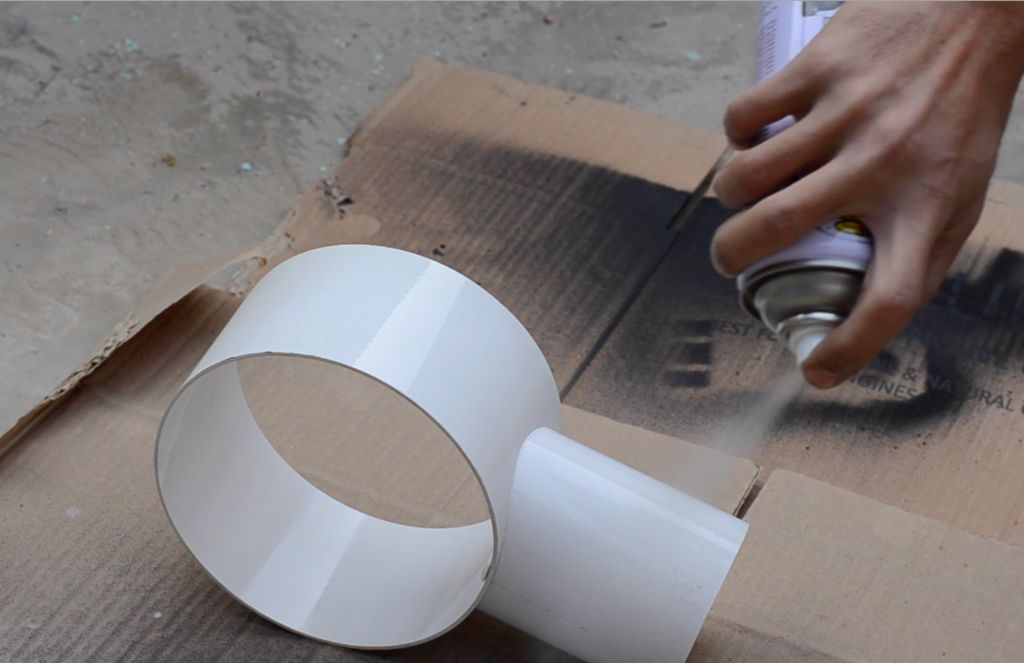
Так как основная часть корпуса готова, я решил покрасить её, чтобы придать ей приятный и опрятный вид. Я покрасил всё белым, используя аэрозольную краску, оставив неокрашенным только фиберглас, который был защищён от покраски изолентой.
Конечный результат оказался хорош, и синий лист фибергласа смотрелся фантастически на безупречно белой поверхности.
Шаг 8: Полоска светодиодов
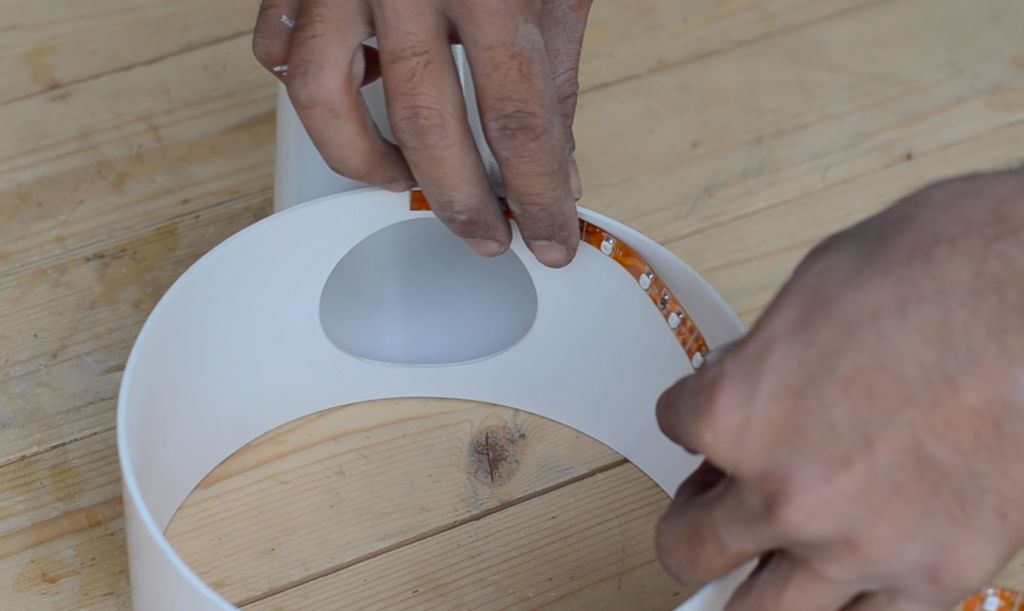
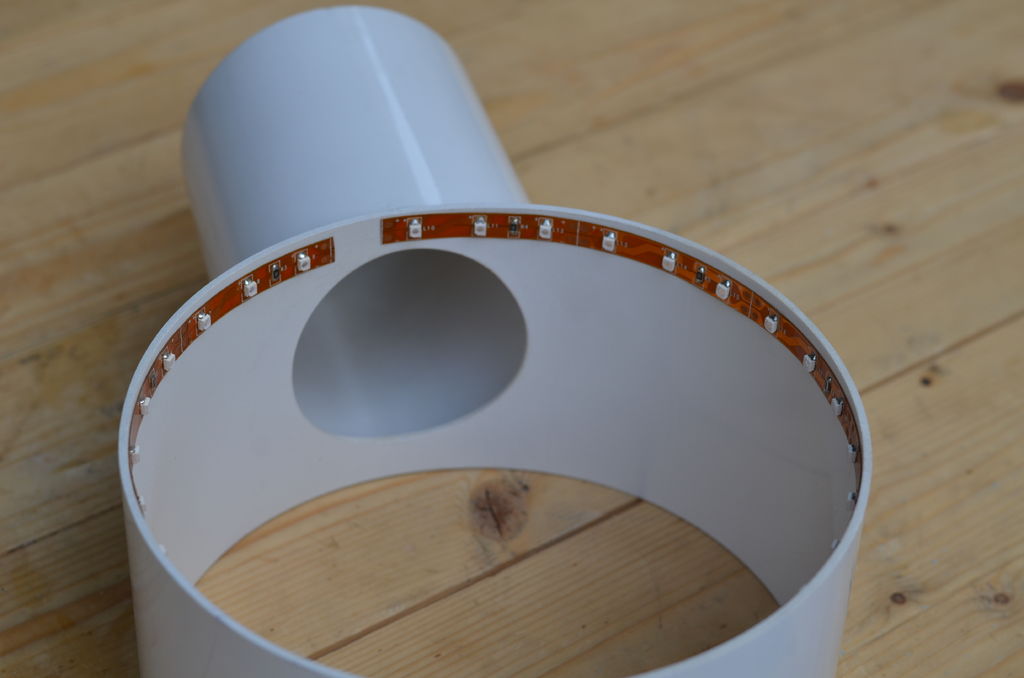
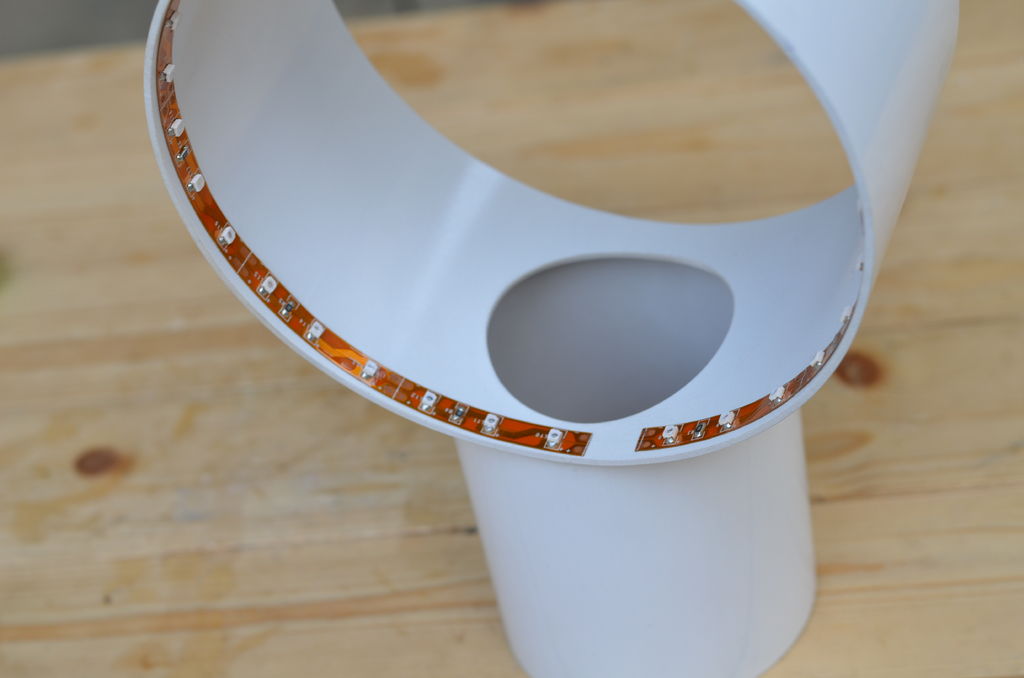
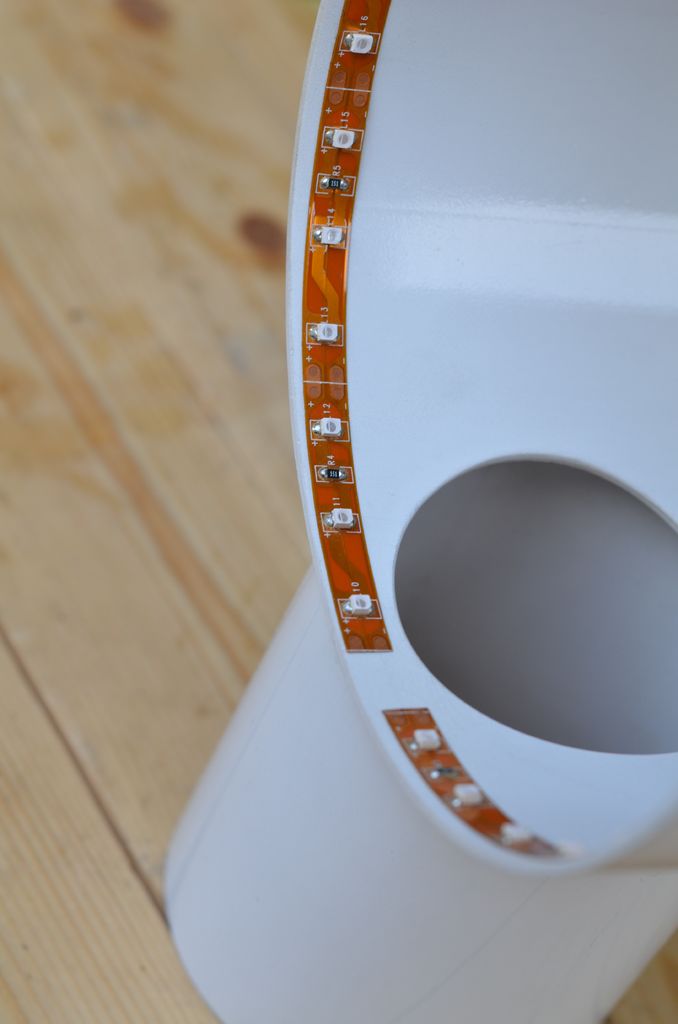
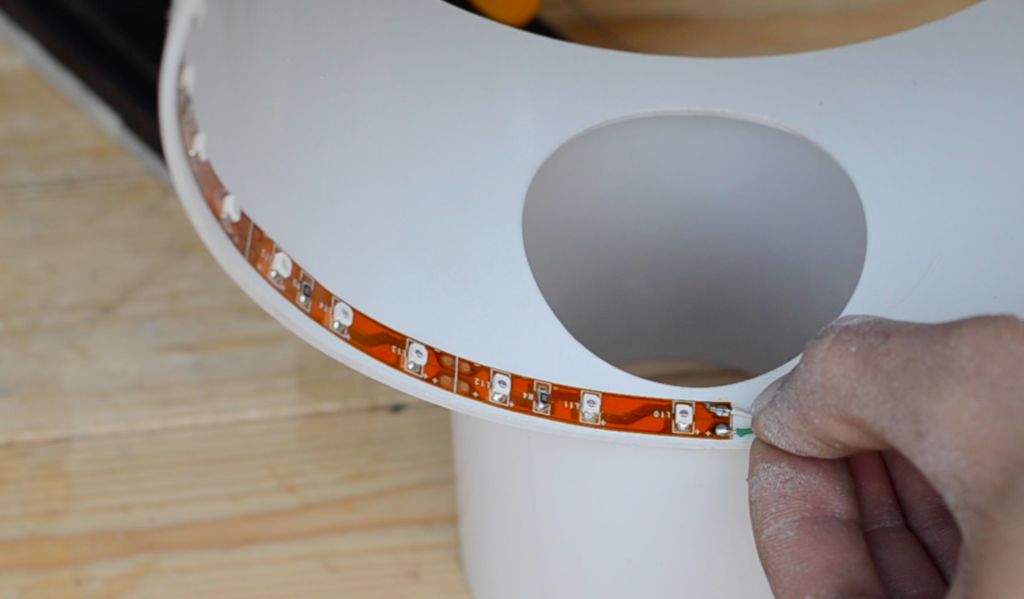
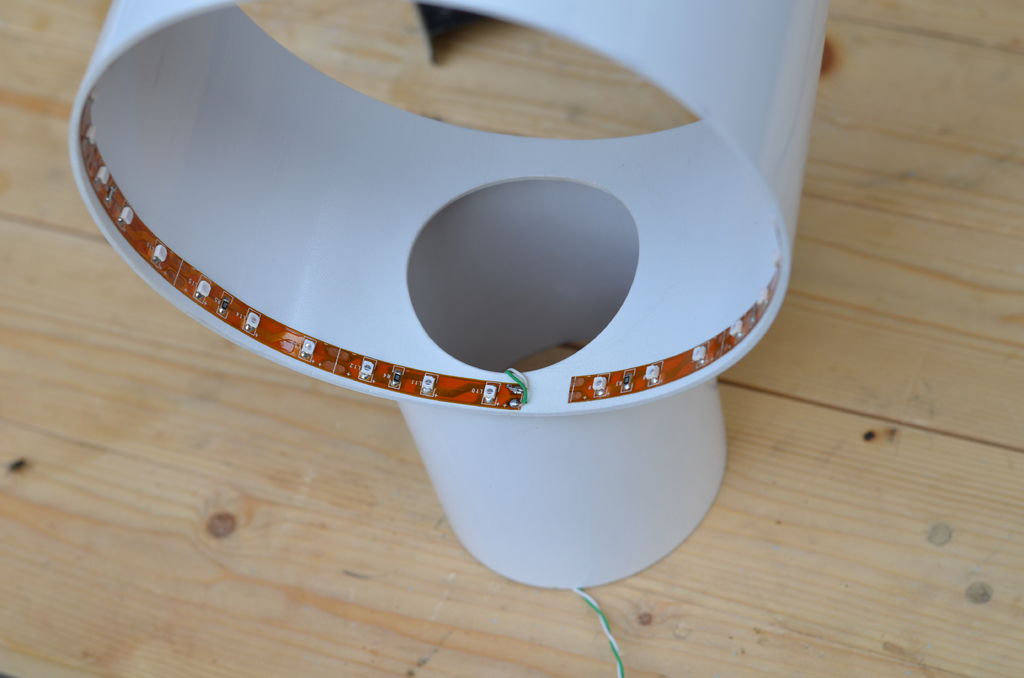
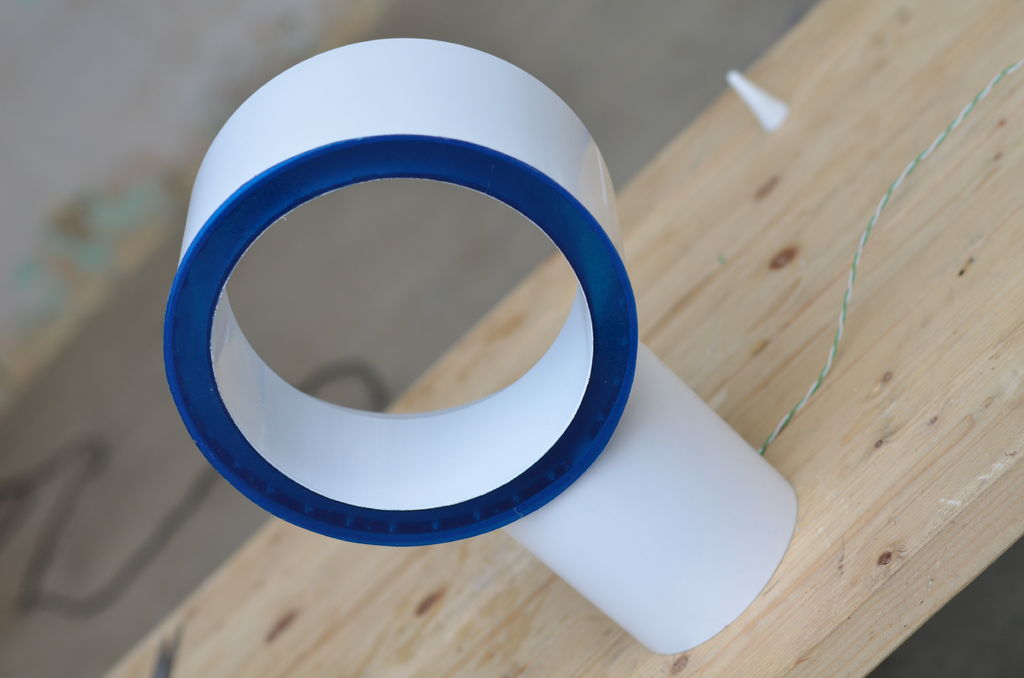
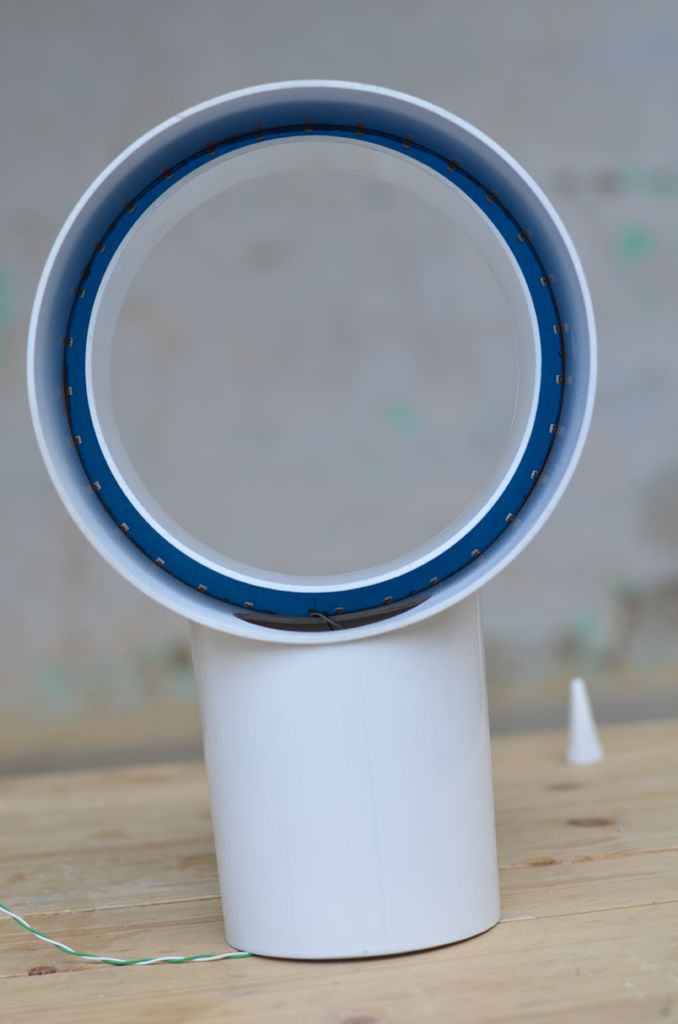
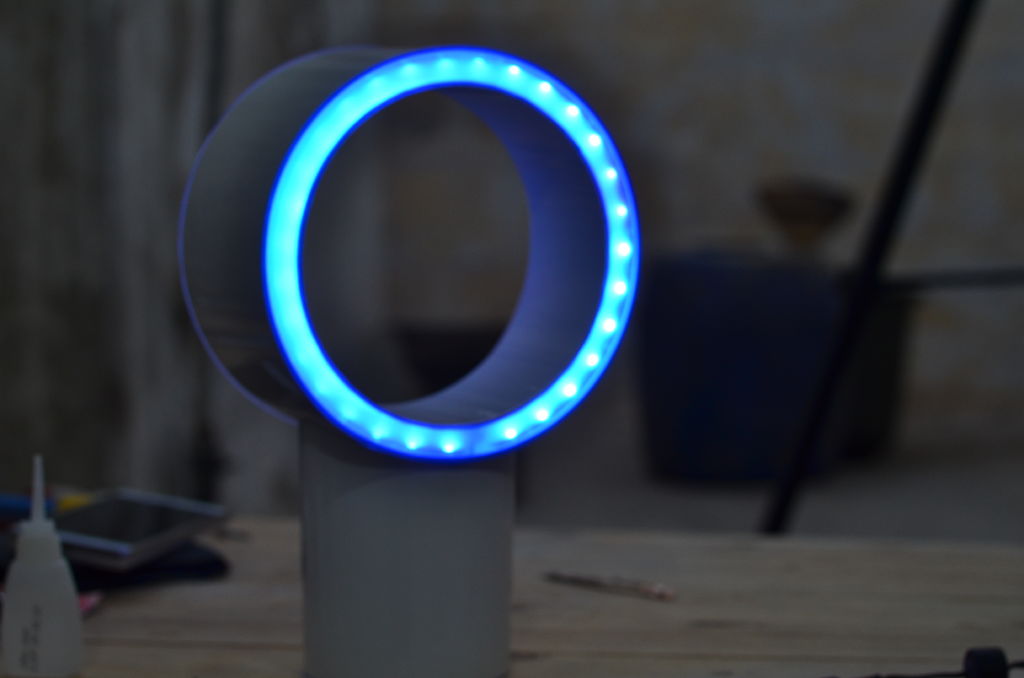
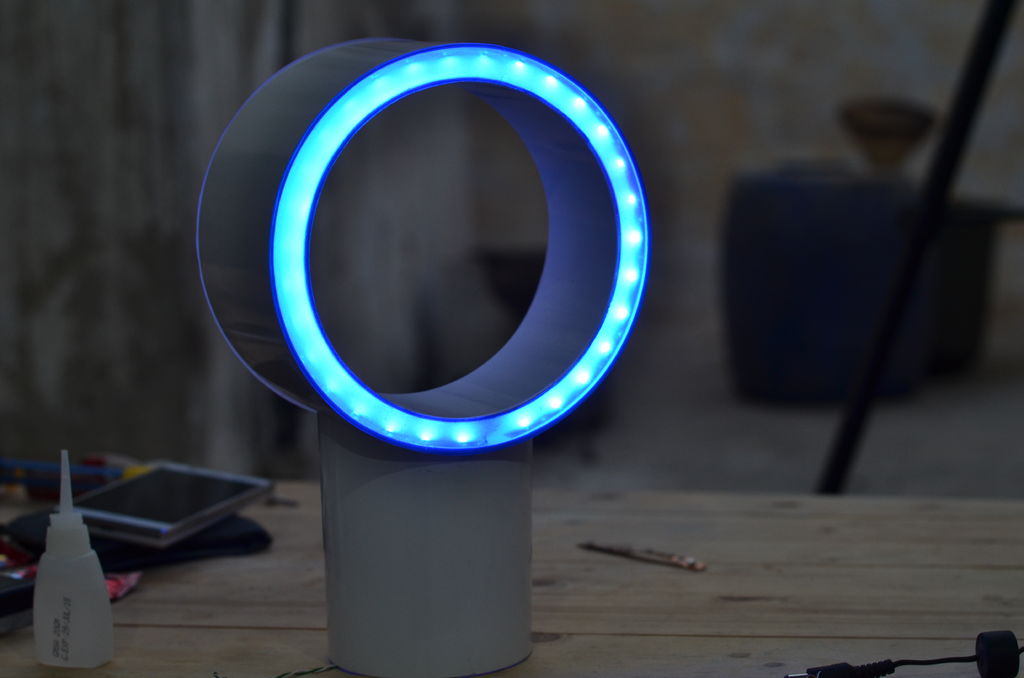
Чтобы дизайн был более привлекательным и элегантным, я добавил 12вольтную полоску светодиодов на внутреннюю часть воздуховода в той половине, где фиберглас будет склеен с внутренним воротником воздуховода. Светодиодная полоска отрезается нужной длины. На задней её части есть липкая полоса, оторвав защитную плёнку, приклеиваем светодиодную полосу к поверхности ПВХ.
Таким образом, когда я включаю вентилятор, светодиодная полоса начинает освещать заднюю часть воздуховода и это создает очень крутой эффект распространения синего свечения, если смотреть спереди.
Шаг 9: Склеивание всех частей

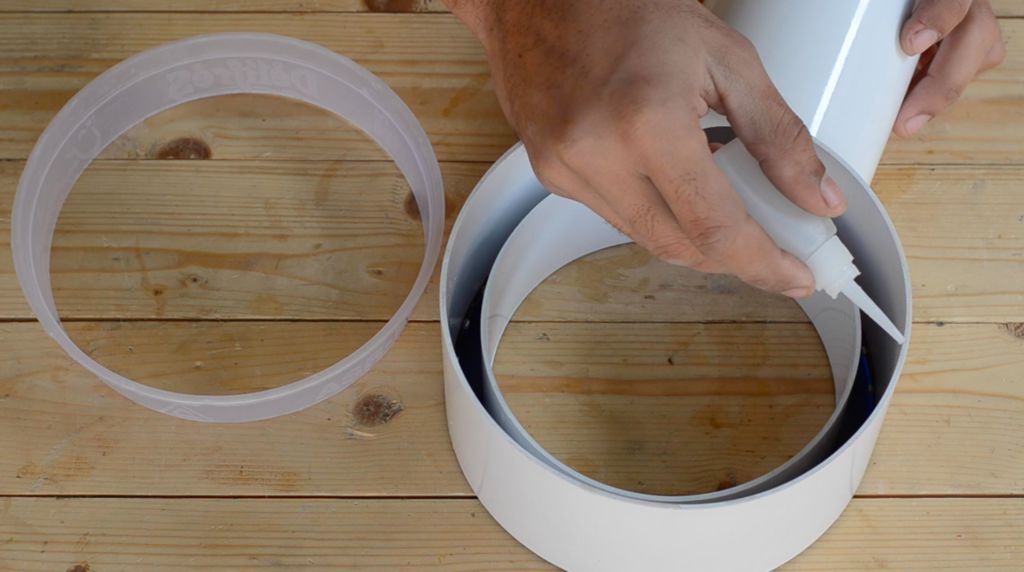
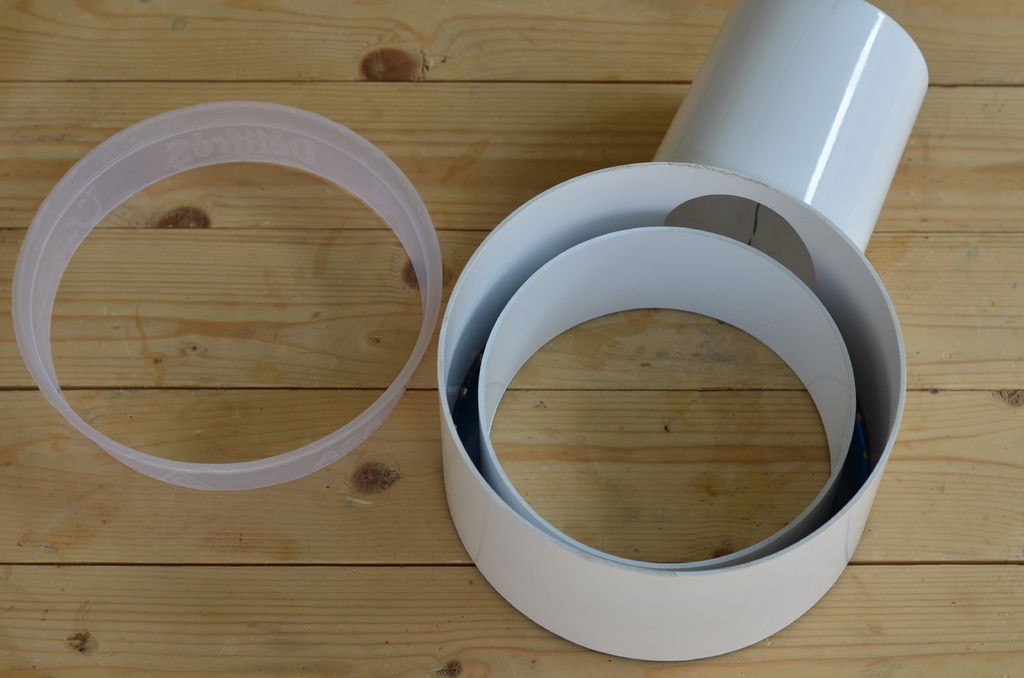
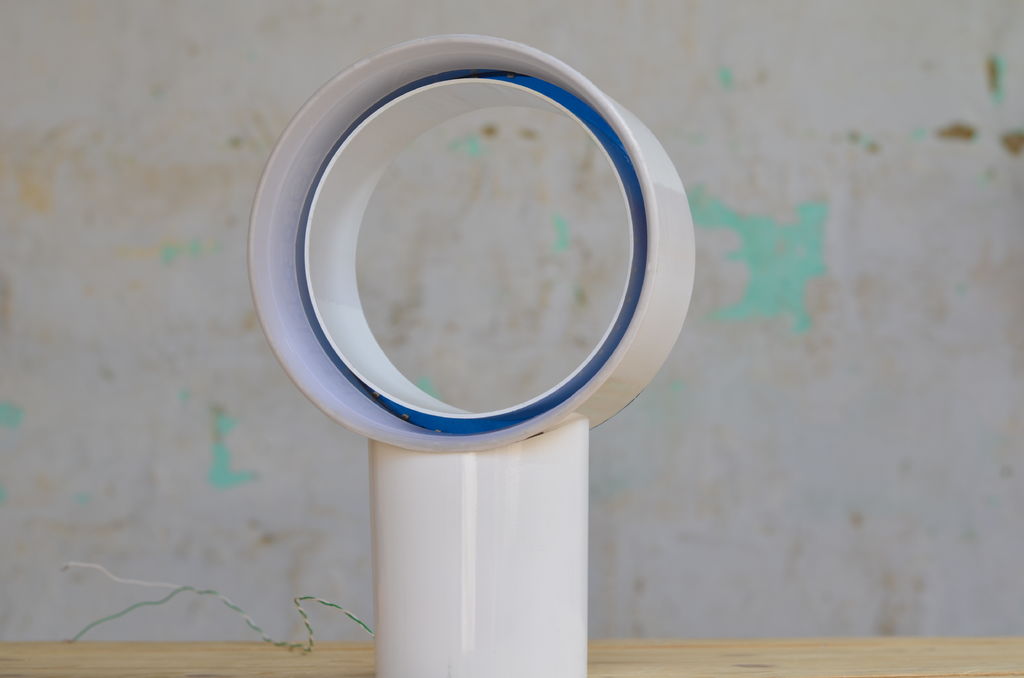
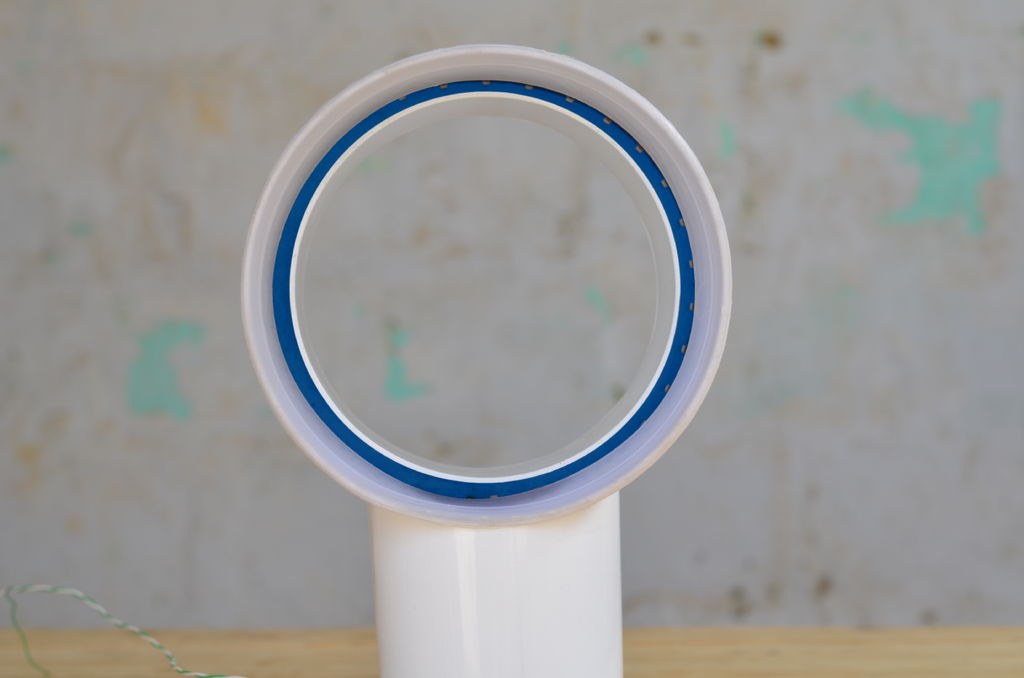
Когда краска высохла, я приступил к склейке всех частей вместе, чтобы сформировать основное тело нашего безлопастного вентилятора, используя суперклей, который, как мне кажется, скреплял все накрепко.
Шаг 10: Установка вентилятора
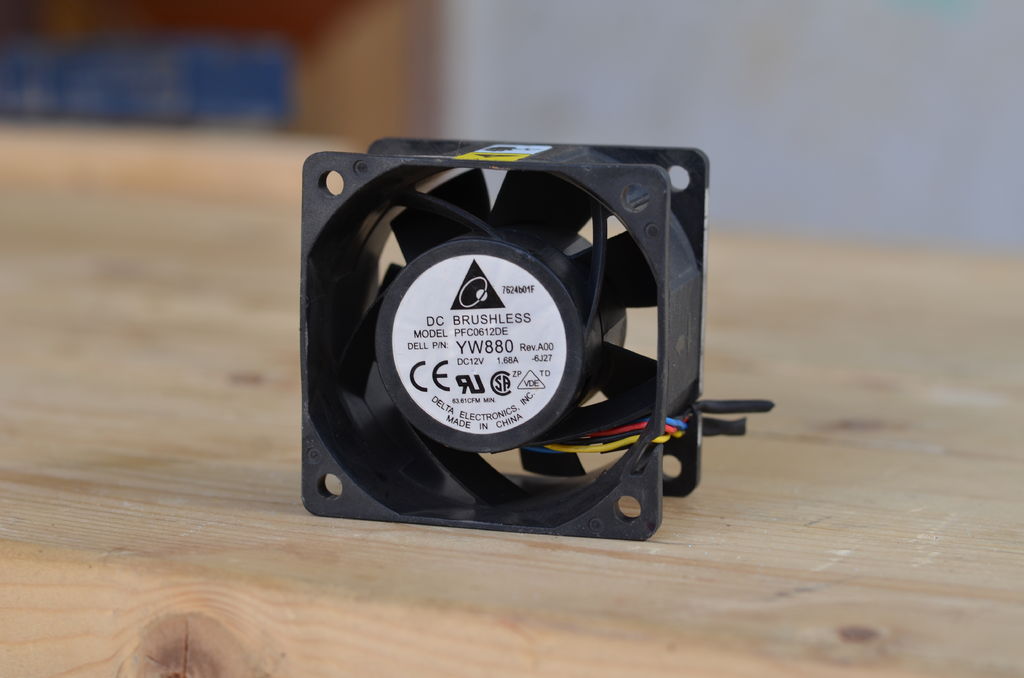
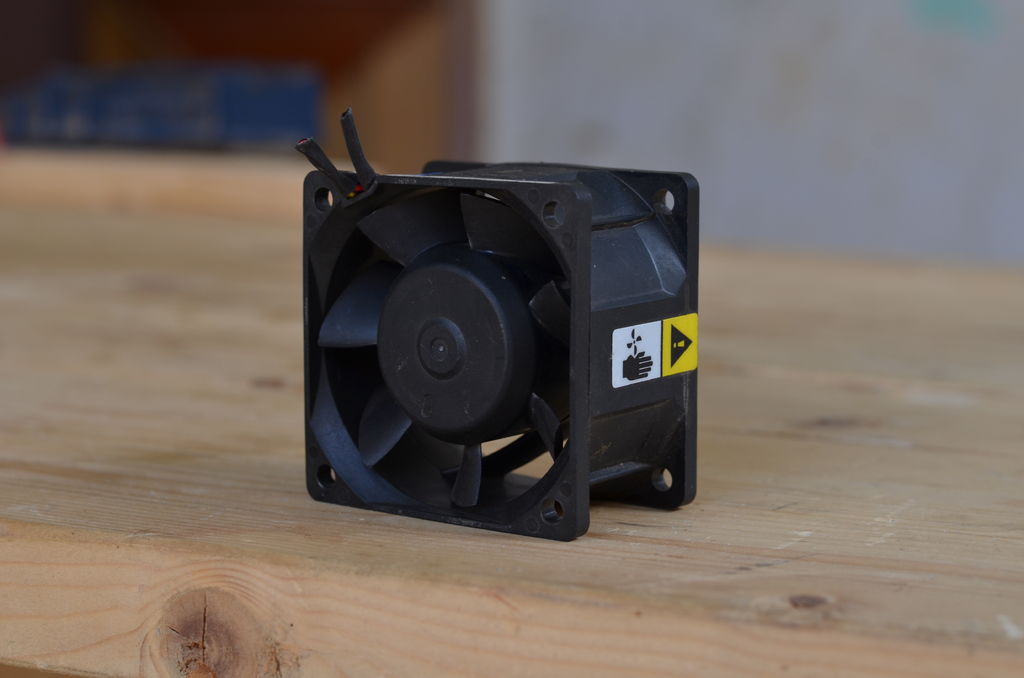
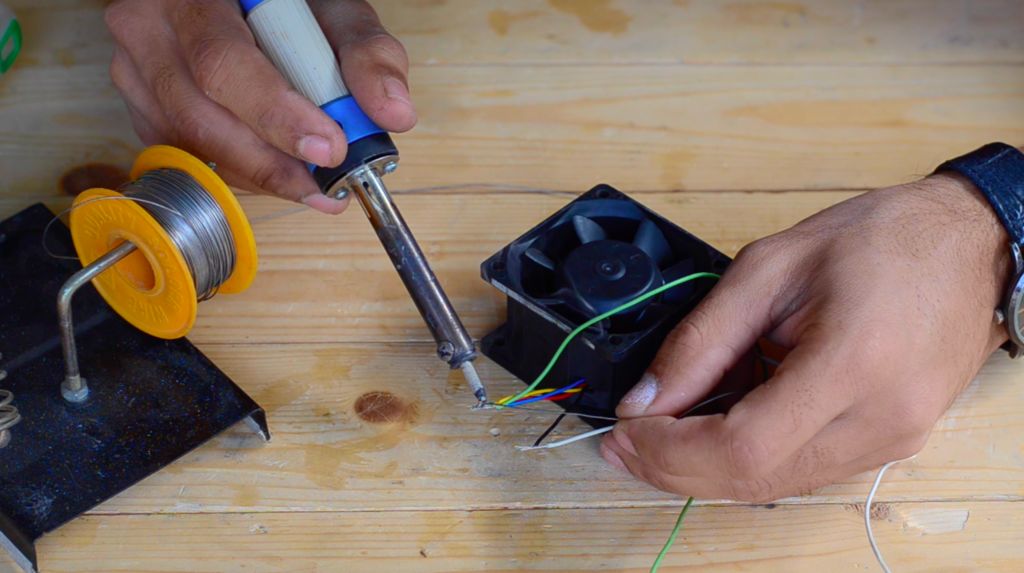
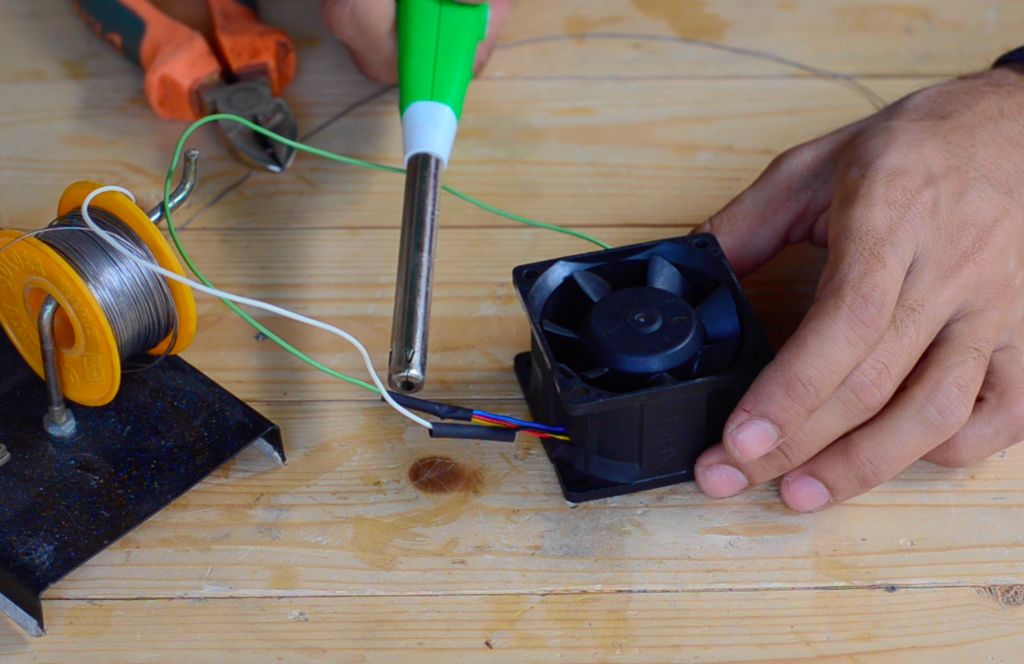
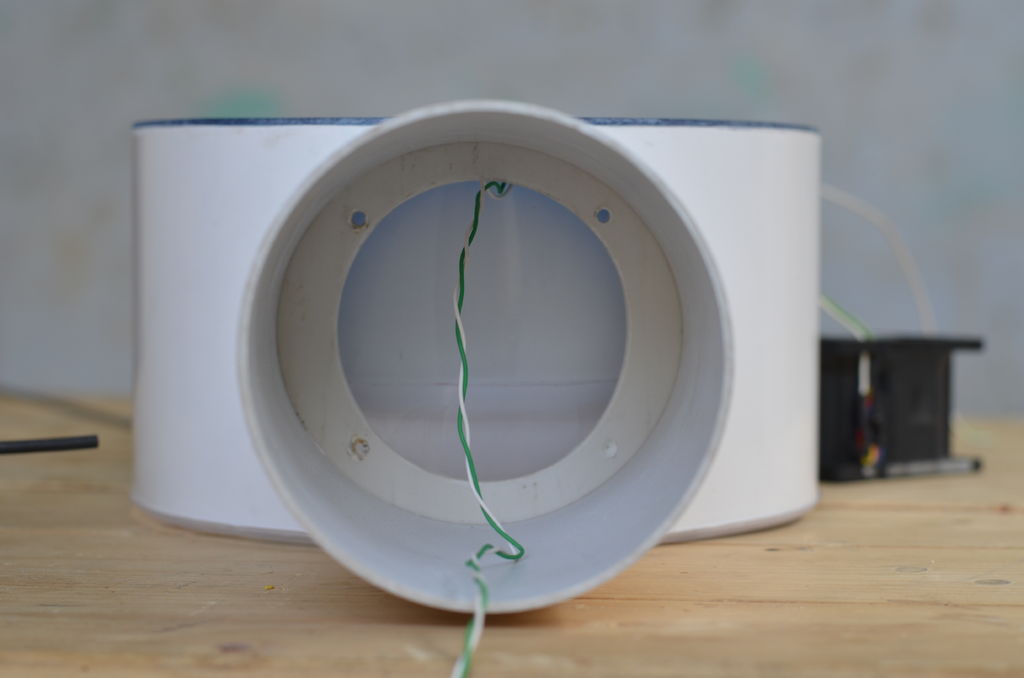
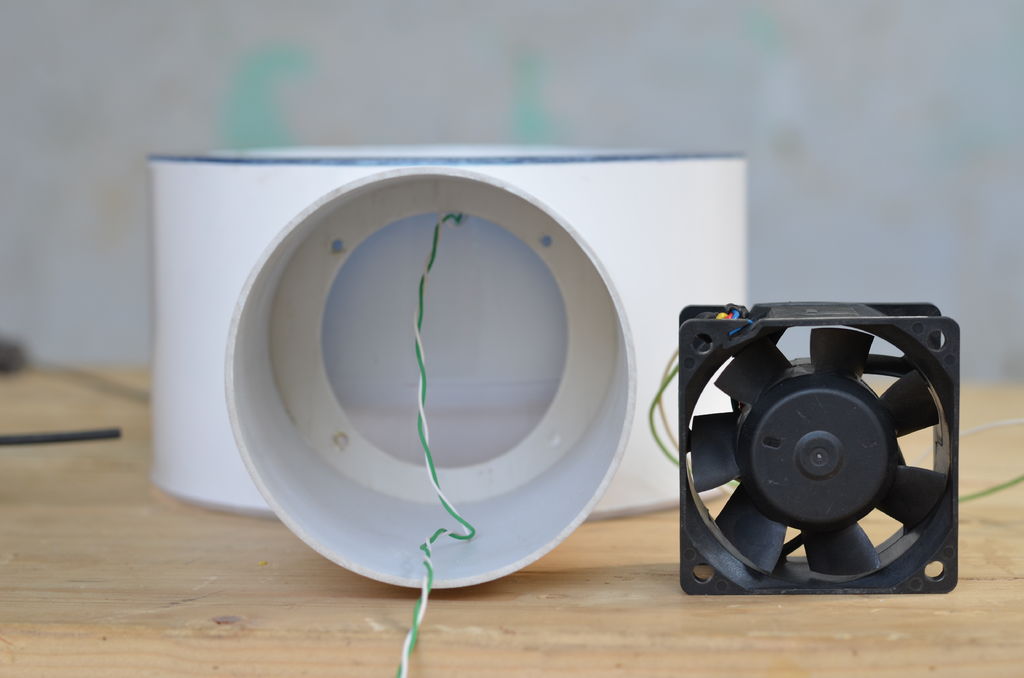
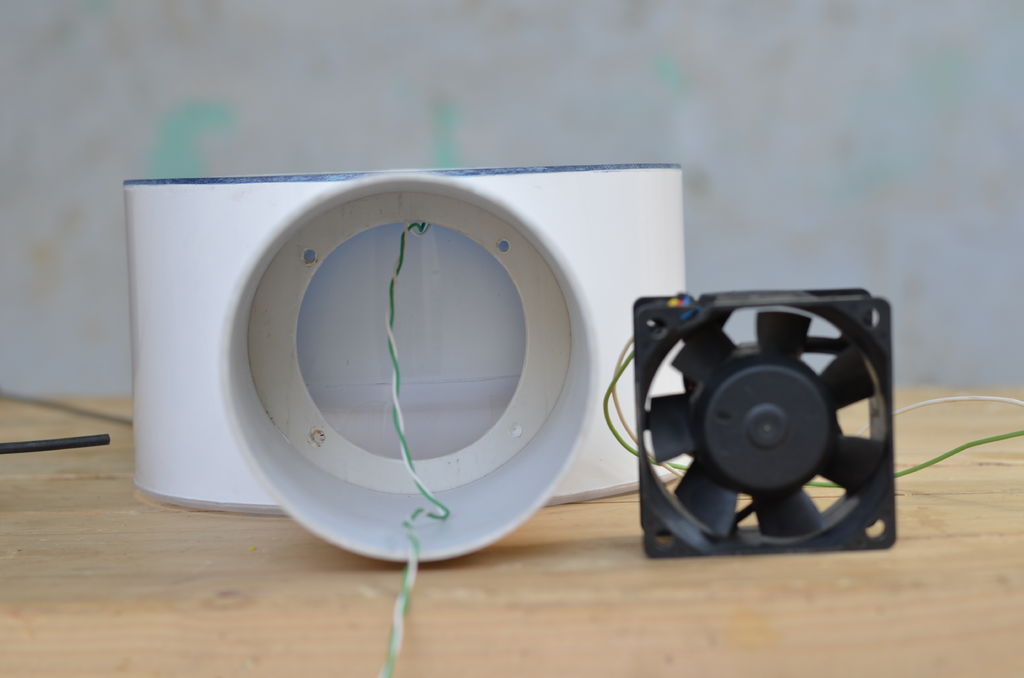
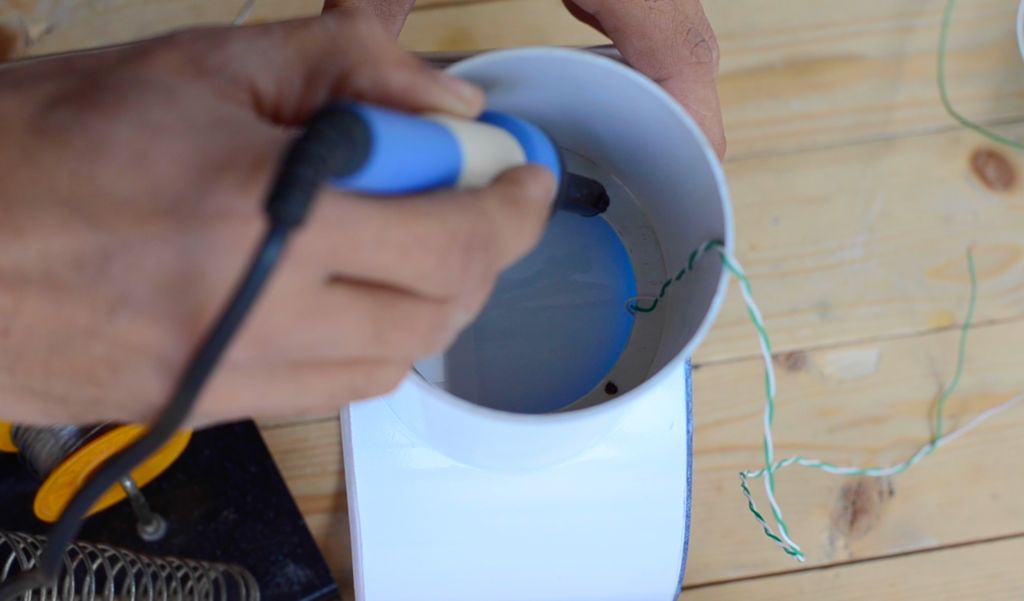
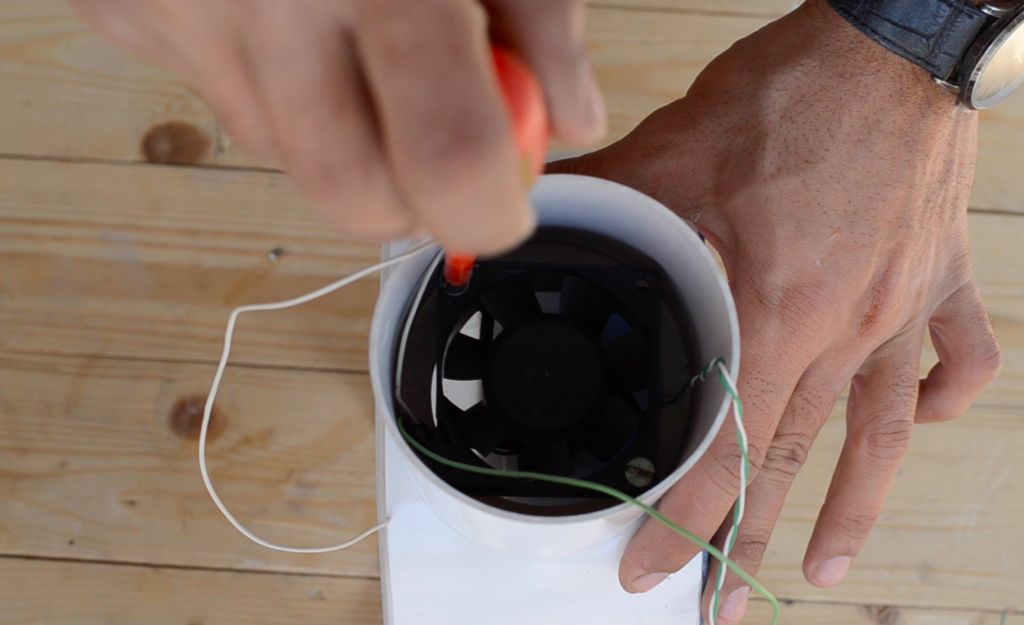
Итак, в каждом безлопастном вентиляторе есть вентилятор с лопастями 🙂
Чтобы наш безлопастной вентилятор заработал, я использовал высокоскоростной вентилятор 12V DC, который я обнаружил в своих старых компьютерных завалах. Более того, это был серверный вентилятор, что означает, что он более мощный, чем обычный компьютерный вентилятор. Так что я очень советую вам использовать вентиляторы такого типа.
Вентилятор устанавливается внутрь основания, прямо снизу от воздуховодного корпуса при помощи четырех винтов для дерева, что позволяет крепко закрепить его на месте. Он устанавливается таким образом, чтобы тянуть воздух вверх и, поэтому нам нужен вентилятор, у которого будет достаточно силы.
Шаг 11: Входные отверстия для воздуха
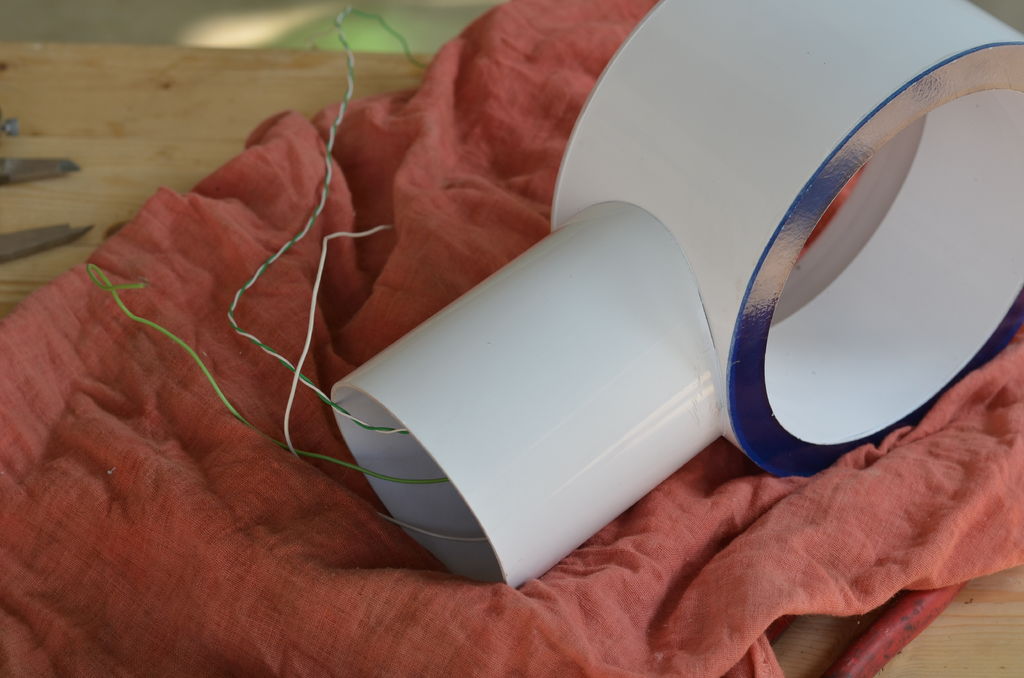
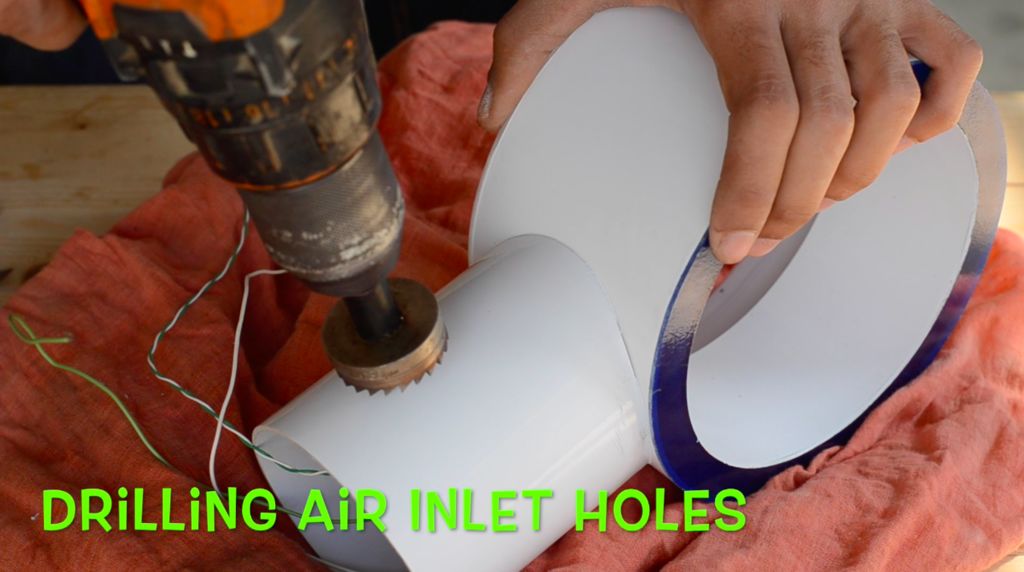
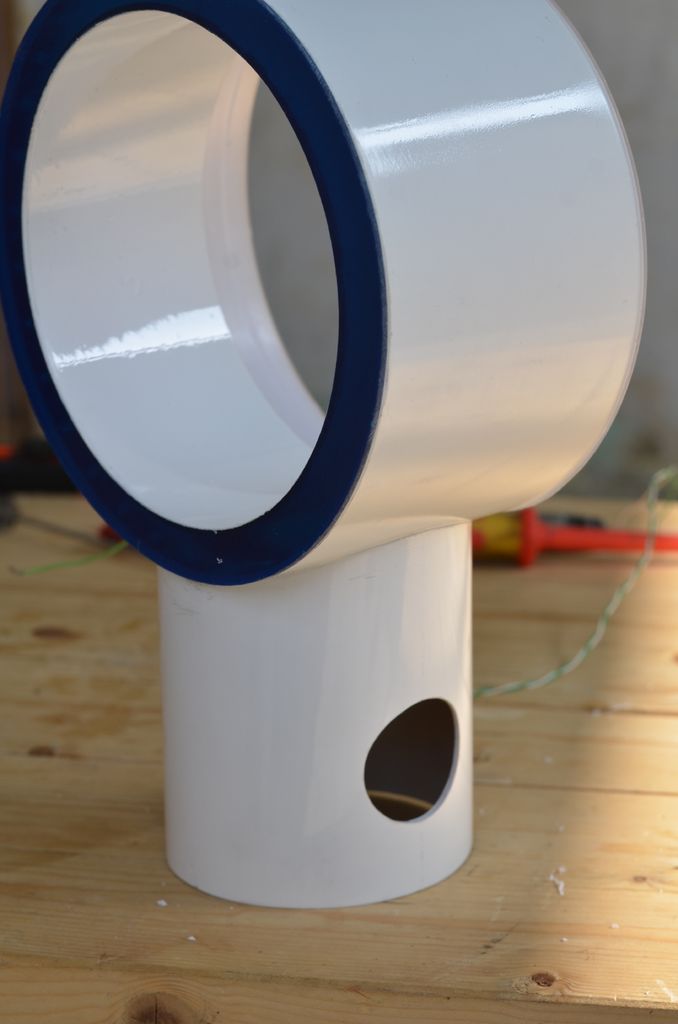
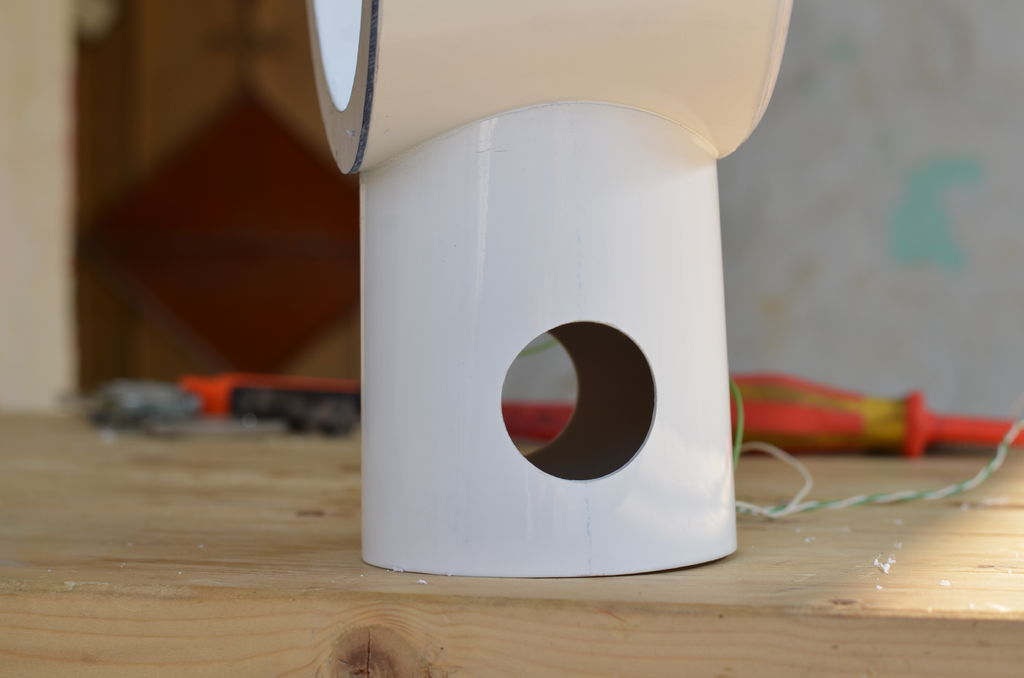
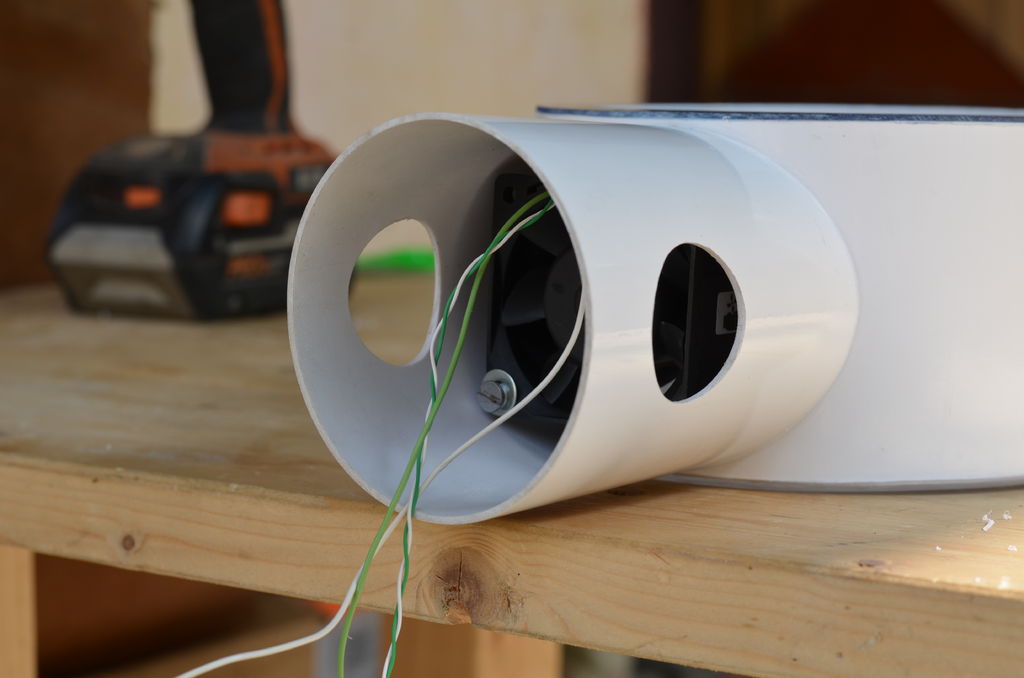
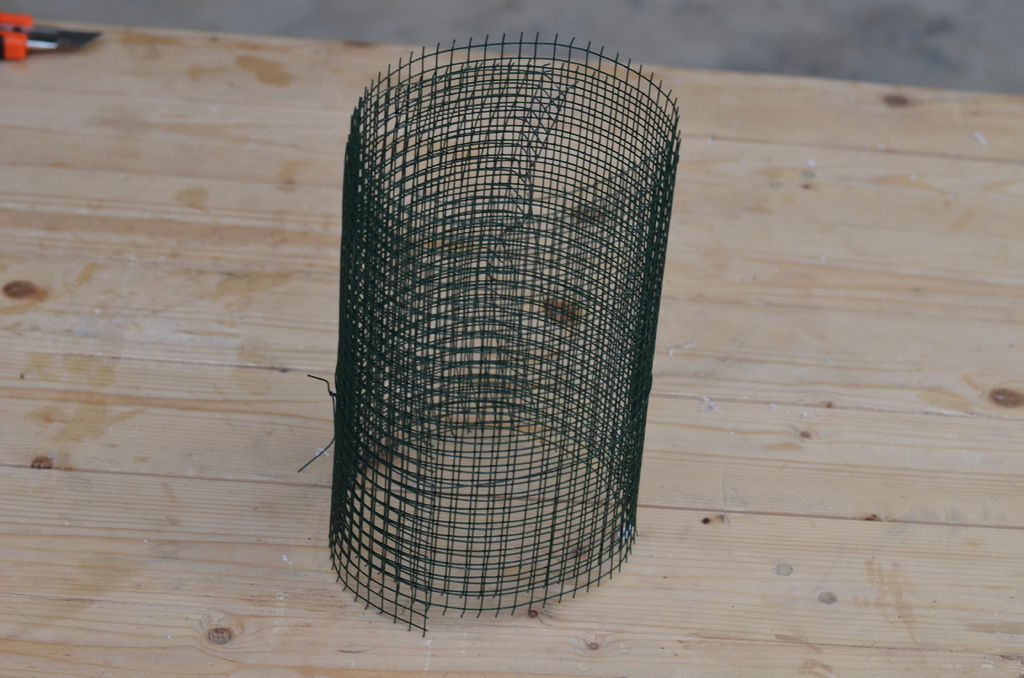
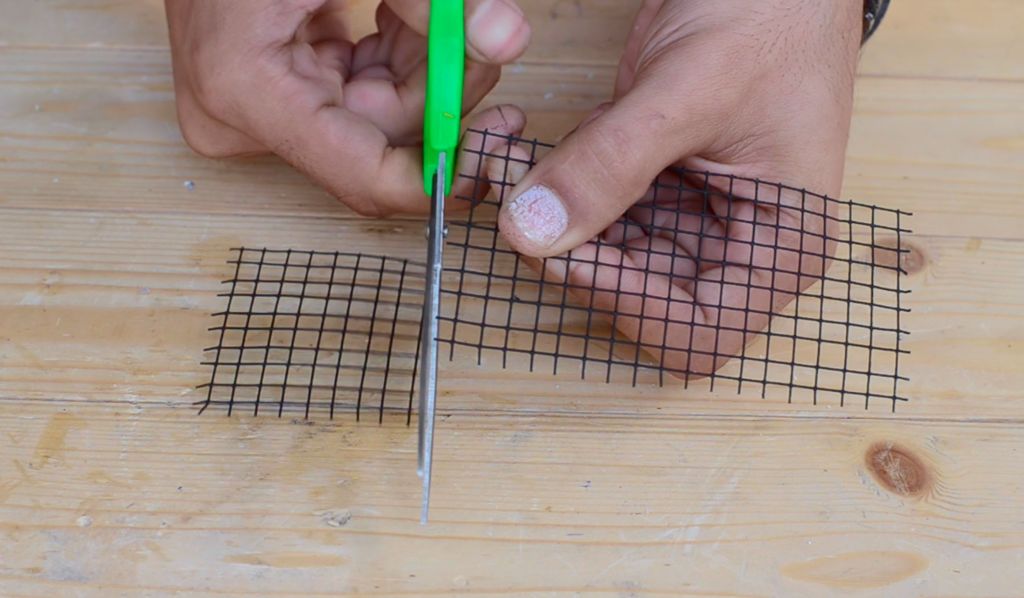
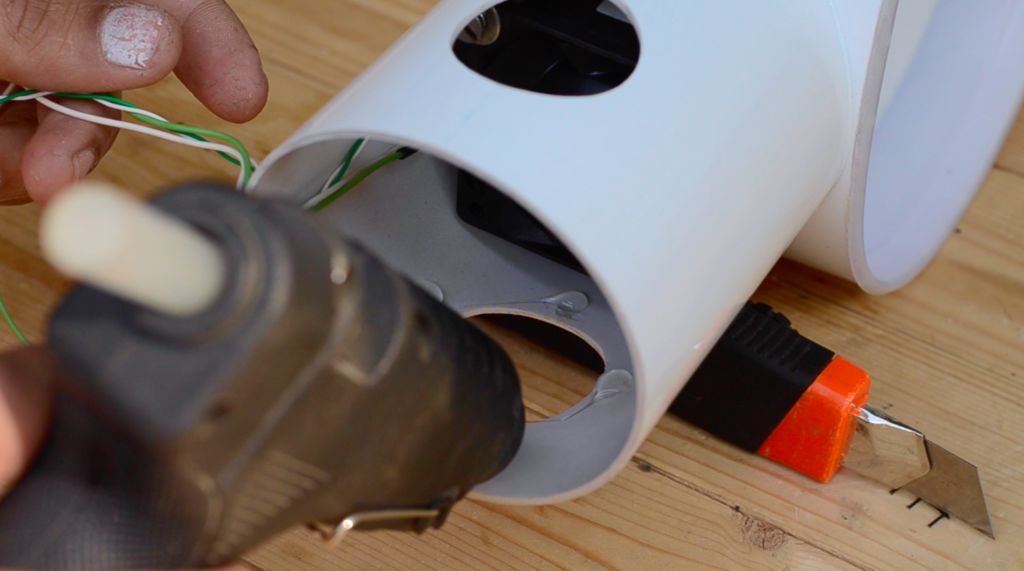
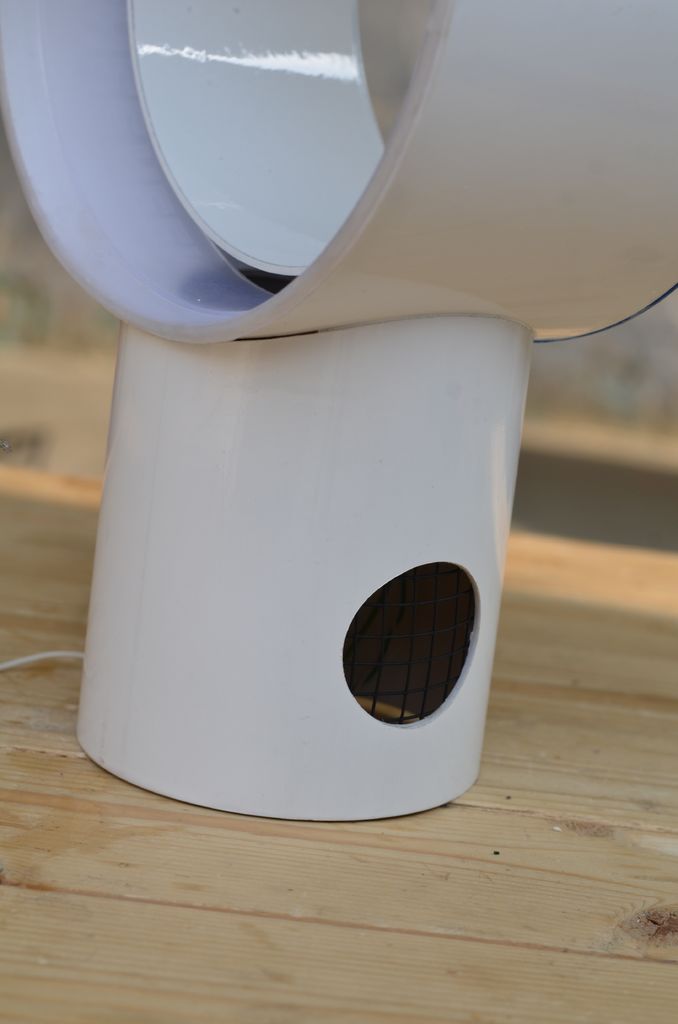
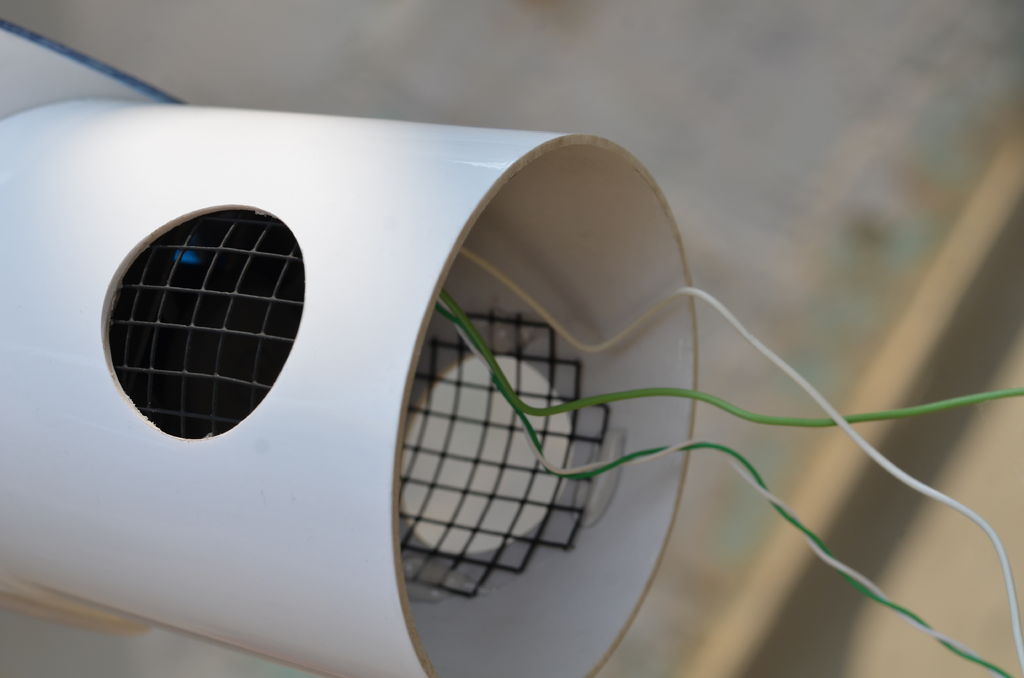
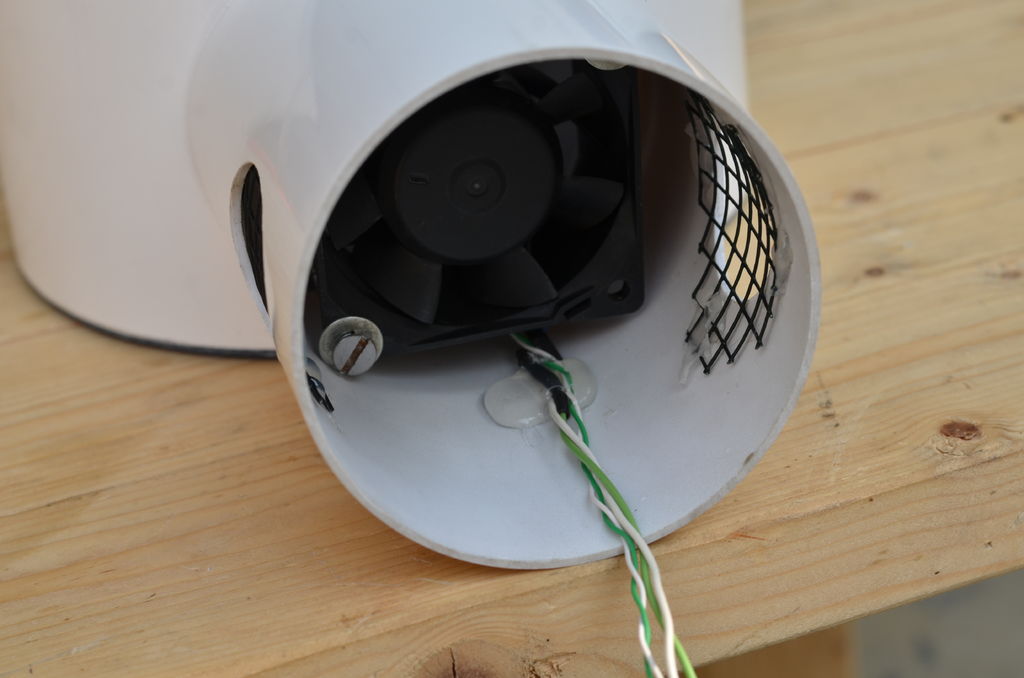
Пара входных отверстий сверлится прямо под вентилятором по обеим сторонам трубки-основания. Эти входные отверстия дадут возможность воздуху засасываться в основание.
Чтобы уберечь любопытных от повреждения конечностей, я приклеил металлические сеточки на оба входных отверстия. Сетки сперва были окрашены в матовый черный цвет и затем закреплены при помощи горячего клея.
Шаг 12: Модуль управления скоростью
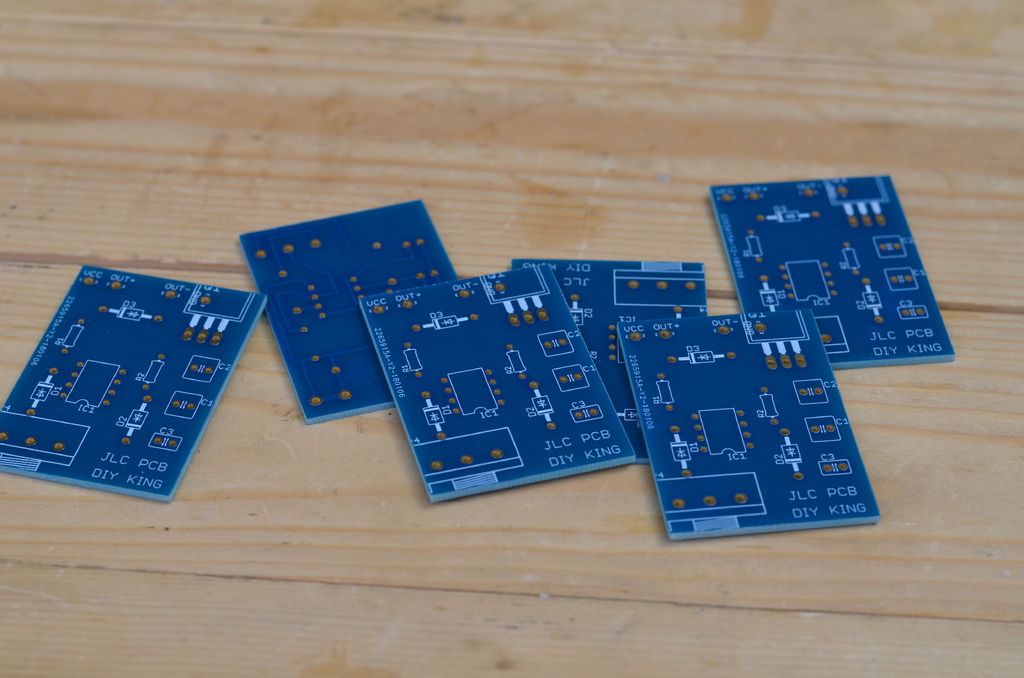
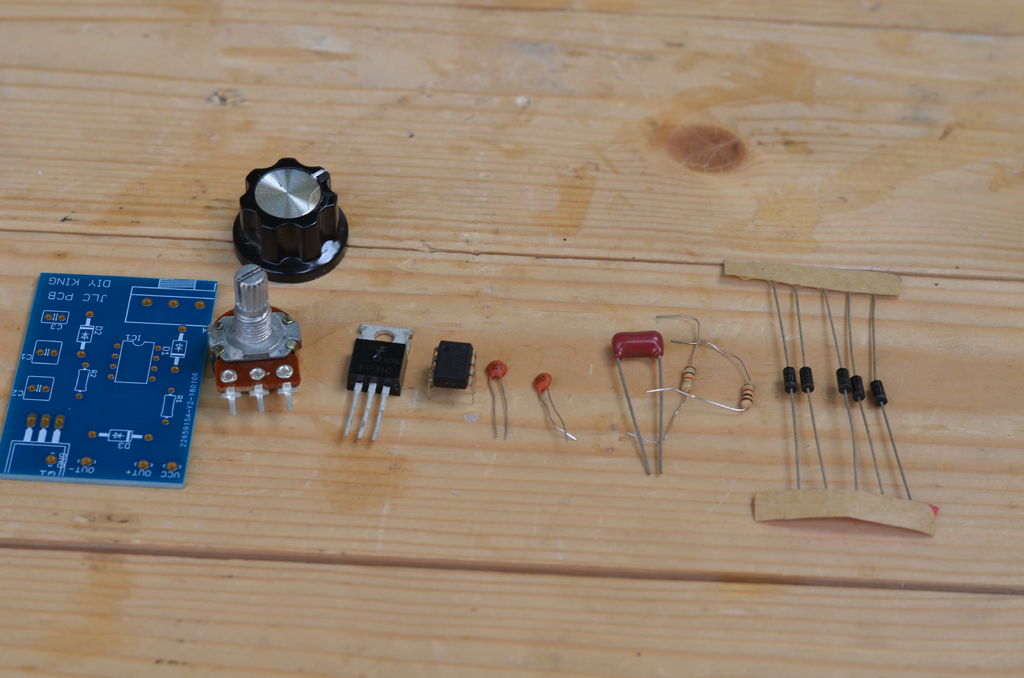
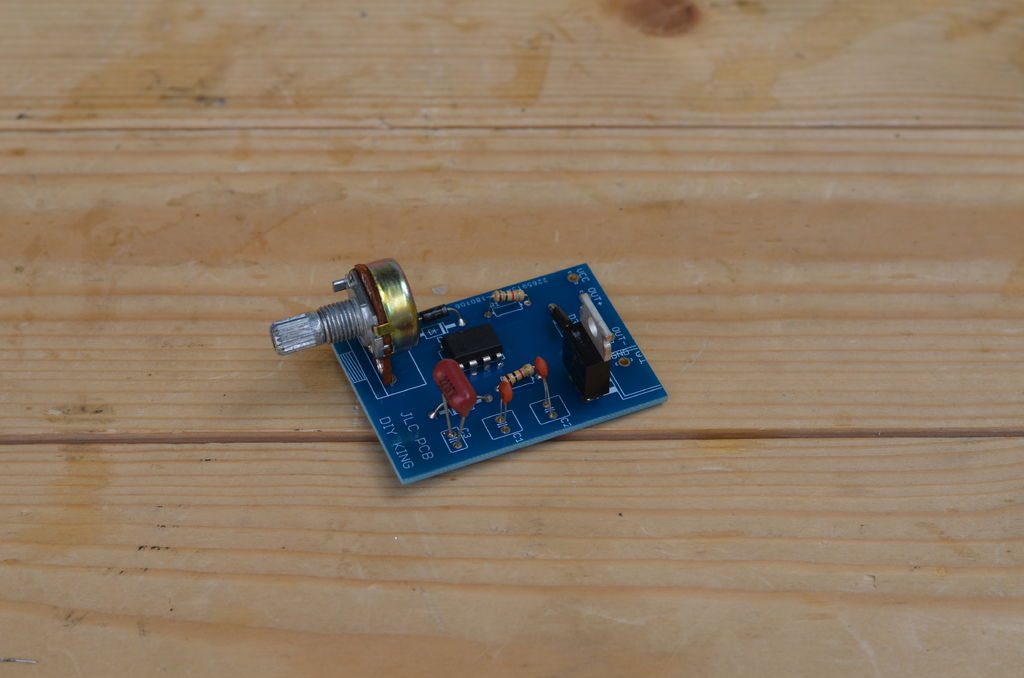
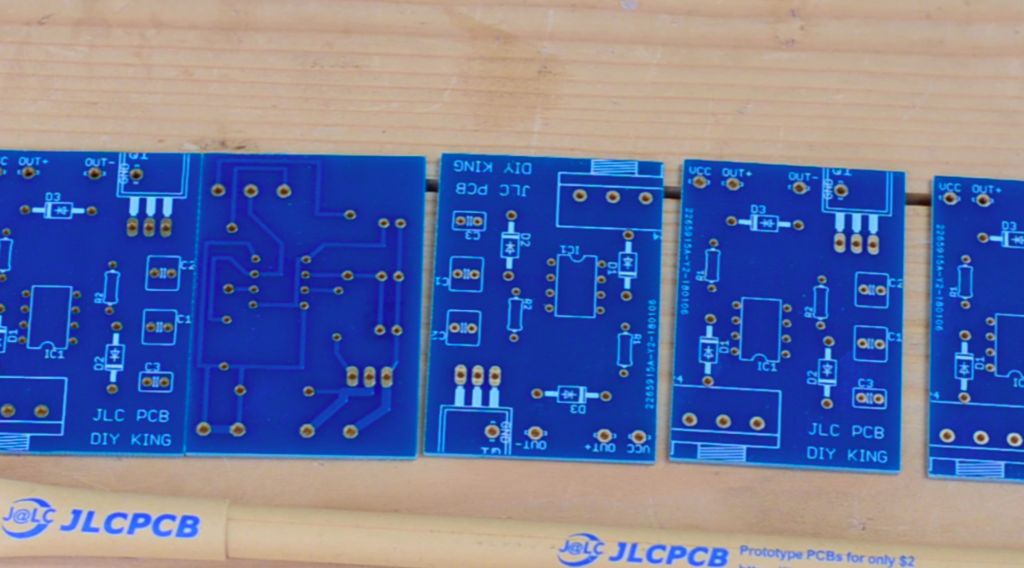
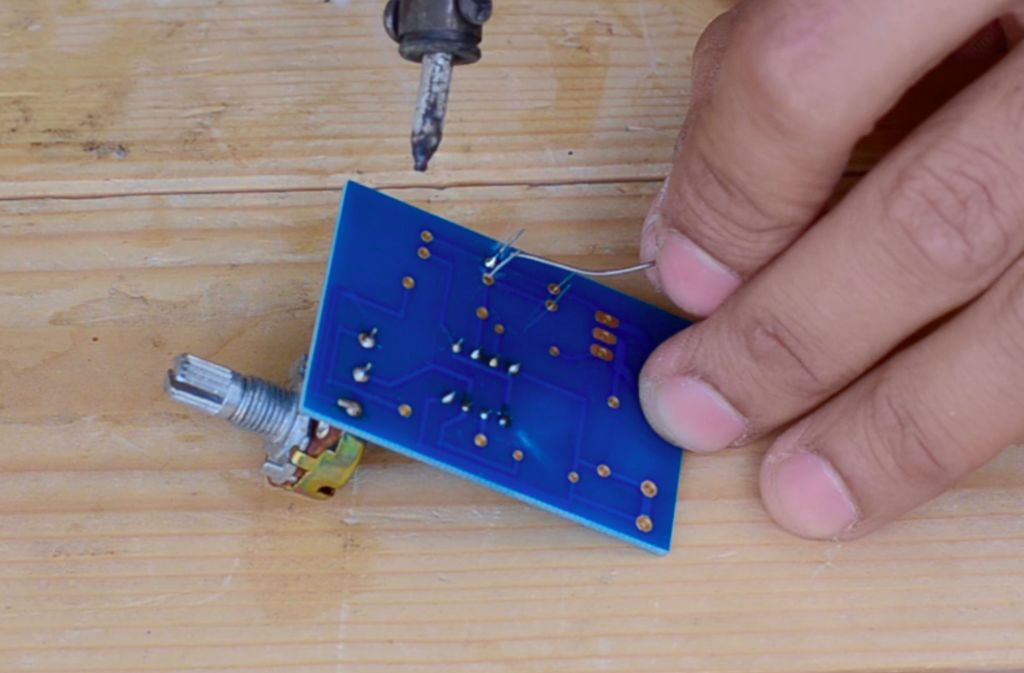
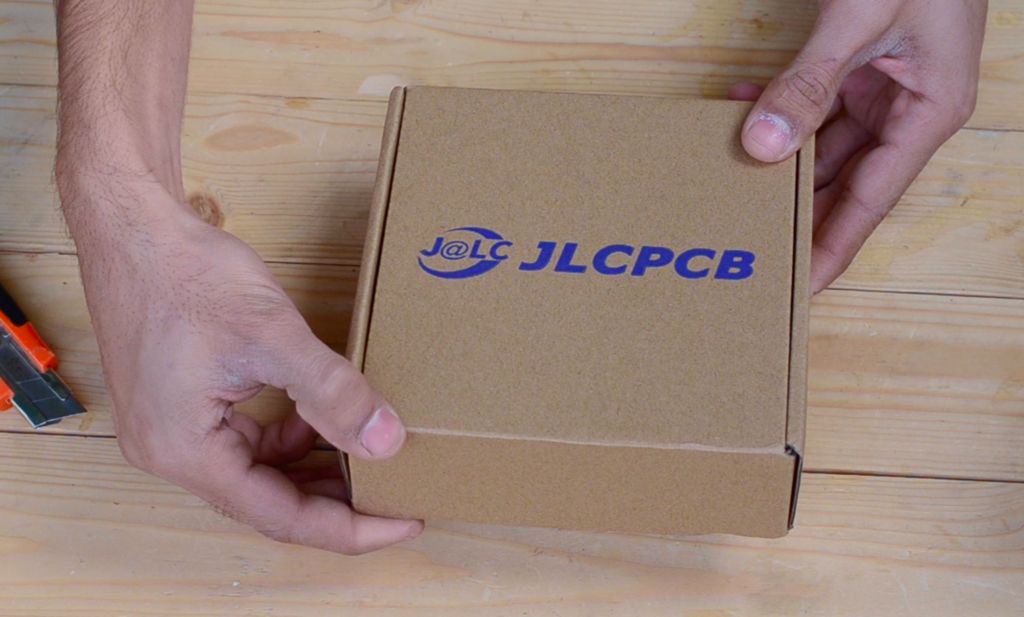
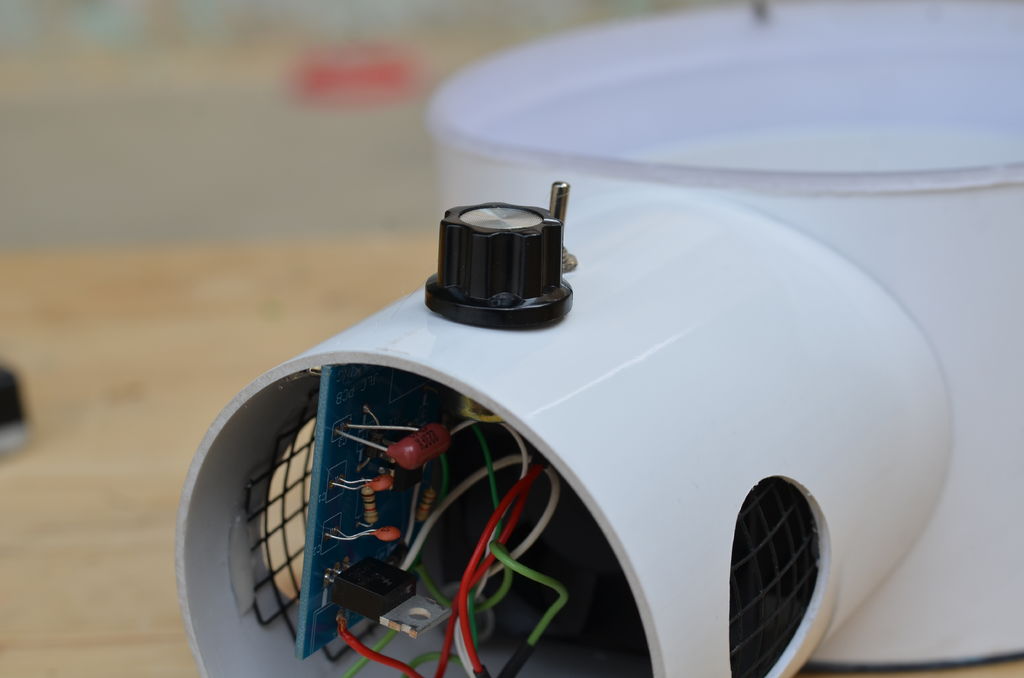
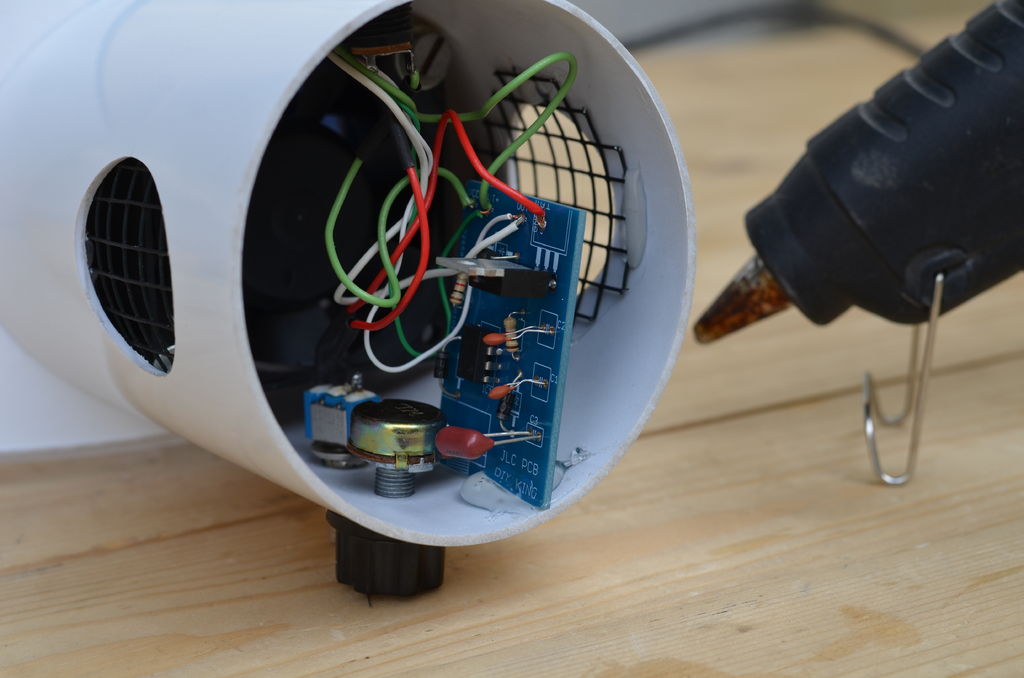
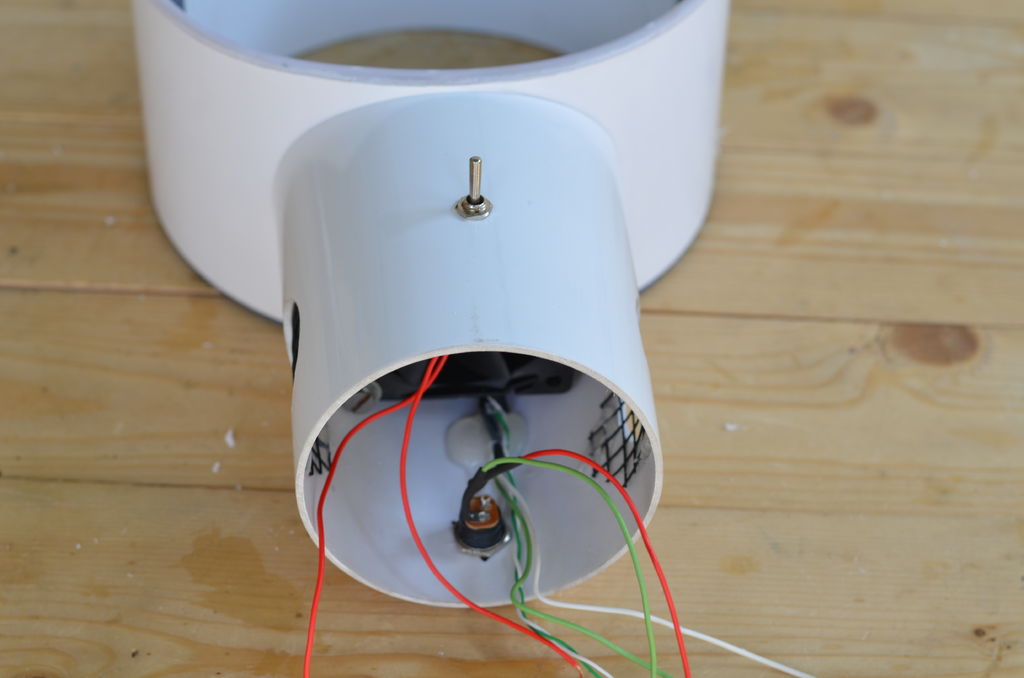
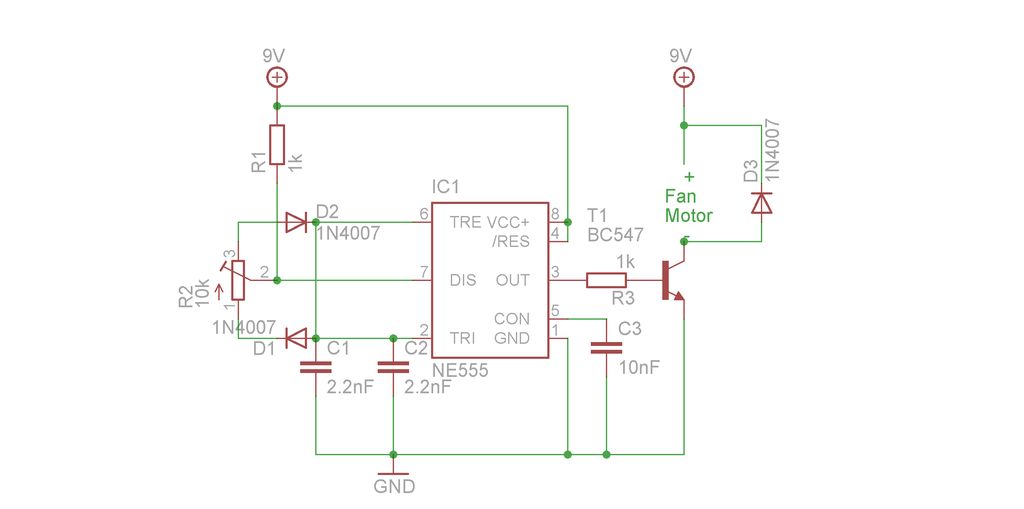
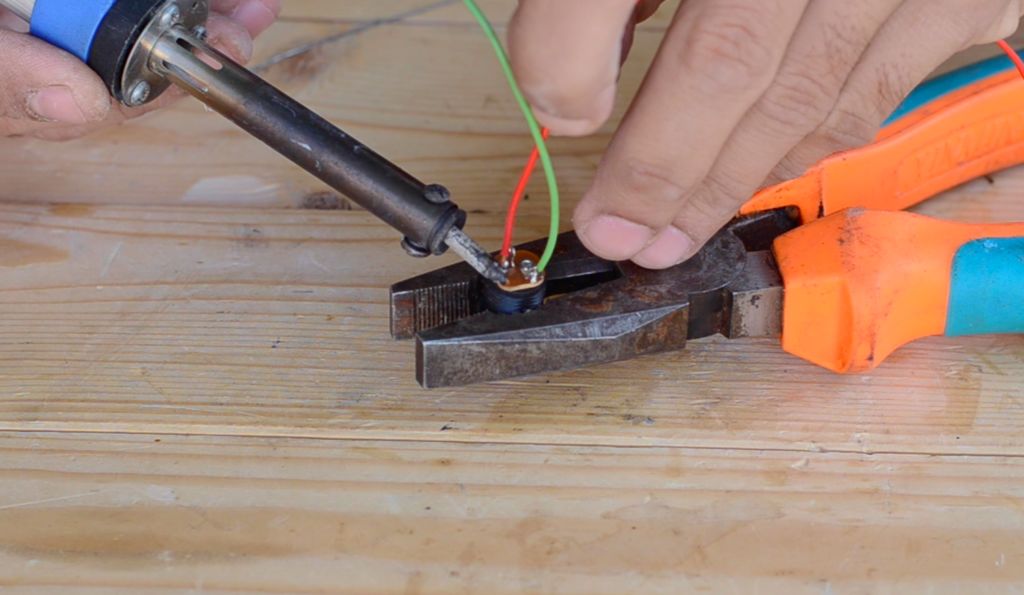
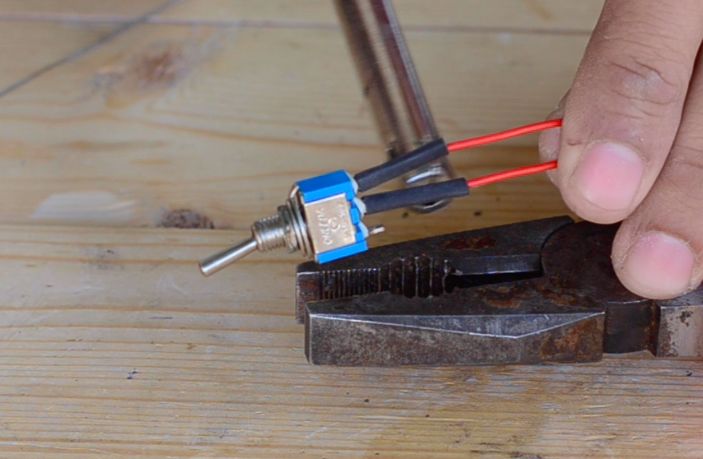
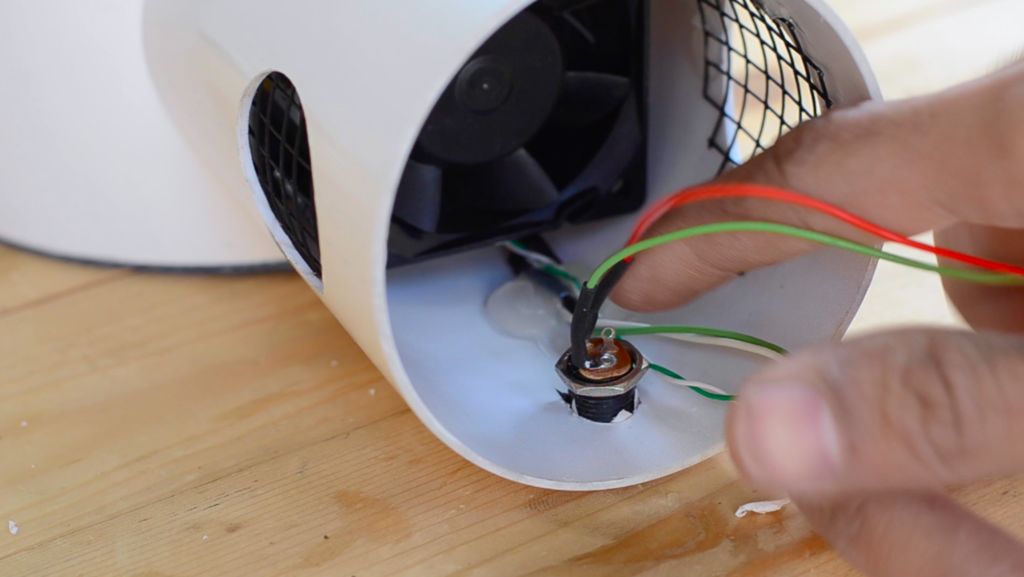
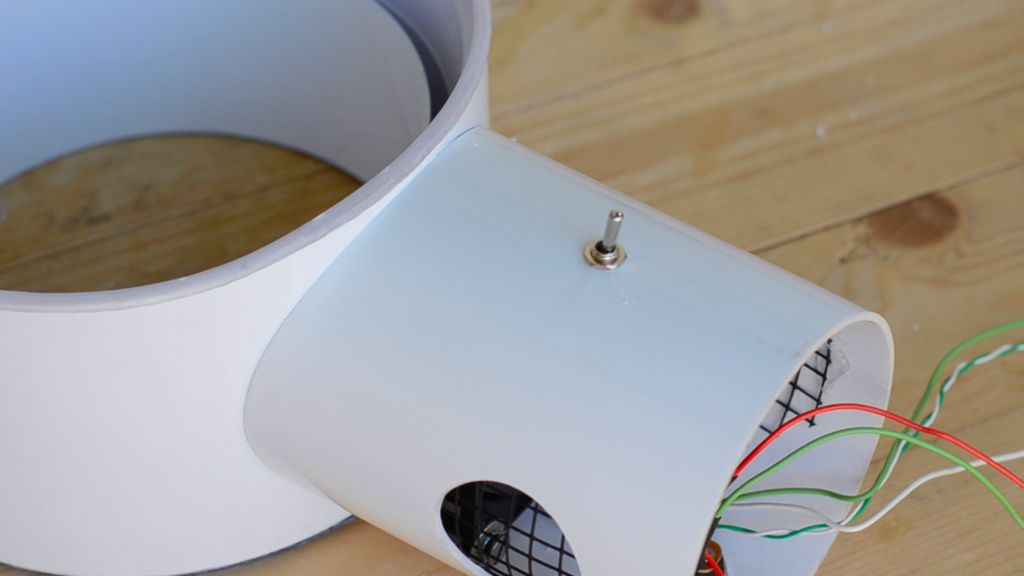
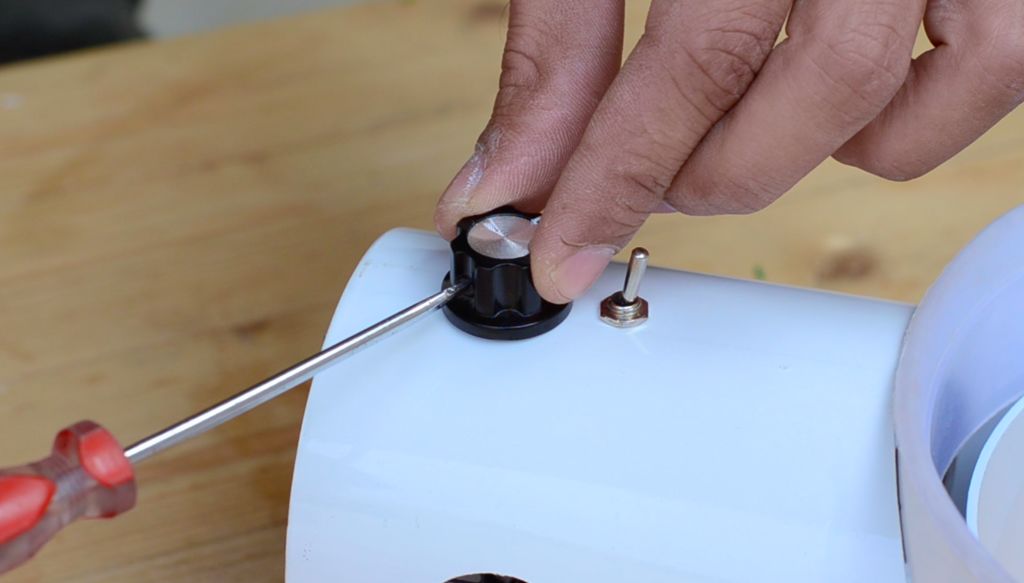
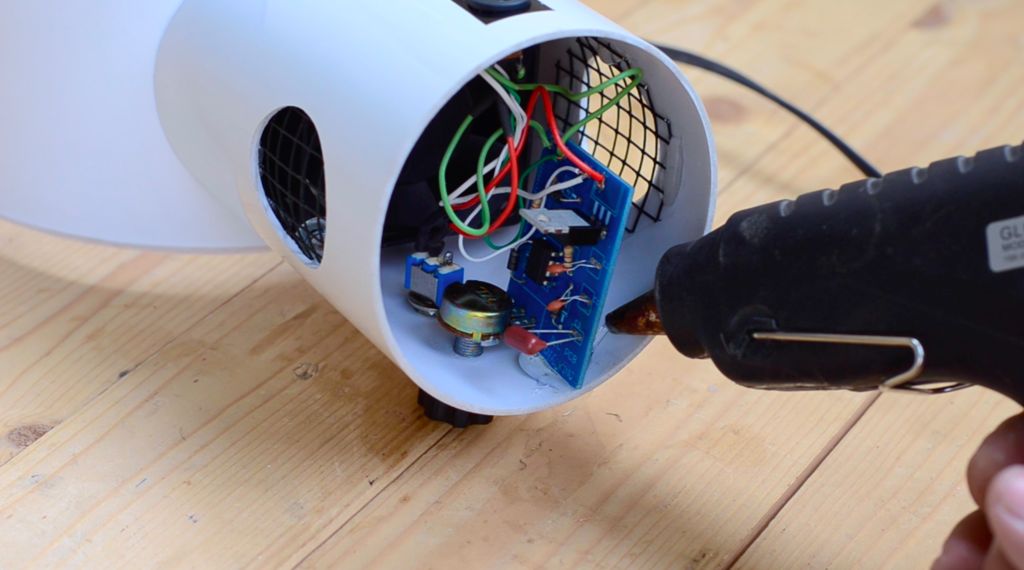
Так как проект подходил к завершению, я решил добавить в него ШИМ-модуль управления скоростью, чтобы можно было регулировать количество воздуха, выходящего из вентилятора, а также уровень издаваемой им громкости.
Чтобы осуществить свою идею, я спроектировал простую схему ШИМ-модуля управления скоростью, а также соответственно печатную плату в Автокаде.
Схема работает на базовых принципах. Она использует интегральную схему-таймер 555, которая в течение каждой секунды несколько раз переключает транзистор, а скорость переключения зависит от сопротивления, создаваемого потенциометром. Таким образом, поворачивая ручку переключателя, мы можем регулировать импульс и тем самым контролировать скорость вентилятора.
Я прилагаю все данные, включая схему, спецификацию и файлы формата Гербер для схемы ШИМ, которые могут потребоваться для заказа платы через интернет на веб-сайте.
Кроме того, обратите внимание на ребят JLCPCB, поскольку они делают отличное предложение для первого заказа, вы можете заказать 10 печатных плат, включая бесплатную доставку при заказе всего от 2 долларов США.
После пайки всех компонентов на печатной плате я соединил её с потенциометром, ручка которого выглядывала с лицевой части основания вентилятора, и была оснащена кнопкой для регулирования скорости вентилятора.
Файлы
Шаг 13: Дно основания
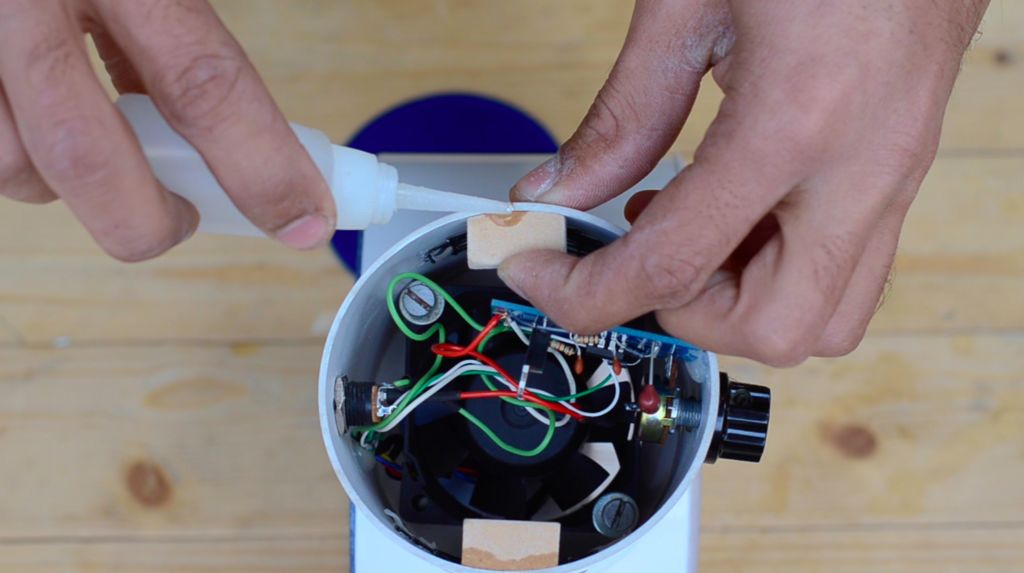
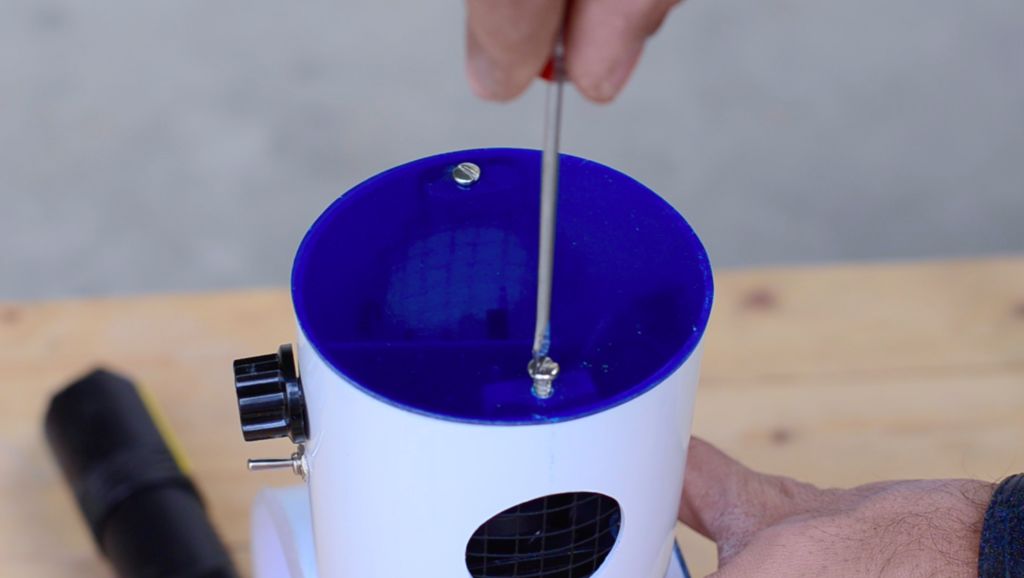
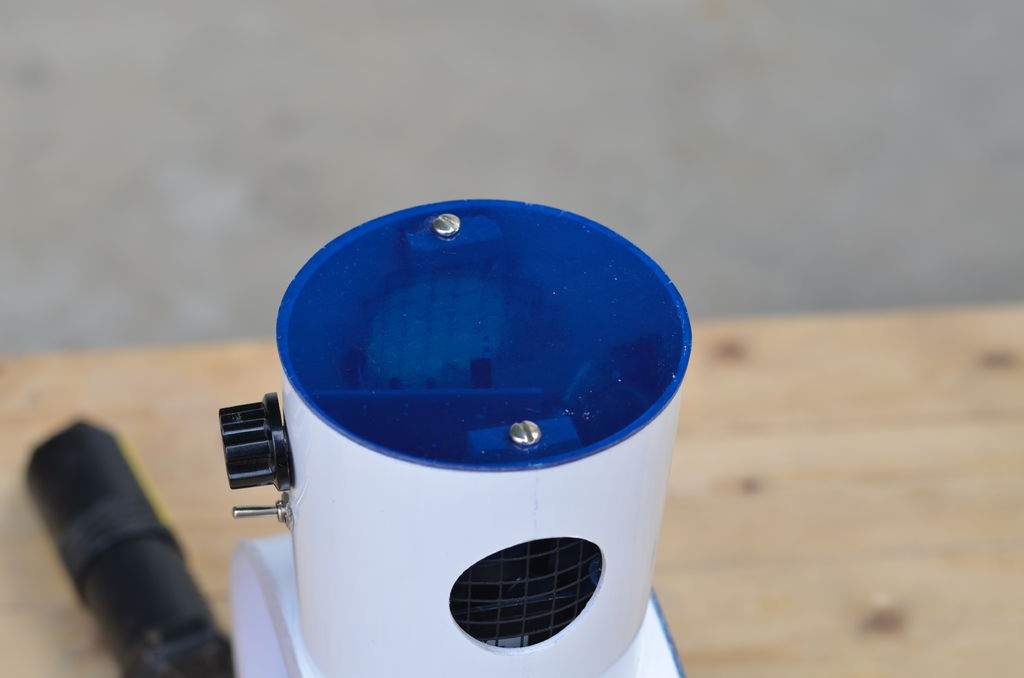
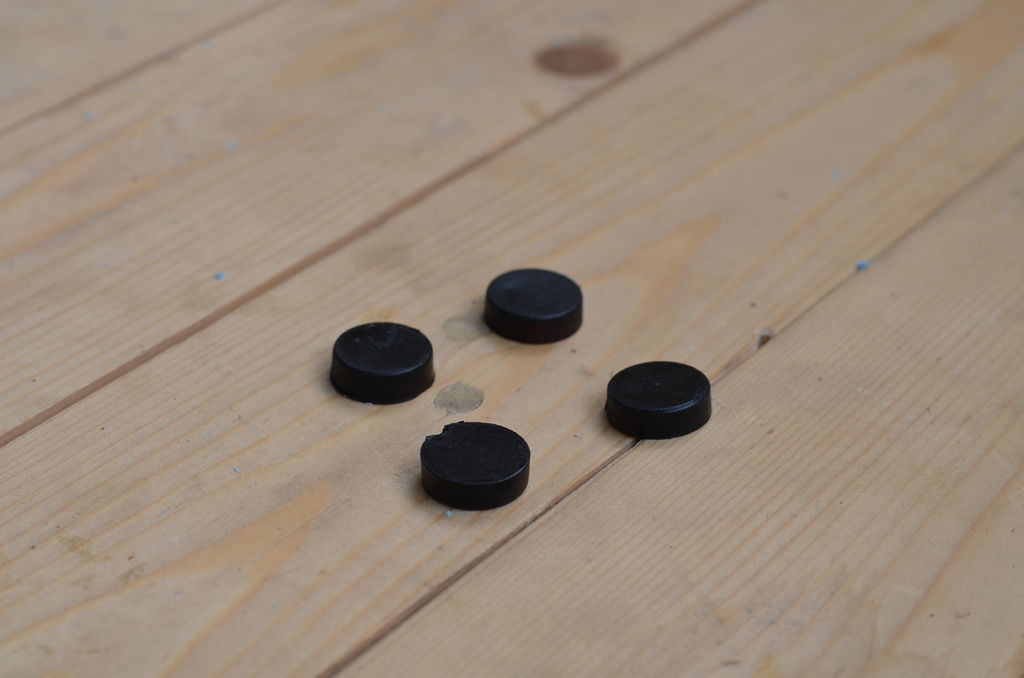
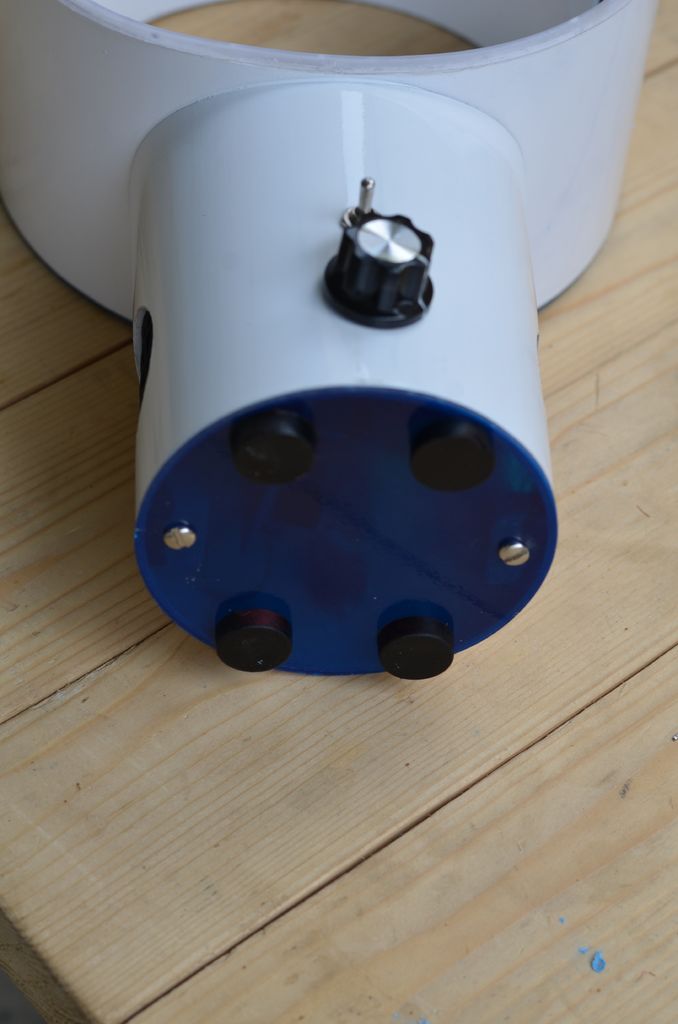
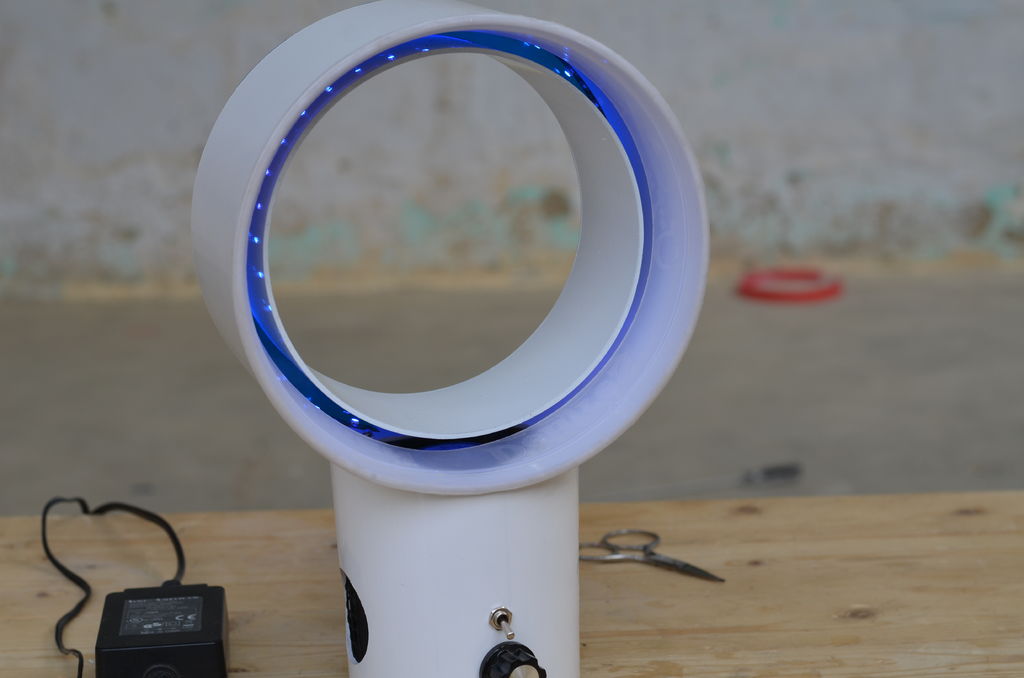
Чтобы завершить проект, я приклеил плату к основанию горячим клеем. Затем я вырезал лист фибергласа и прикрутил его к основанию снизу, точнее к двум деревянным брусочкам, которые я сперва приклеил внутрь основания.
Чтобы вентилятор не скользил туда-сюда во время работы, я приклеил к дну 4 резиновых кнопки.
Вентилятор готов к работе…
Шаг 14: Конечный результат
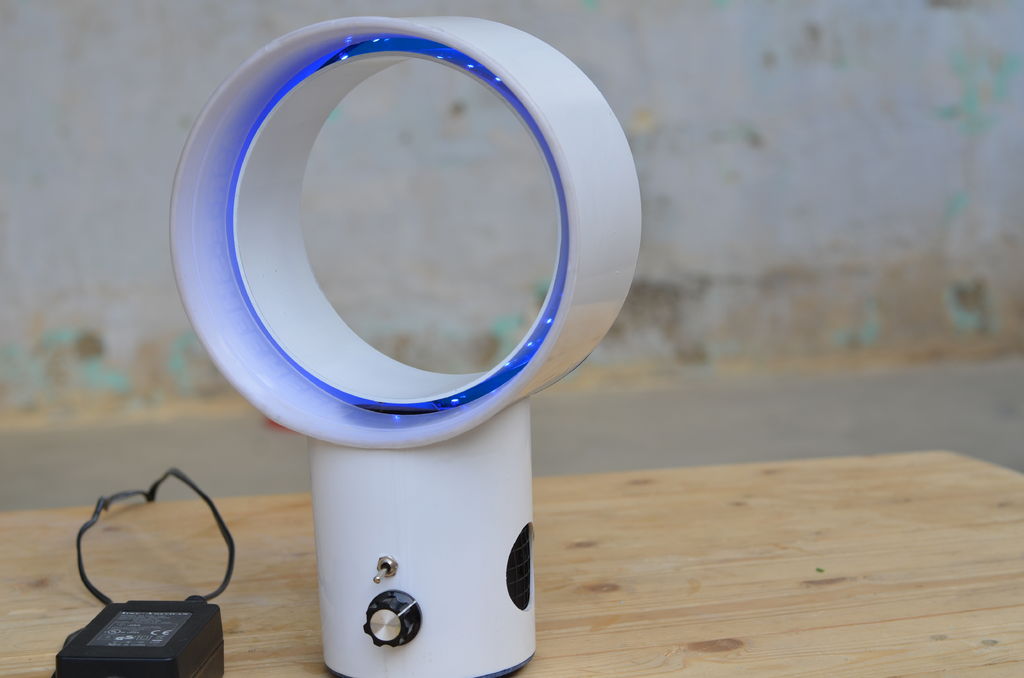
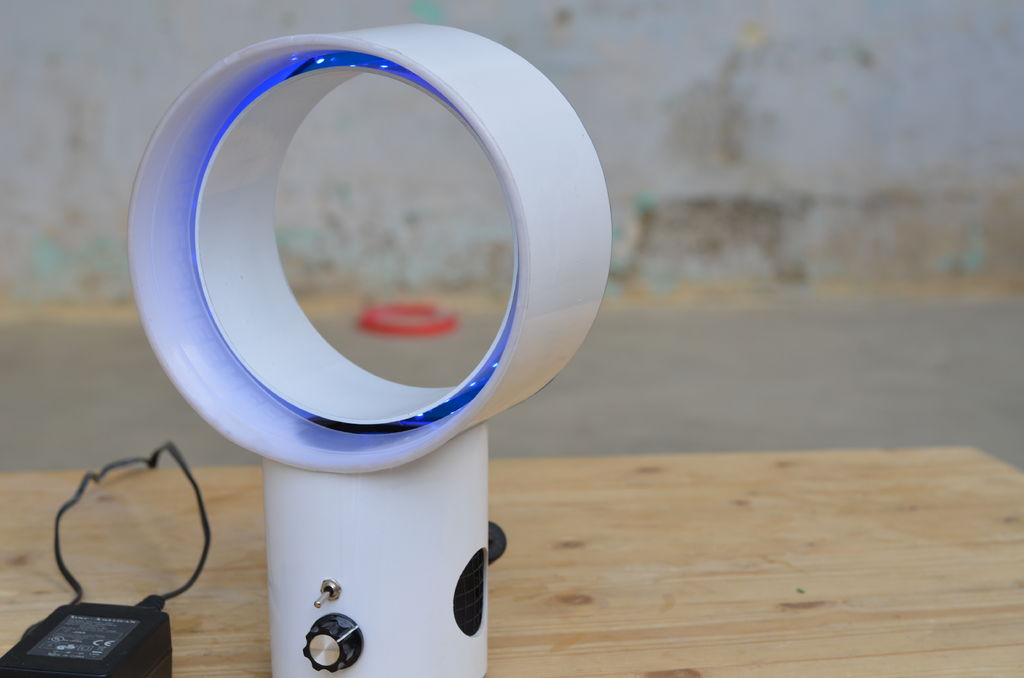
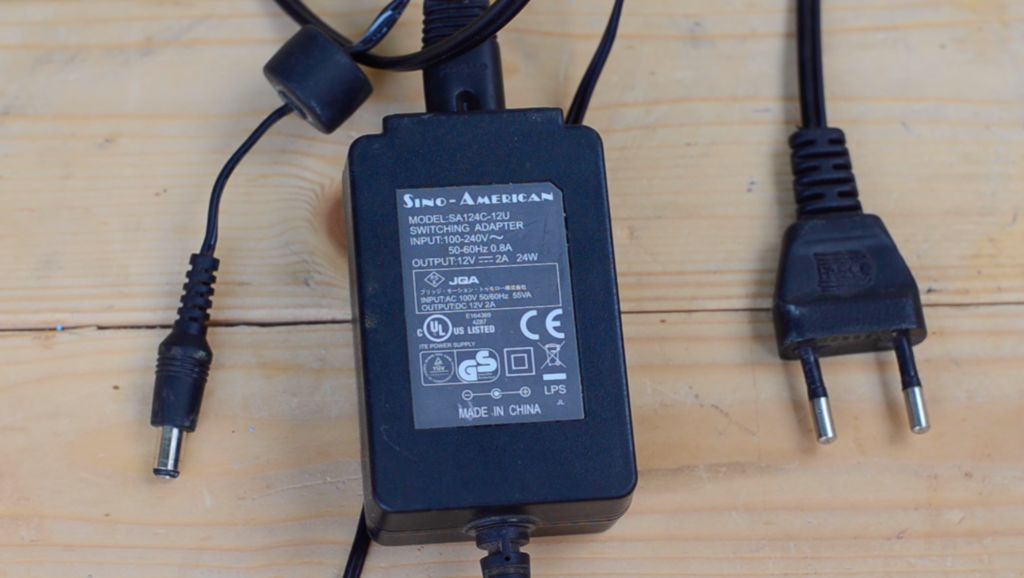
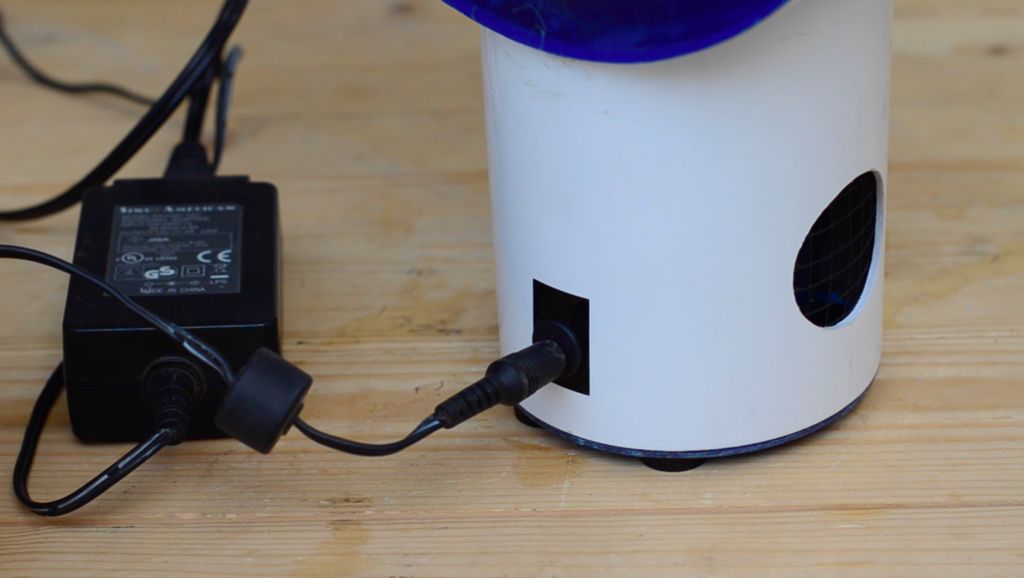
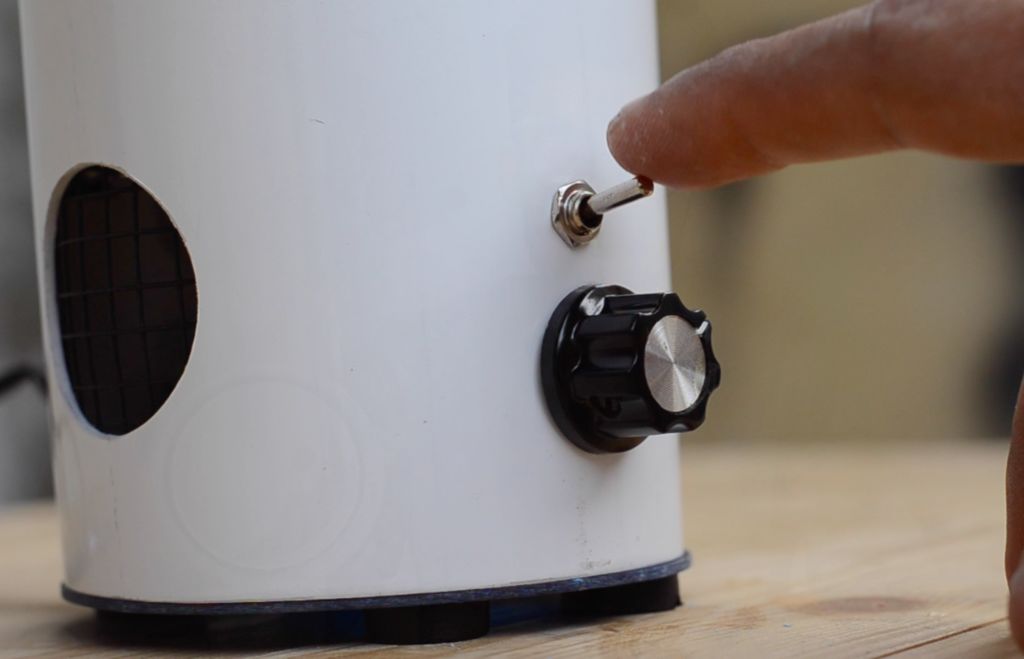
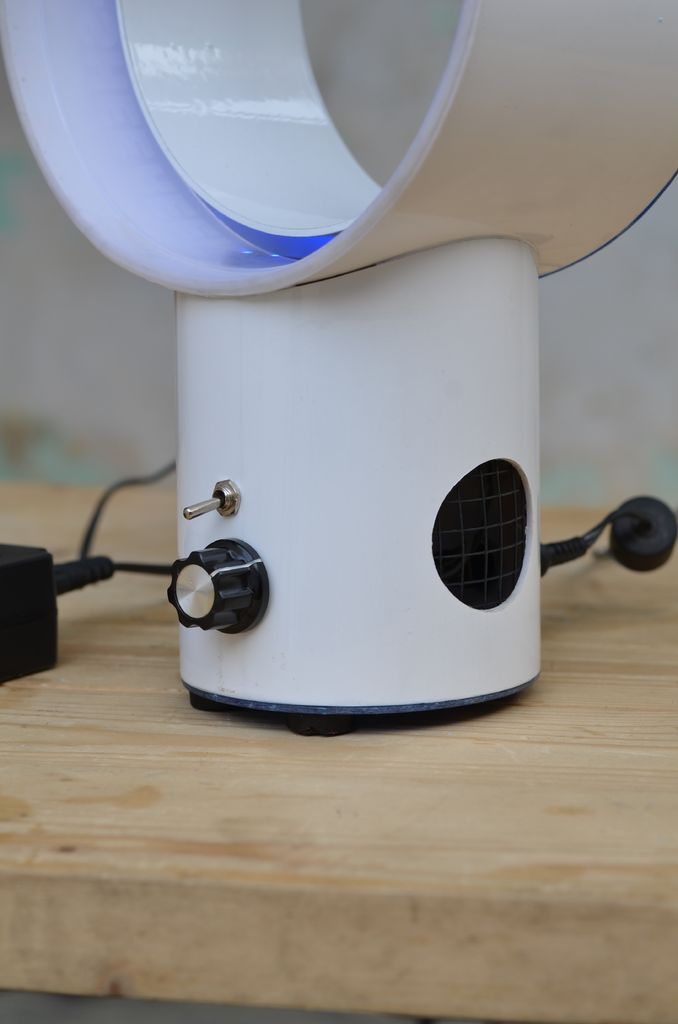
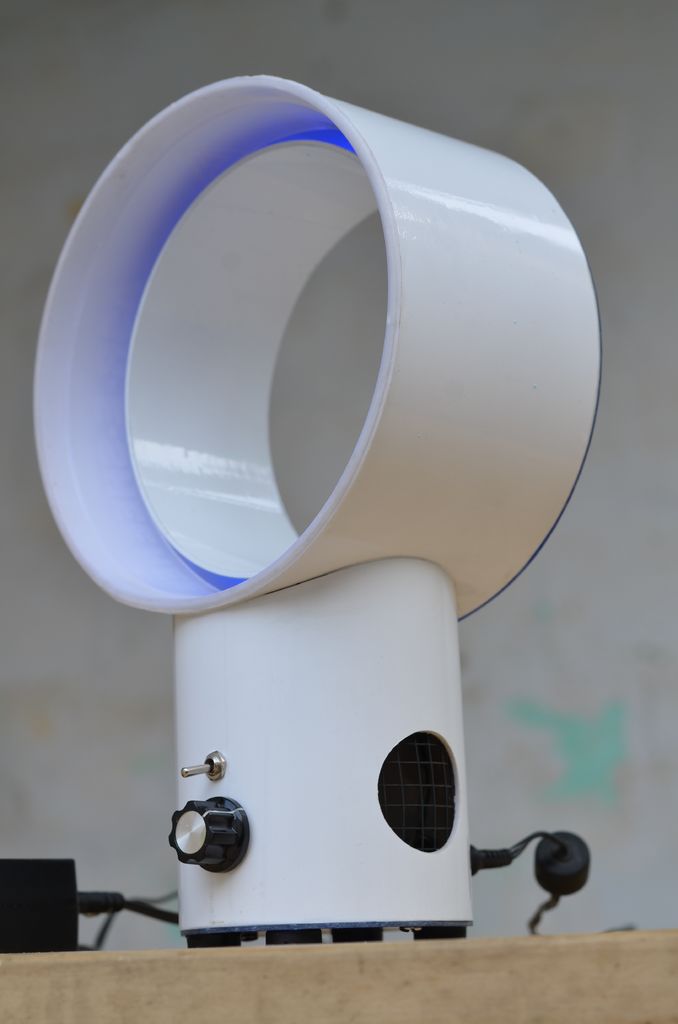
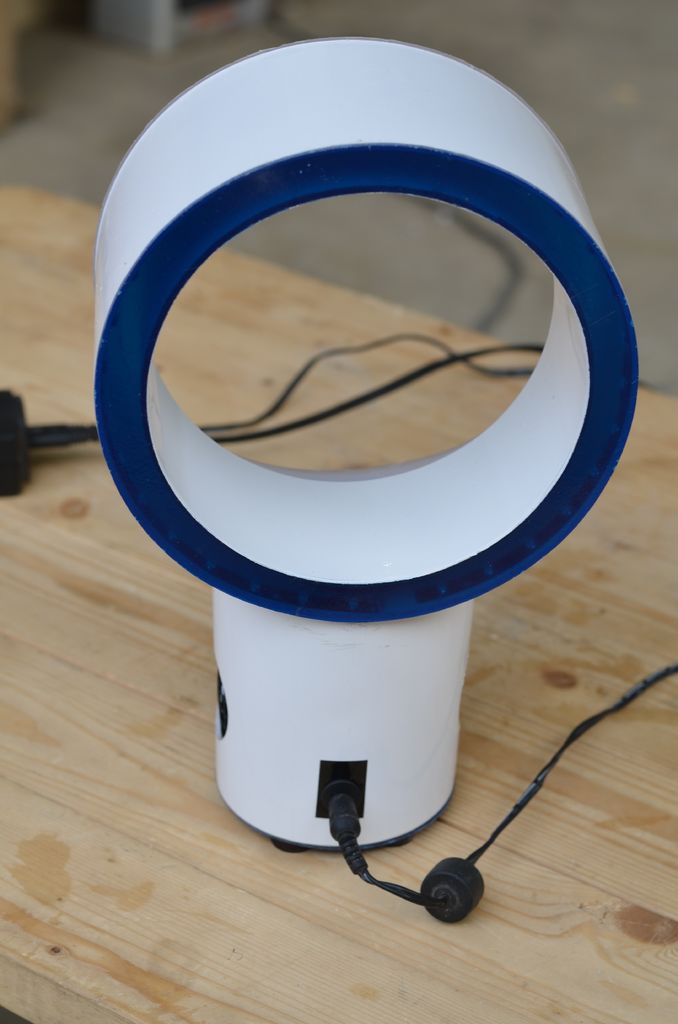
Проект прошел потрясающе. В начале у меня стояла непростая задача о создании подходящего корпуса без использования 3Д-принтера, но по мере продвижения всё стало идеально сходиться вместе, и, конечно же, та пластиковая чашка идеально подошла к моим нуждам.
Финальный результат очень крут, учитывая тот факт, что использовались очень ограниченные приспособления и общедоступное оборудование, я достиг почти совершенного результата…. Да, самодельный безлопастной вентилятор…
А до тех пор, развлекайтесь, создавая и изучая клёвые самодельные штуки.
С наилучшими пожеланиями, Король DIY.