Пресс используется не часто, но если в нем возникла нужда, то заменить его нечем. Когда мне понадобился гидравлический пресс, я изучил цены на рынке и пришел к выводу, что мне самому не сложно разработать чертежи и сделать мини пресс своими руками.
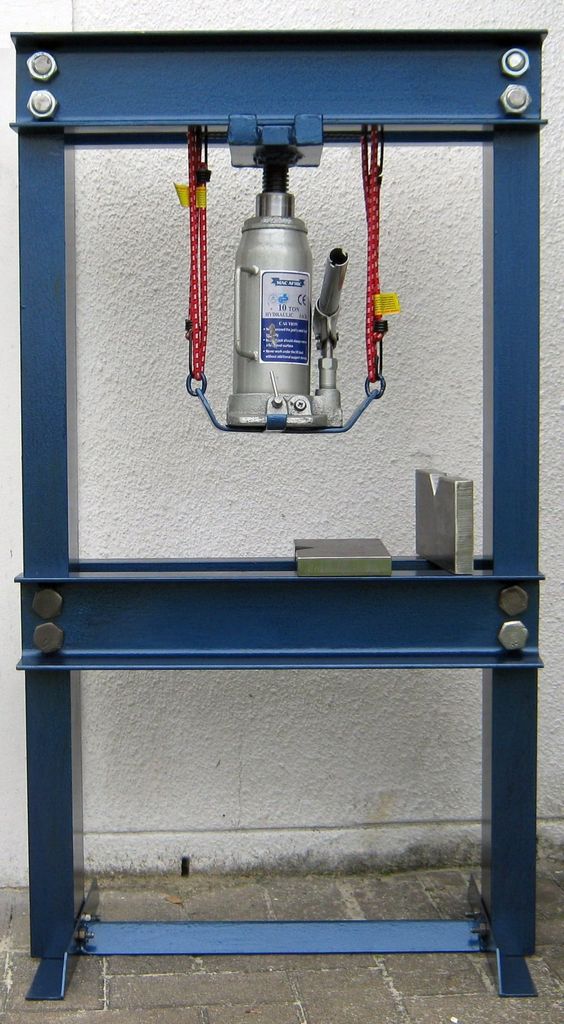
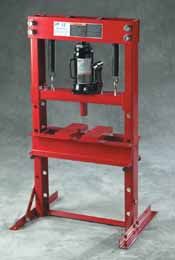
Практика показала, что это довольно легко – немного сварки, сверления, резки и шлифовки, и перед вами самодельный пресс из домкрата на 10 тонн.
После изучения материалов о прессах я выделил следующие моменты в дизайне и функциональности кустарных конструкций:
- Лебедка, задуманная для понятия нижней рабочей перекладины, по факту практически никогда не используется.
- При изготовлении пресса 10 т с неподвижным гидроцилиндром, без бокового смещения, все должно быть хорошо отцентровано.
- Использование настольных прессов ограничено из-за небольших размеров, а большие по размеру напольные очень тяжелы и занимают много места.
- Возвратные пружины на прессе упрощают работу с семикилограммовым домкратом.
- Манометр, хоть и желателен, не является необходимостью.
Я решил сделать механический пресс средних размеров, что-то среднее между напольным и настольным агрегатом, также я хотел иметь возможность демонтажа домкрата, если он понадобится мне где-то еще.
Содержание статьи
Шаг 1: Меры безопасности
Так как стаканный домкрат будет привариваться, используйте одежду с длинным рукавом, сварочные перчатки и защитную маску для дуговой сварки. Также учтите, что при дуговой сварке можно получить УФ-ожоги не закрытых участков кожи.
Также необходимо обуть специальную защитную обувь (как минимум кожаные ботинки). Очень хорошо, если у вас есть возможность провести сварку на улице. Не забывайте, что при сварке оцинкованного металла выделяется очень много ядовитого дыма.
Защитная экипировка для шлифовальных работ и резки стали включает в себя: защиту для глаз и слуха. При работе УШМ вы скоро услышите звон в ушах, если будете работать без должной защиты, не говоря о снопе искр, который разлетится по помещению. Искры могут срикошетить от стен и попасть в зазор между защитными очками и лицом, это очень опасно. Рабочие перчатки защитят руки от случайного касания кордщетки, и снизят уровень вибрации от УШМ при резке металла.
При сверлении отверстий коронкой 20 мм будет много искр, поэтому нужны защитные очки. Чтобы при сверлении коронкой металл не начал крутиться, его нужно зафиксировать с помощью тисков.
Шаг 2: Составные части и инструменты
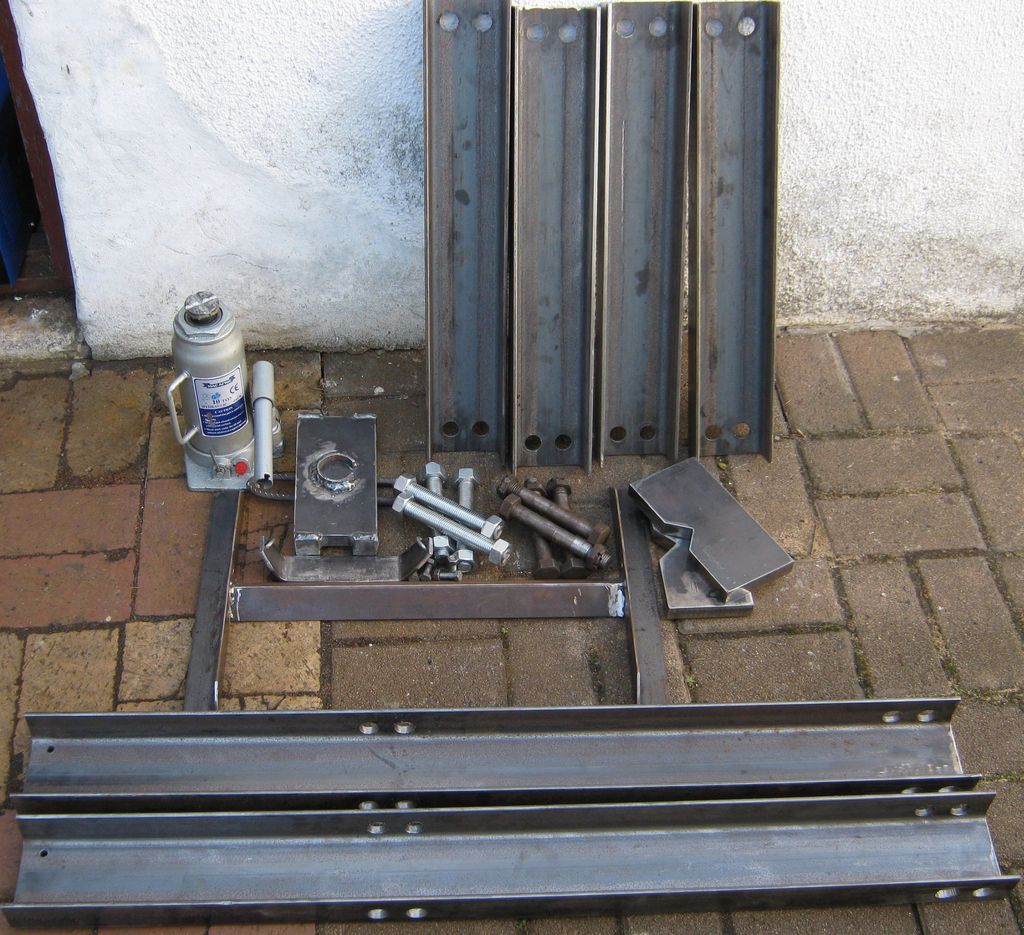
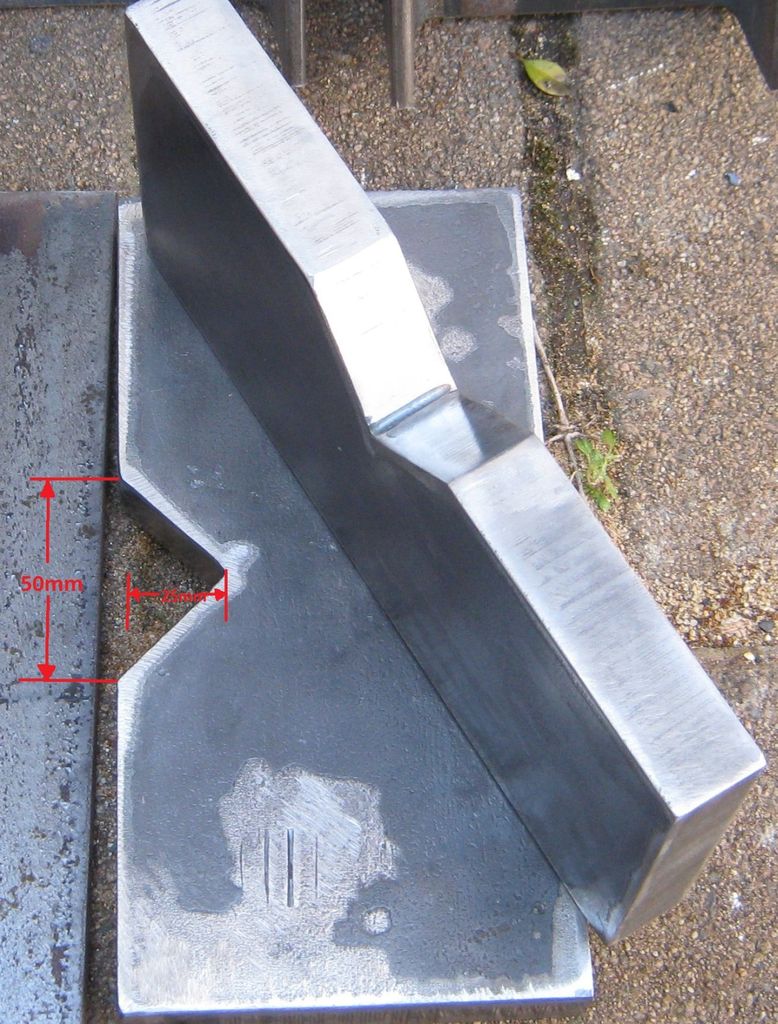
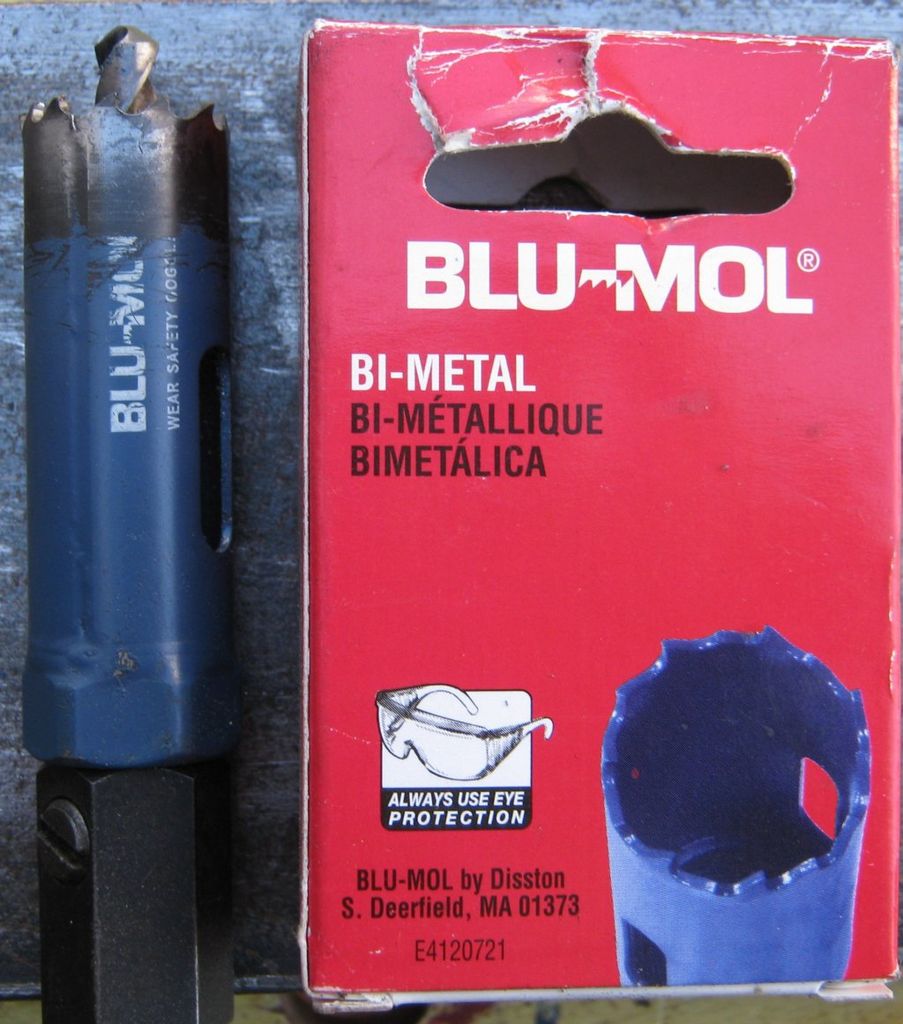
Инструменты:
- дуговой сварочный аппарат
- сверлильный станок с биметаллической коронкой 20 мм, рекомендуемая скорость — 440 оборотов в минуту
- УШМ с набором отрезных и шлифовальных дисков 115 мм
Составные части:
- 4 метровых швеллера с уклоном внутренних граней полок, 100х50 мм. Он дешевле и прочнее, чем профиль с прямыми бортиками.
- 2х1 м боковые стойки
- 4х560 мм поперечины (у меня был стальной профиль 2,24 м, и я просто разрезал его на 4 равные части).
- 1,2 м 30 мм равнополочный уголок для нижних опор
- 460 мм уголок для поперечной стяжки
- 2х350мм боковых скобы
- 8х20 мм болты для перекладин (я использовал болты М20 и гайки М20)
- стаканный домкрат 10 т
- 1х200х100х20 мм верхняя скоба домкрата (сделана газовой резкой на заказ в специализированном отделе)
- 300х30 мм мягкая сталь для нижней скобы
- 2х200х100х20 стальных блока с V-образным вырезом (вырез можно сделать на заказ в специализированном отделе)
Шаг 3: Делаем основание
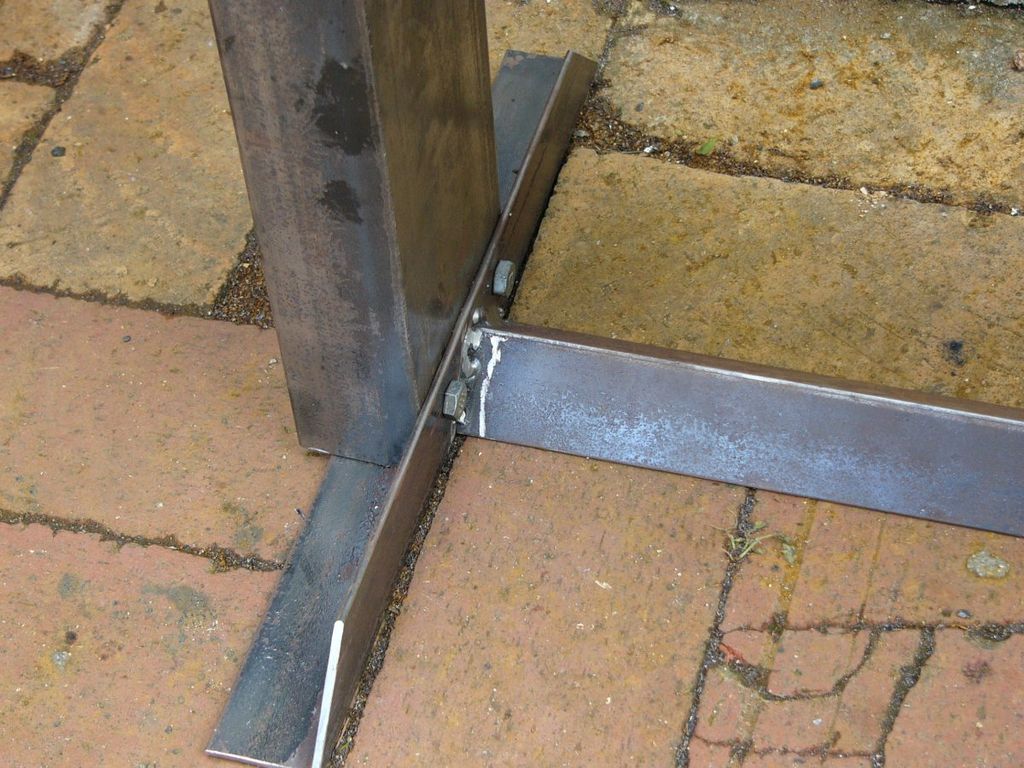
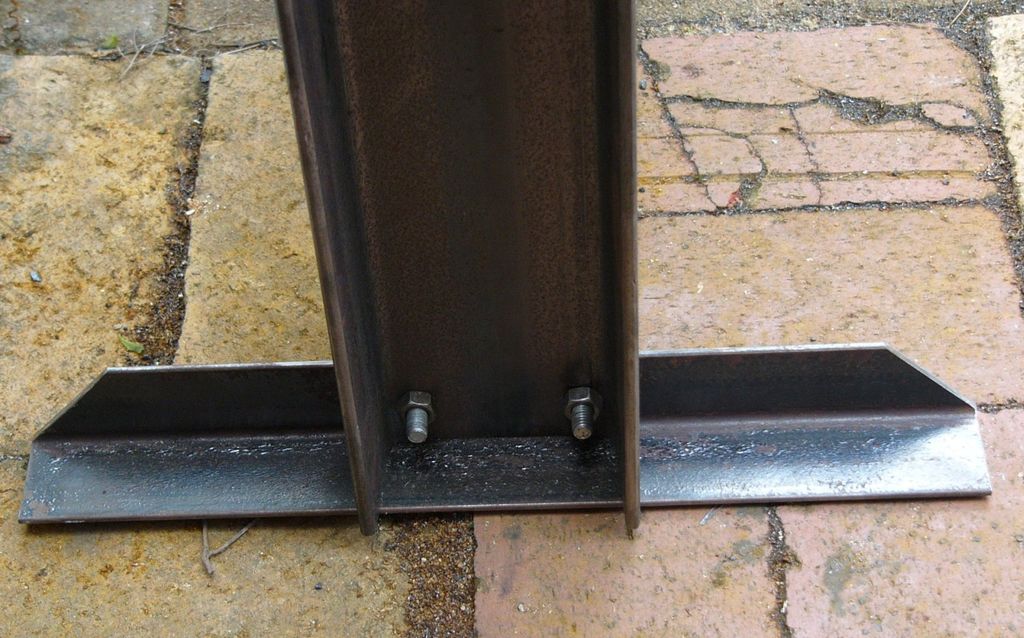
Исходя из того, что поперечные балки длиной 560 мм, длина поперечной стяжки должна быть 460 мм (расстояние между боковыми опорами). Расстояние между боковыми скобами в 350 мм показалось мне оптимальным. Потом я решил, что прежде чем приваривать поперечную стяжку, нужно просверлить 8 мм отверстия под болты. Сначала я отметил места на уголке (поперечная стяжка), где собирался просверлить отверстия, затем засверлился 2 мм сверлом. После я положил уголок сгибом вверх, чтобы обвести контур на боковой опоре.
Таким образом, я получил отлично отцентрованные отверстия, к которым подойдут только соответствующие отверстия на нижней опоре.
Шаг 4: Станина
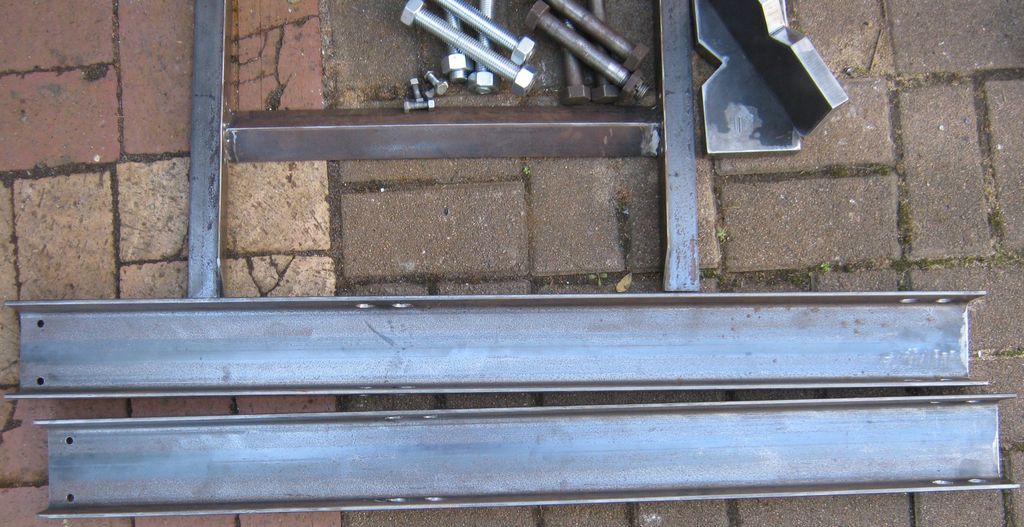
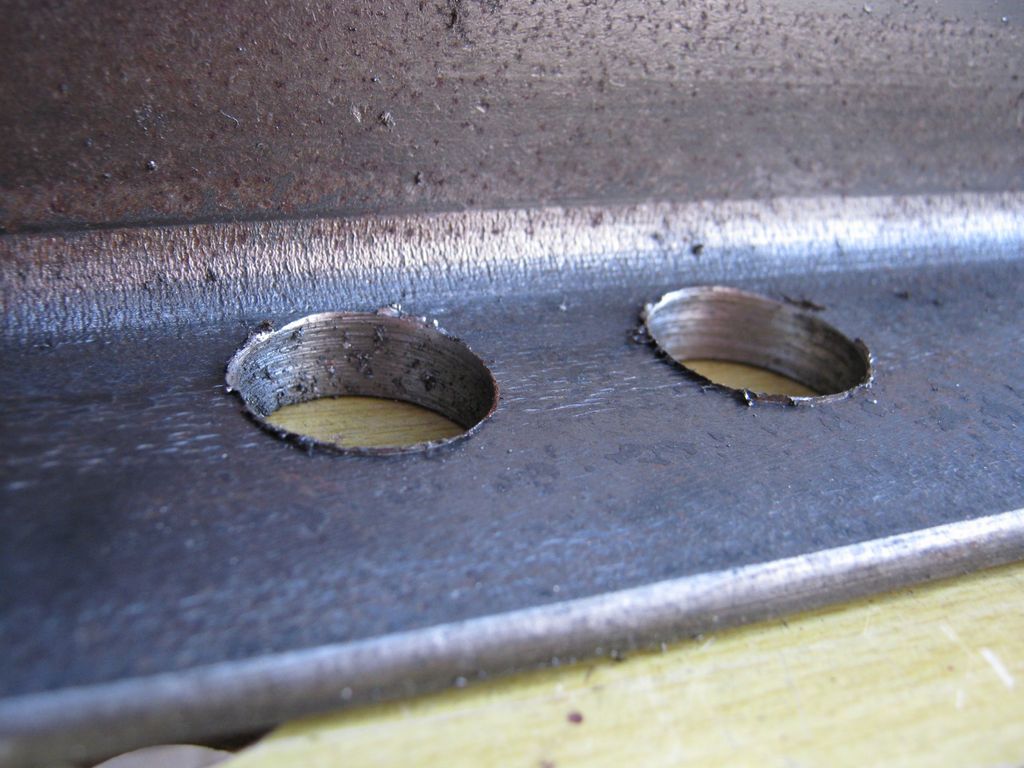
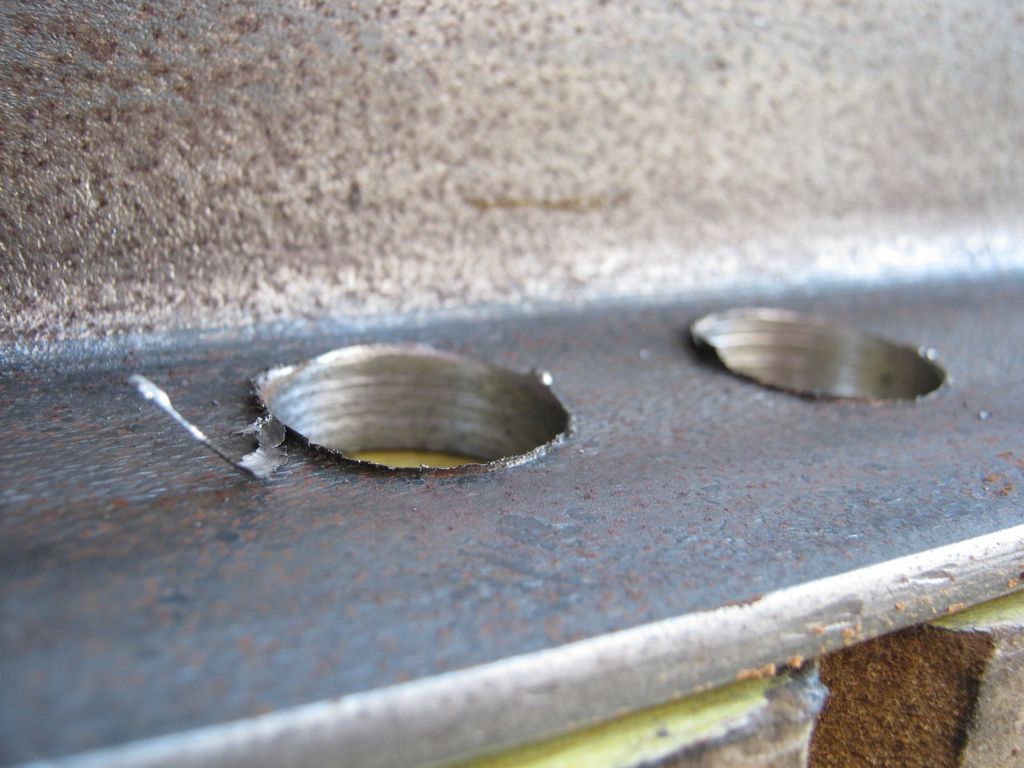
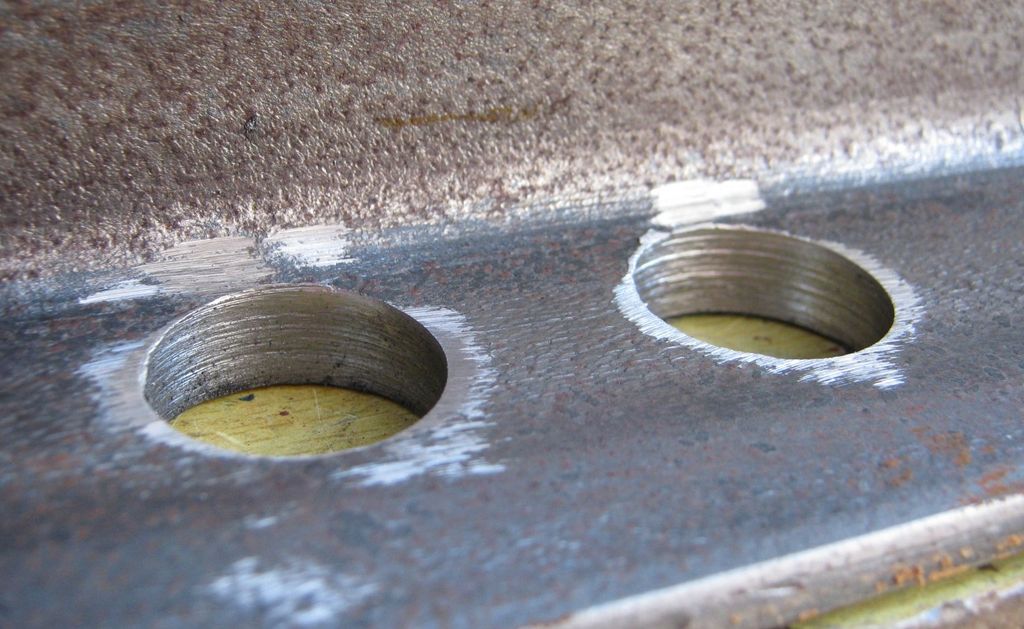
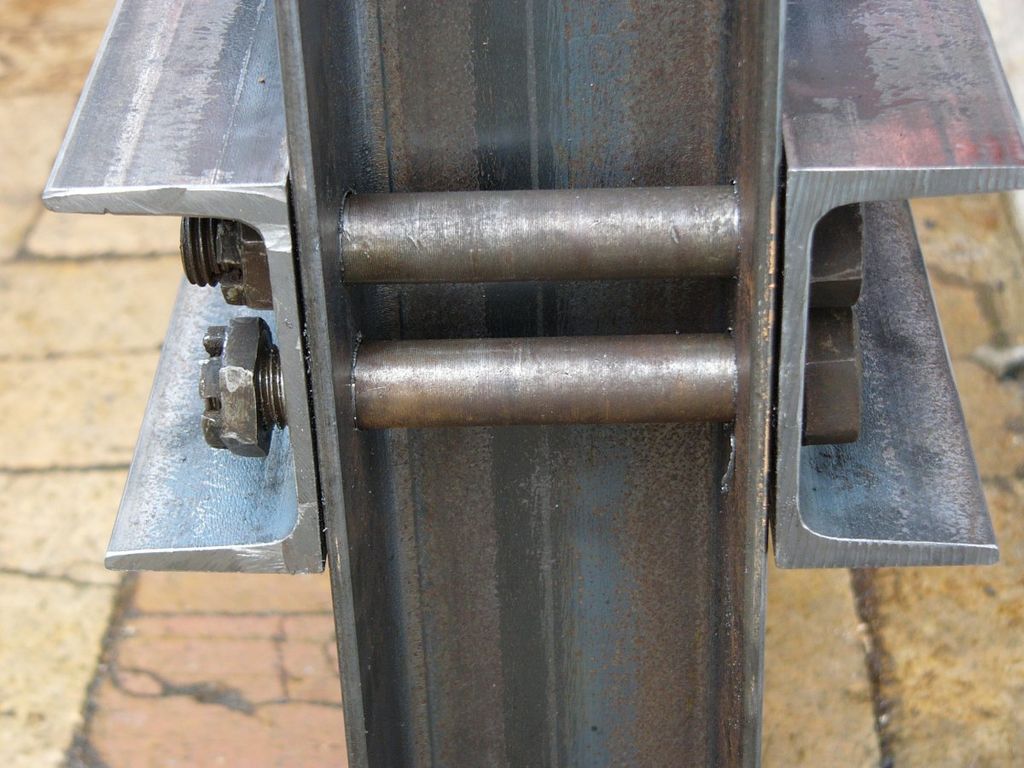
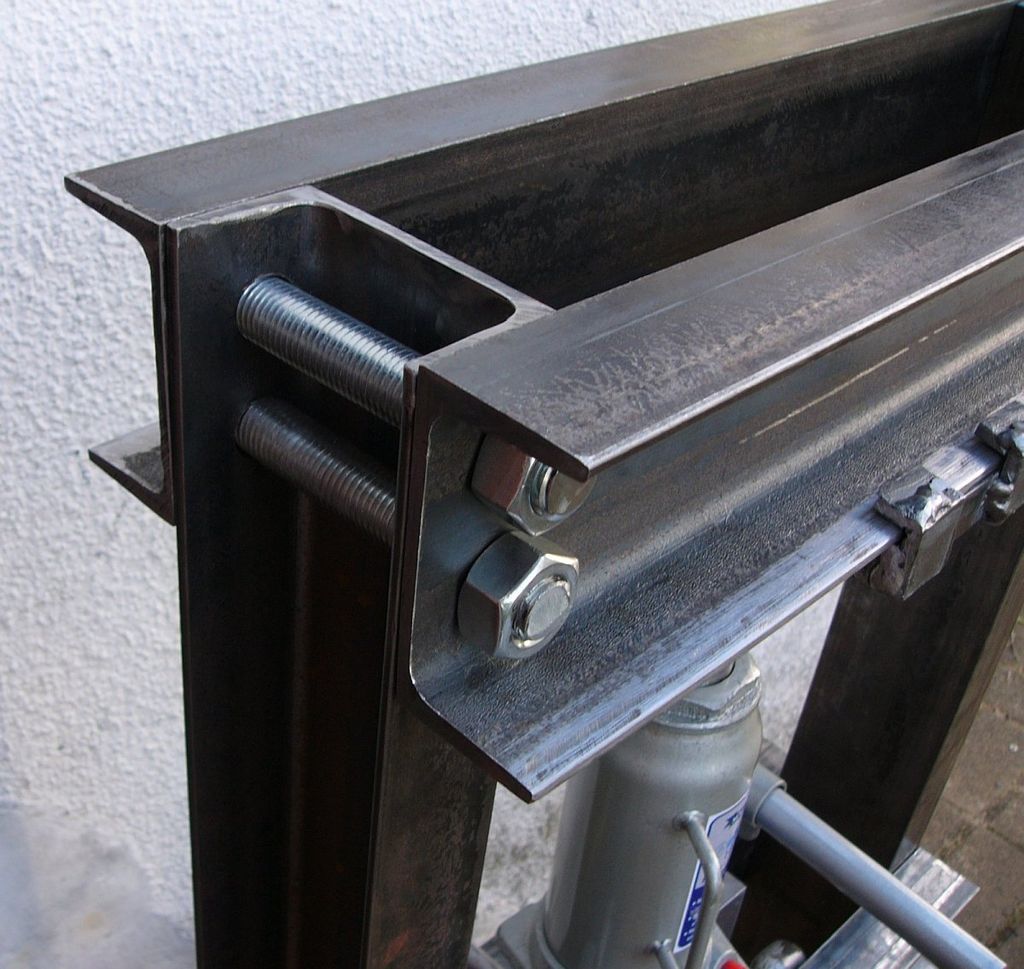
Биметаллическая коронка легко режет 8мм-вую сталь, и остается острой после прорезания 32 отверстий. С обратной стороны остается иззубренный край, поэтому перед покраской пресса метал нужно будет зачистить.
При сборке станины может оказаться так, что отрезки швеллера из-за уклона внутренних граней плохо стыкуются между собой. Это исправит шлифовка поверхностей в местах соприкосновения.
Отметив места сверления отверстий на расстоянии 30 мм от края перекладин, я пришел к выводу, что расстояние между центрами 39 мм гораздо удобнее для сборки, чем 40 мм, которые я планировал (100 мм ширина минус 60 мм общий вычет толщины вставки).
Файл с основными расчетами.
Файлы
Шаг 5: Скобы для стаканного домкрата
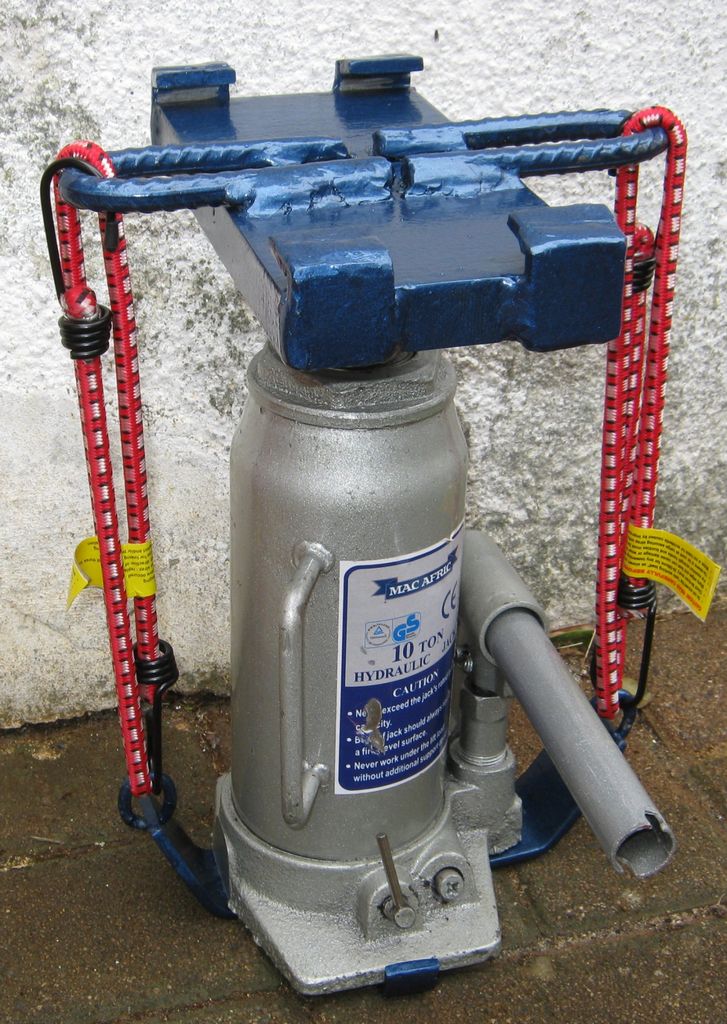
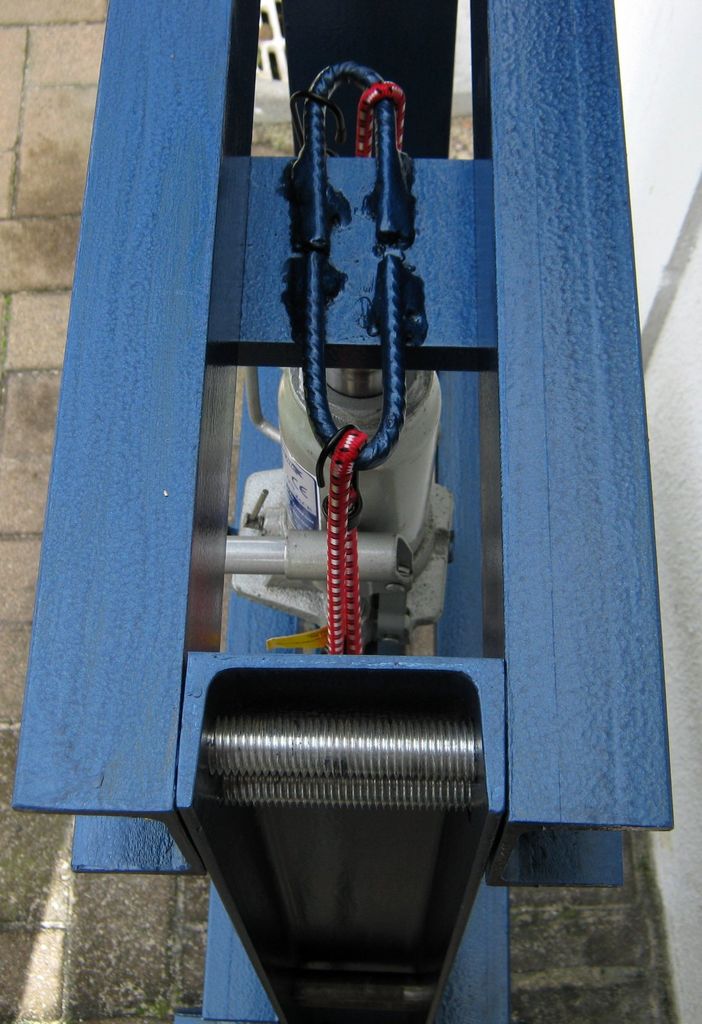
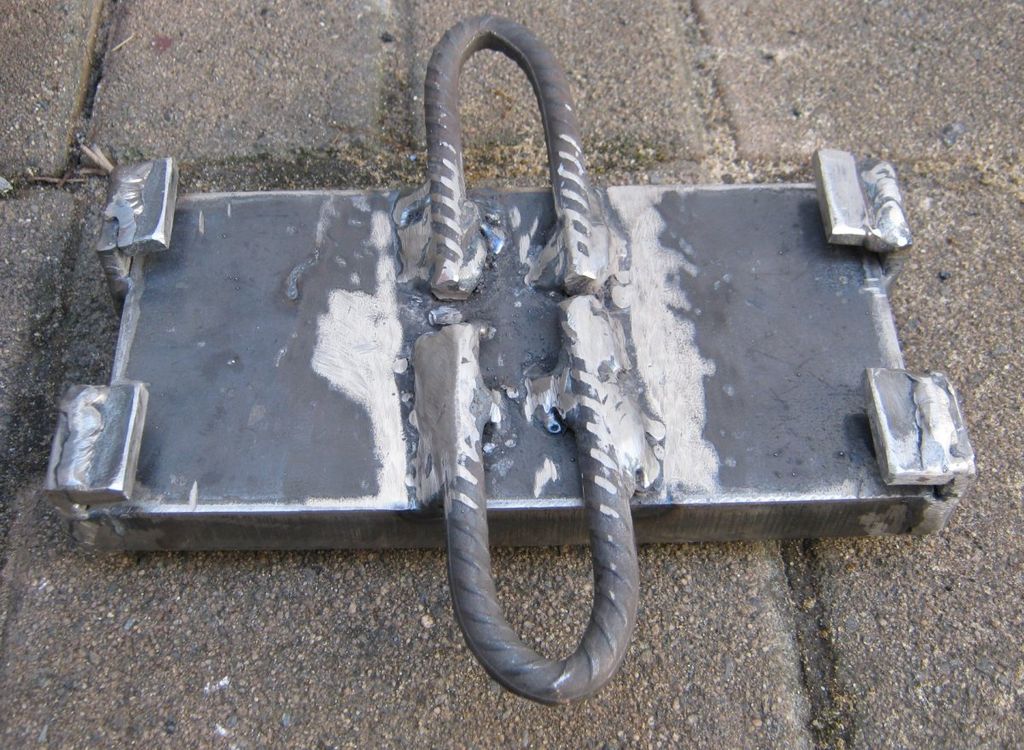
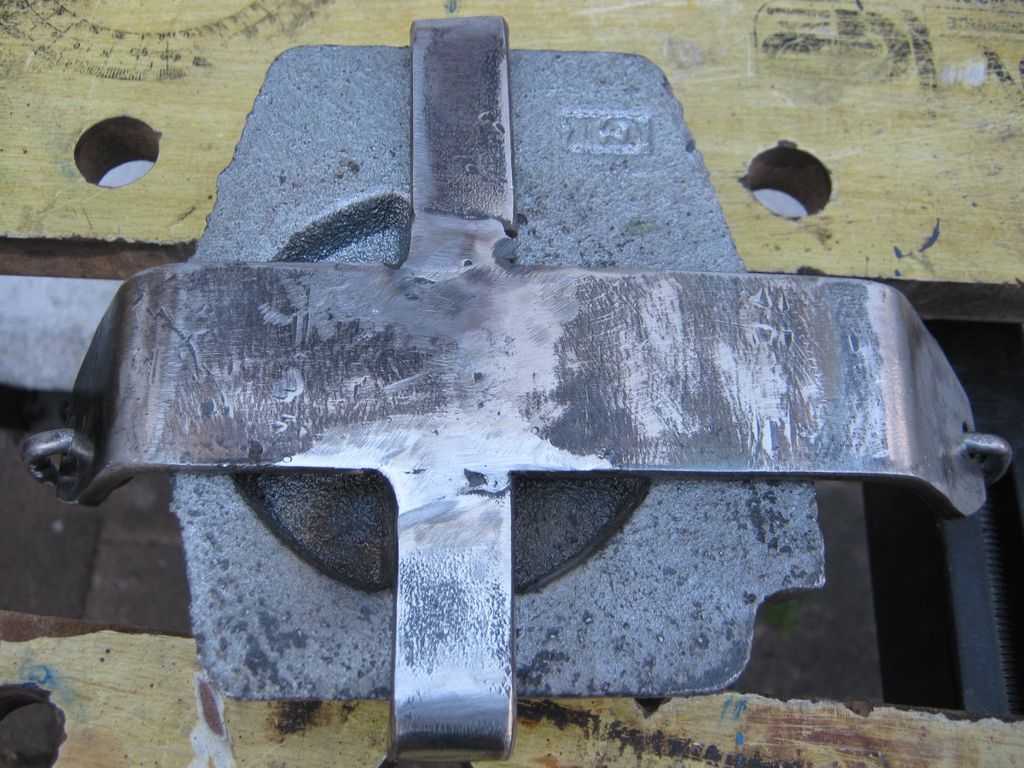
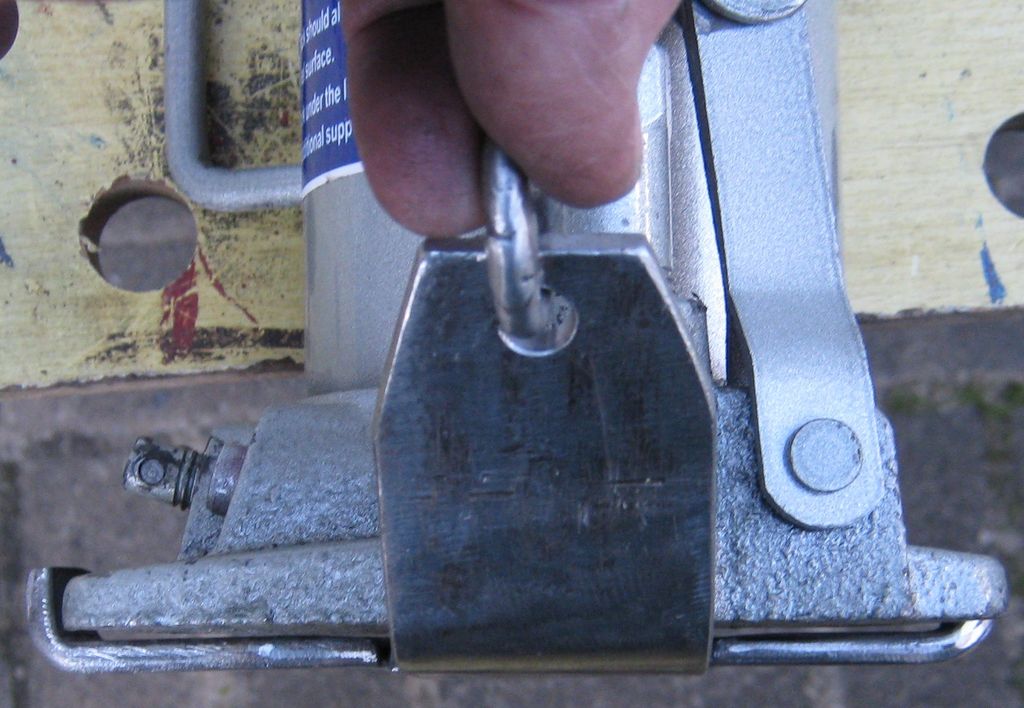
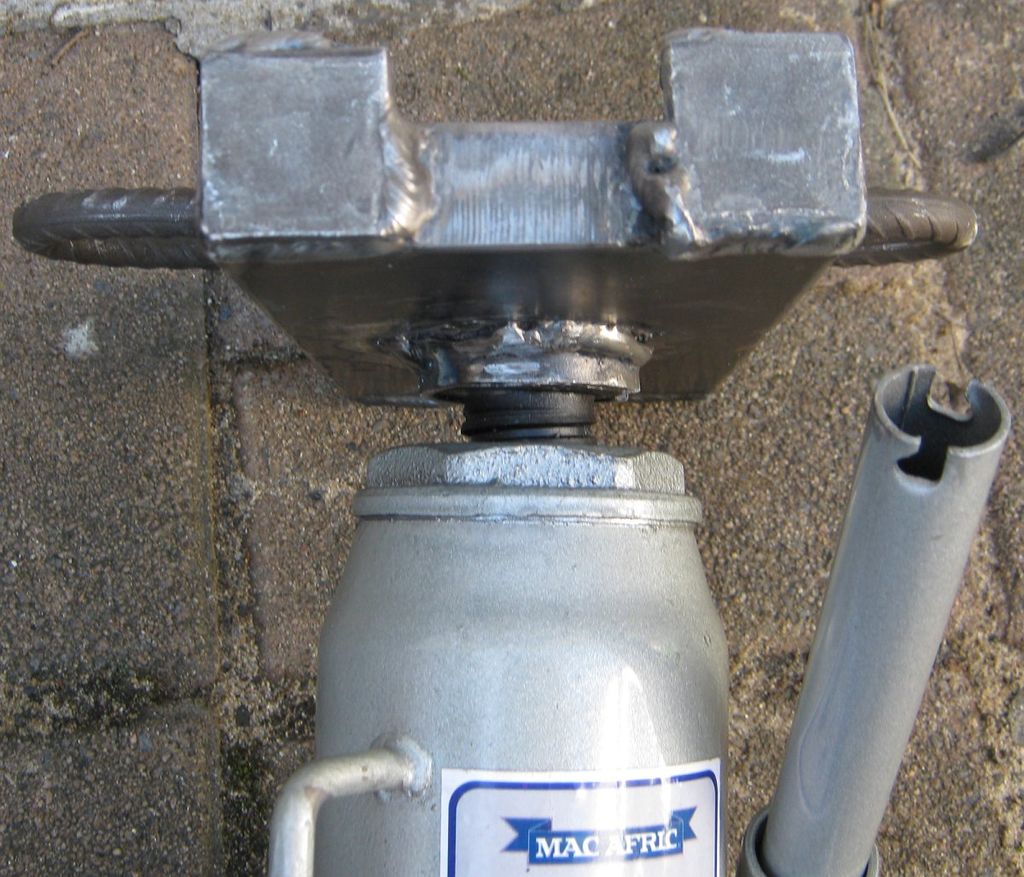

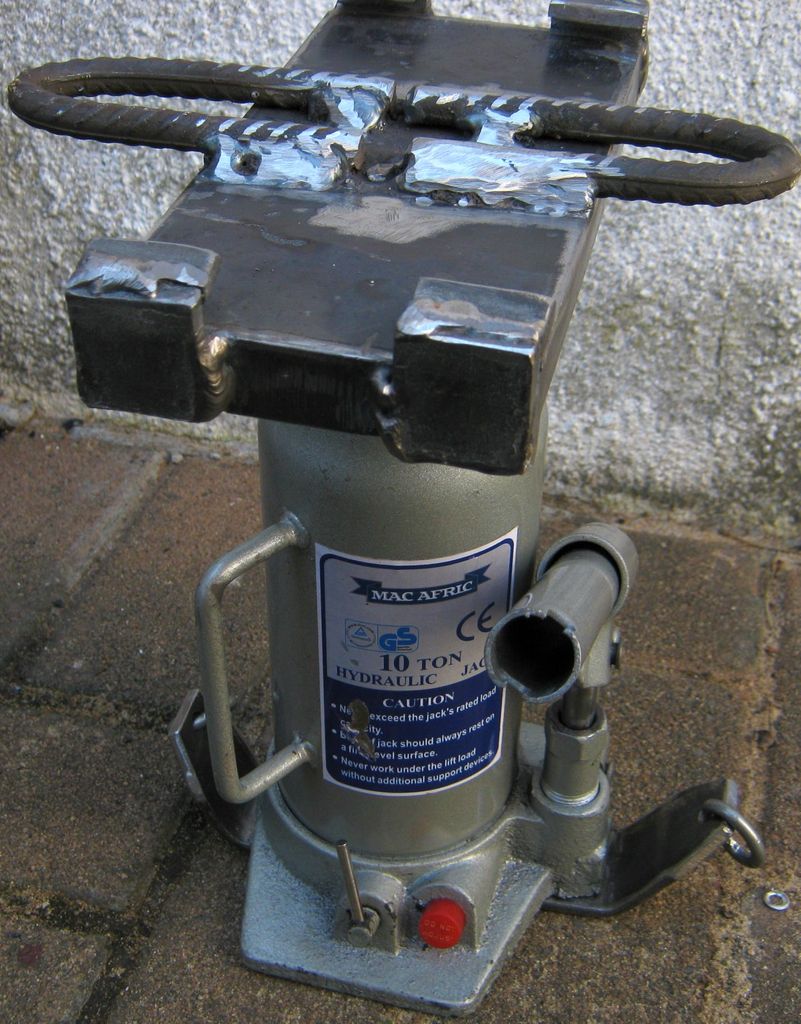
Я приварил отрезок трубы к верхней скобе, чтобы зафиксировать головку выдвижного винта домкрата, затем приварил два согнутых куска арматуры, для крепления возвратных пружин. Временно в качестве пружин используются эластичные тросы.
Нижняя скоба сделана из кусков ненужной стали, сваренных друг с другом и согнутых, чтобы удерживать основание домкрата. Пока я ищу подходящие пружины, эластичные тросы крепятся звеньями цепи.
Тросы маркированы предупреждением о недопустимости растяжения свыше 50% изначальной длины. Как можно чаще трос нужно проверять на повреждения, разлохмачивание оплетки. Не допускайте, чтобы лицо или части тела находились на пути растянутого троса, на случай возможного разрыва.
Шаг 6: Испытание
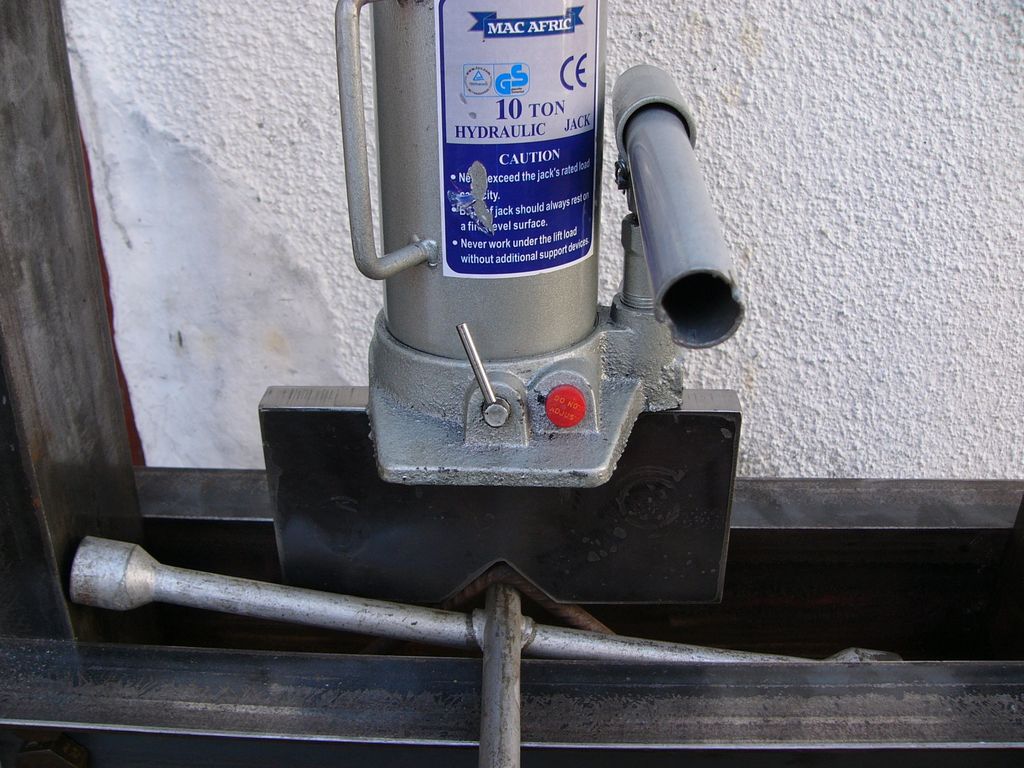
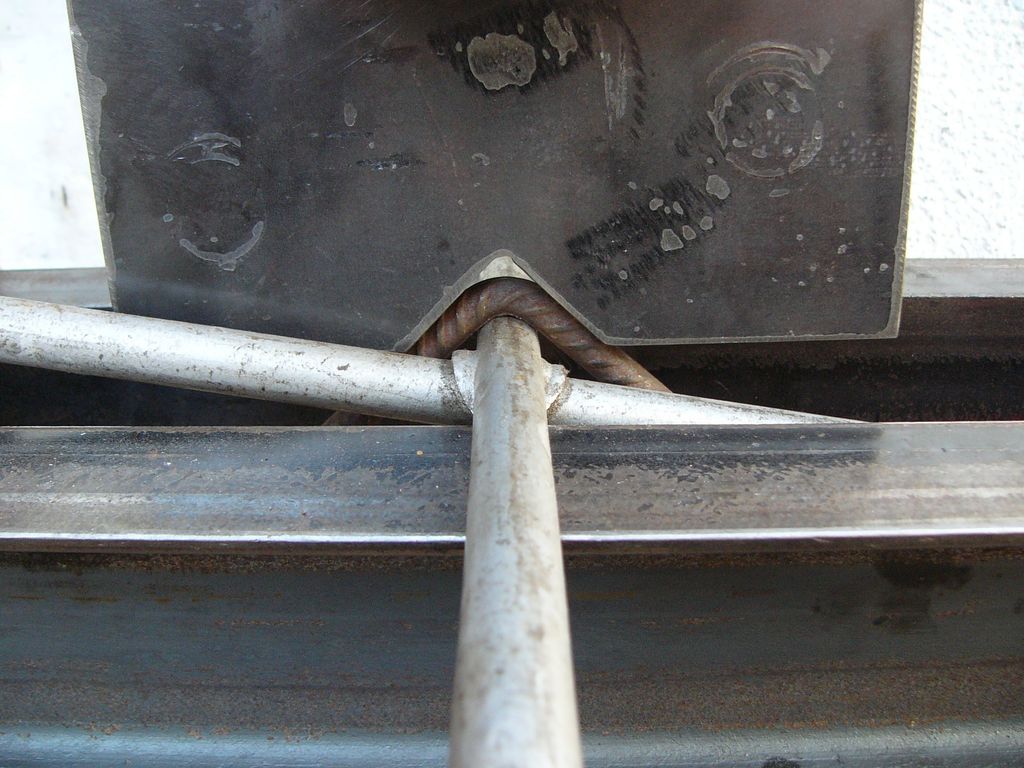
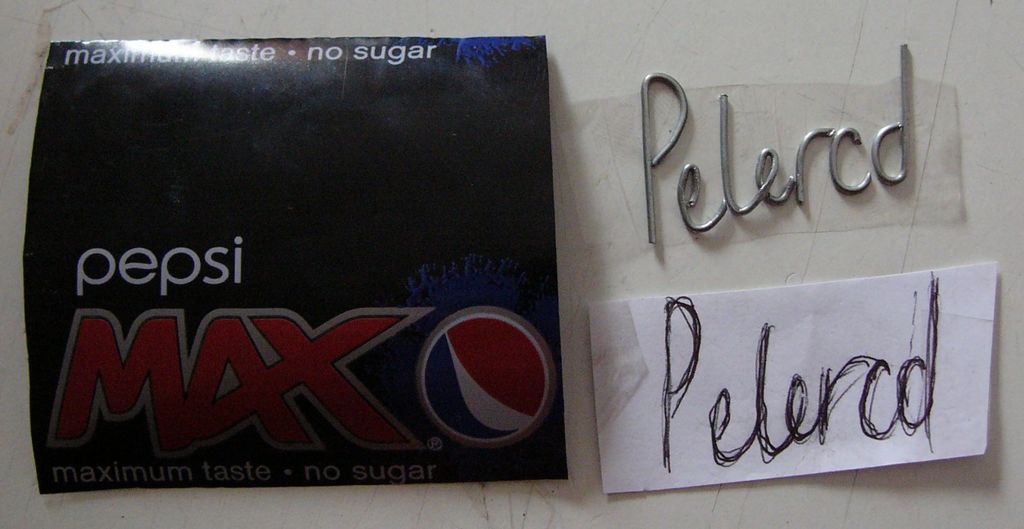
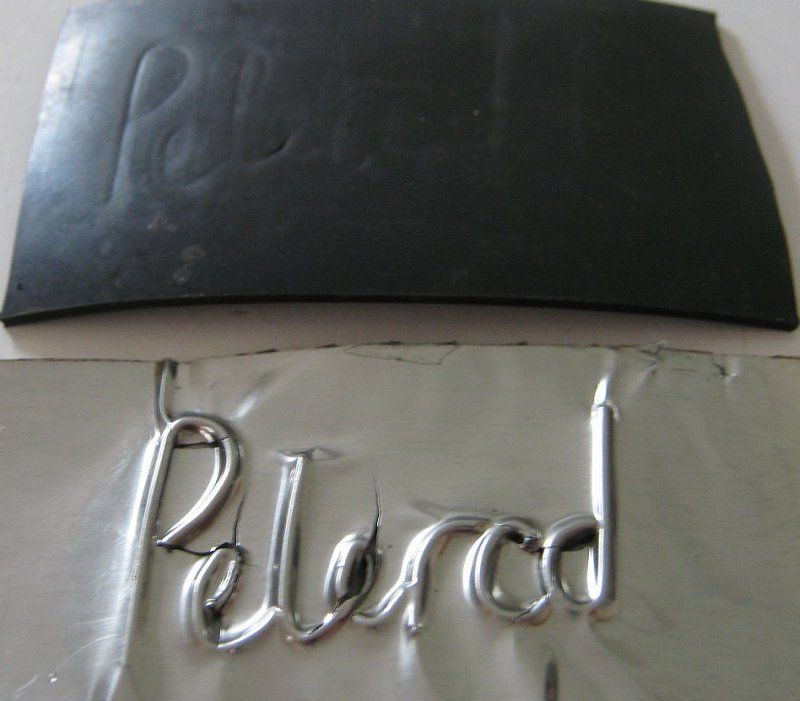
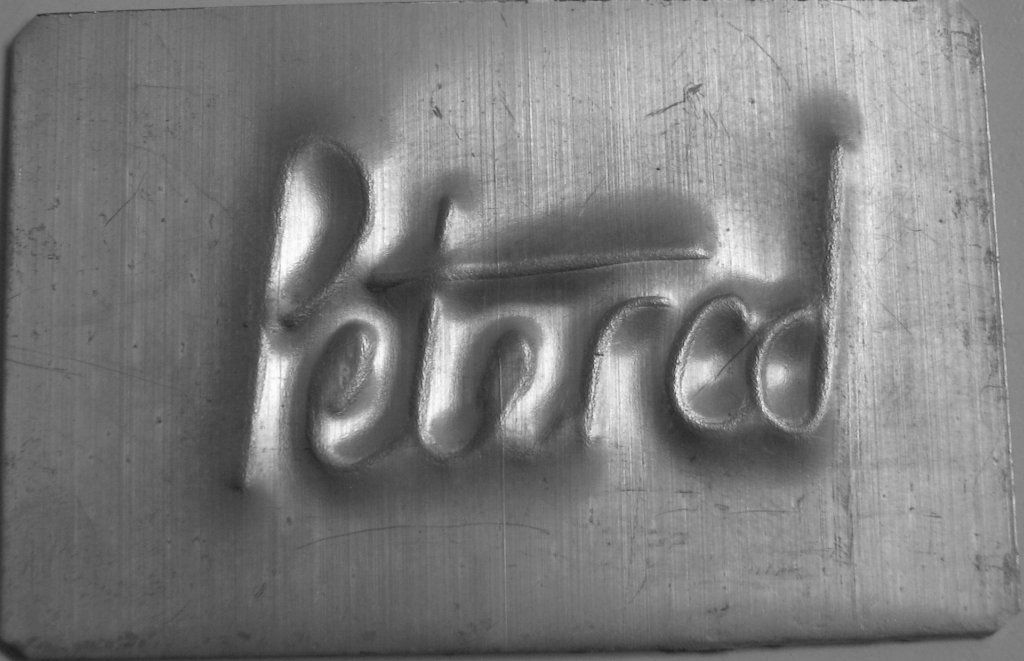
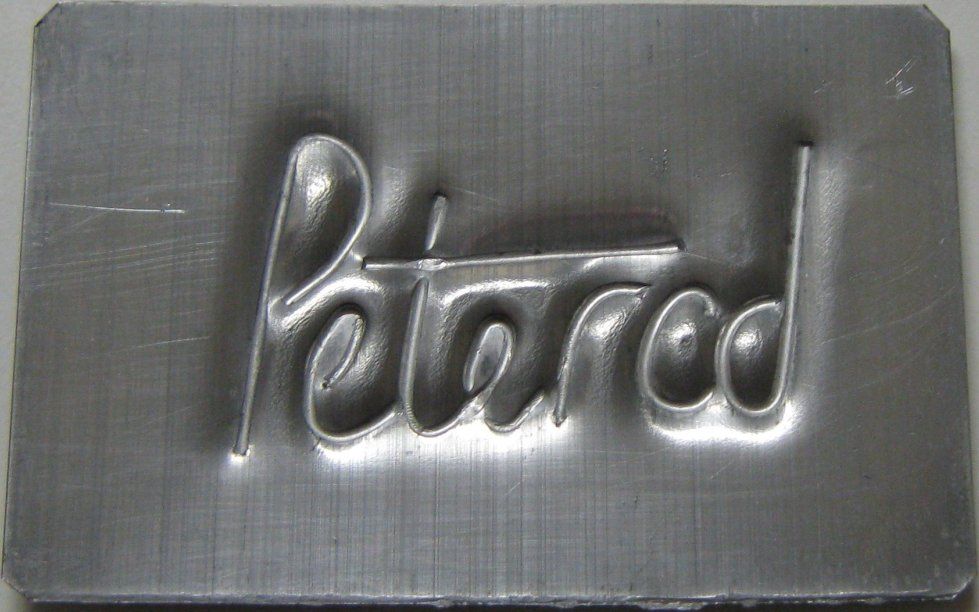
10мм-вую арматуру сгибает на отлично, до 90°. Для V-образного сгиба пришлось использовать дополнительно балансир и столбы от ограды.
Единственная модификация домкрата – замена штока на более длинный, для облегчения работы.
Я попробовал горячую штамповку, но имевшаяся у меня алюминиевая банка не выдержала испытания. Возможно, нужно взять или более толстый металл, или более тонкую проволоку (я пробовал с проволокой 1,23 мм).